核废料钢桶制造工艺研究
文/赵光曦
摘要:对某规格新式核废料桶的制造过程进行研究,介绍废料筒各组成部分的制作方法,重要尺寸的保障工艺。
关键词:核电站; 放射性废物;核废料桶
随着全球经济发展,传统能源方式已经不能满足工农业发展和人民生活的需要,核电作为一种清洁高效的能源形式已经被广泛运用,并逐步成为人类能源供给的主要形式。我国的核电技术起步较晚,据统计2018年核电在我国总发电量中占比仅为4.2%,而美国和欧盟各国在2017年时核电占比就到达了20%和25.6%,其中法国更达到了惊人的75%,成为该国最主要的能源形式。目前在我国的能源结构中火电仍占主要地位,然而矿物燃料的大量燃烧造成的酸雨、雾霾、温室效应等环境问题已经严重影响到我国的生态建设,不符合“美丽中国”的发展要求。为应对日益严重的环境问题,政府正逐步加快核电机组的审批和开工速度,预计到2030年提高我国核电占比到发达国家的平均水平。这就意味着,到2030年前,平均每年需新开工建设百万千瓦级核电机组八台左右。
核电站的广泛建设伴随着越来越多的放射性废料的产生,核废料桶作为放射性废物的存放、运输、后处理的容器形式,以其清洁、环保、安全、高效的特点已经成为世界核电站放射性废物处理的主要消耗品。以日本为例,平均废物产量为600~700桶/年,截止上世纪80年代末,日本第一福岛核电站储存的废物就达到了25万桶。随着“一带一路”倡议的实施和我国的“华龙一号”机组在世界范围内的应用,巴基斯坦、阿根廷、南非等越来越多的发展中国家的核电站也将成为核废料桶的主要使用者。因此,在可预见的未来,核废料桶在国内外核电产业的发展中有着广阔的市场前景。
由于核辐射会对人体产生伤害,在对放射性废料的处理过程中将采用高度自动化的生产线,保证全过程无人参与。核废料桶将在完全自动化的生产线中完成转移、运输、放置废物、后处理等过程,这就对桶的外形尺寸、力学性质、强度、稳定性等有严格的要求,稍有超差项就会对生产线的检测元件产生影响或者执行机构无法达到工艺效果,造成不良的后果。因此,各核电站对核废料桶制造精度都有着严格苛刻的要求,作为制桶业的高端消费品其经济价值和实用价值不言而喻。
本文以160L核废料桶为例,分别对各个组成部分的生产过程进行研究,有助于了解核废料桶的生产工艺,对开发其他形式、尺寸规格的桶型具有参考指导意义。
1 外形及各部分组成
目前,全世界核电站使用的主要桶型的尺寸规格为400L、200L、170L,而160L桶作为一种更符合我国国情的新式桶型只有少数企业可以生产。随着我国能源产业结构的不断升级和“一带一路”倡议的延伸,160 L桶也将逐步应用到各个新建核电站的废料处理中,其市场前景相当可观。
160L钢桶由桶盖、筒身部分和桶底组成(见图1)。废料桶的桶底与桶身通过氩弧焊连接,桶身桶口处经过翻边处理与桶盖的外径配合(见图2);在运输和存放过程中,桶身与桶盖分开放置,在使用时,将桶盖压入桶身中,利用接触面的圆形凸起部分与桶身产生塑性变形一次性把合固定,形成不可分割的整体,以保证放射性废物在转移、处理过程中不会泄漏(见图3)。在桶身的中部利用钢板自身褶皱变形增大截面的刚度,其作用相当于两道“加强筋”,大大提高了桶身横向抗压强度,保证桶底焊接、配合桶盖过程的精度及运输使用过程中抵抗变形的能力。

图1 160L钢桶外形图
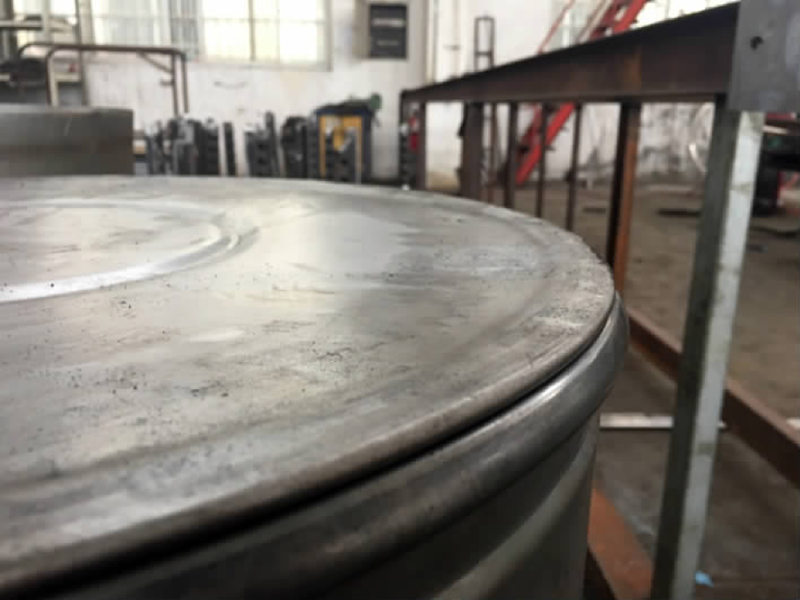
图2 桶口与桶盖配合处

图3 桶底与桶身点焊定位
2 桶底的制作
为提高材料的利用率,减少浪费,根据桶底的目标直径和拉伸高度计算毛坯的合理直径,切割成圆形的桶底毛坯(见图4)。
将桶底毛坯放入桶底模具(见图5)内,通过压力机一次压制成形。在压制前可以在毛坯面涂抹拉伸油,防止因摩擦过大撕裂板材。
在某些情况下,废料桶在使用中要在桶底穿刺以排除桶内残留的液体。因此,底部穿刺区域的位置和高度是制作桶底的重要尺寸。穿刺区域离桶底支座太近会使穿刺区强度过大,穿刺机构无法穿透桶底,造成“穿不动”;离支座太远又会因穿刺区刚度过小使桶底变形量过大超出穿刺机构的有效行程,造成“穿不透”。经过多次试验分析,160L桶型穿刺区选取在距支座处8~17mm范围为宜。
此外,在不影响使用的情况下应尽量使穿刺区域靠近桶底面以增大穿刺机构的有效行程,保证穿刺质量。通过试验,取距桶底支座处的垂直距离不超过5mm为宜。
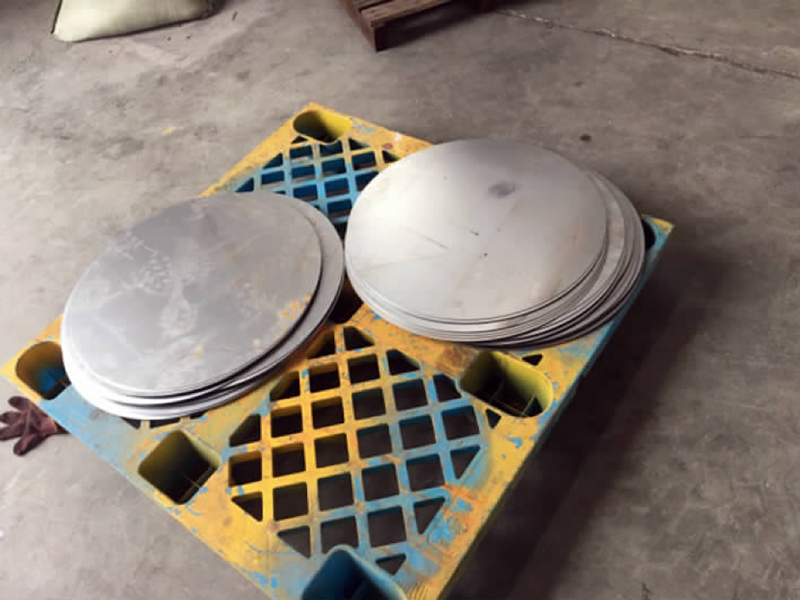
图4 桶底毛坯
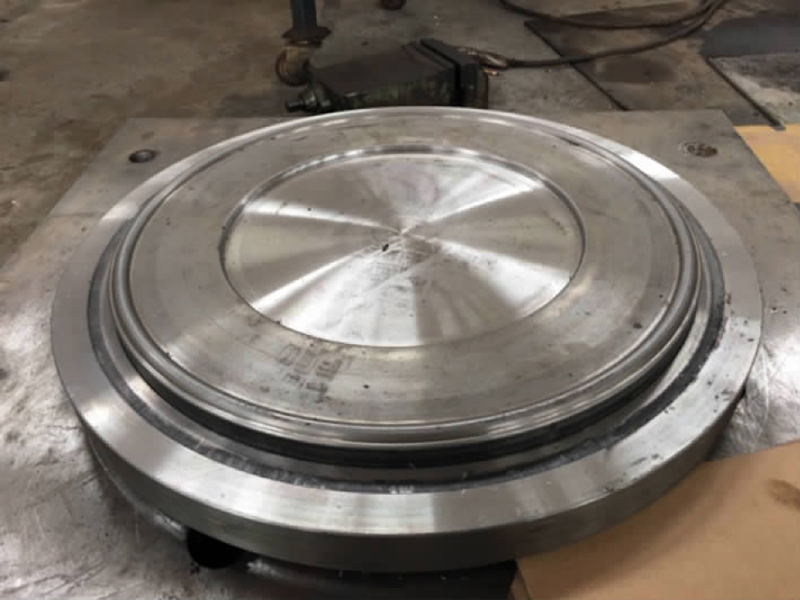
图5 桶底模具
3 桶身的制作和焊接
首先,根据图纸尺寸及焊接、切边翻边量等工艺确定裁板的尺寸;成品桶的直径由板材长度决定,桶高由板材宽度经过切边、翻边、剪裁后确定。
剪裁好的板材通过卷板机达到需要的桶身弧度后焊接成桶(见图6);焊接好的桶身在滚筋机上通过上下模具的挤压在桶口、桶身两处形成三道加强筋。滚筋机构造:滚筋机通过电机驱动导链带动上梁转动,达到“滚动”的目的;根据滚筋设计位置在上梁和下梁布置凸模和凹模,通过液压系统压下上梁使凸模和凹模达到合理的间隙,在滚动和压下的合力作用下达到滚筋的效果。在滚筋过程中压下和滚动动作的配合是成功的关键,通常情况下是“边滚动边压下”直到达到需要的间隙使得桶身的褶皱逐步形成,如果先压下到位后再开始滚动则容易造成桶身滚动中“跑偏”,使得产生褶皱的位置发生移动造成滚筋失败。
桶身桶口由于与滚筋机挡板挤压磕碰往往会形成“波浪边”,需要通过切边翻边机对桶口处的形状和尺寸重新加工;完成上述工序后测量总高,在桶底处剪去超差的高度,得到最终的桶身形式(见图7)。
在整个制桶过程中桶高是十分重要的尺寸,直接关系到能否保证运输转移过程的顺畅无卡阻,以及检测元件是否能正常检测到桶的准确位置。因此,在焊接桶底和桶身时必须复测桶身高度。为保证焊接位置准确可靠,可以制作焊接工装(见图8)以调整桶底桶身到指定的焊接高度点焊固定后,再取下工装焊接。
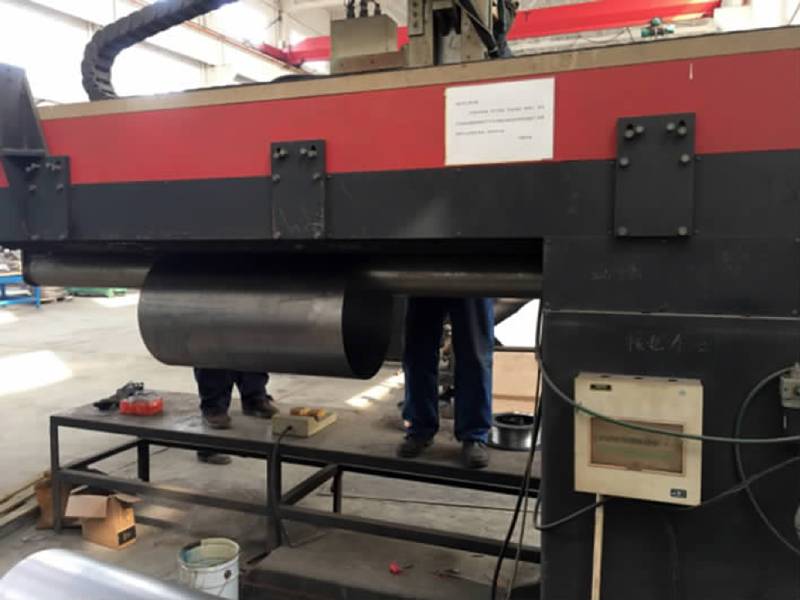
图6 桶身焊缝焊接
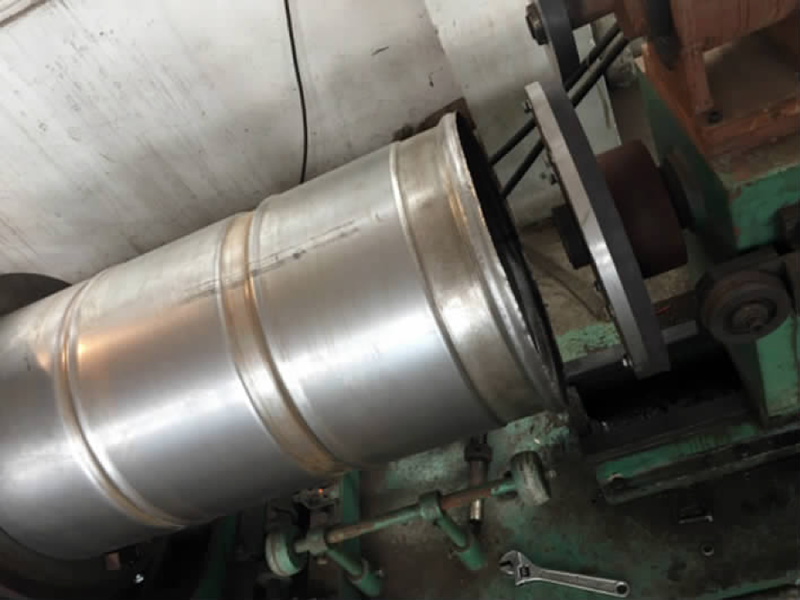
图7 桶身剪边翻边机

图8 焊接工装
4 桶盖的制作
桶盖的制造工艺与桶底相似,不同点在于:桶盖的构造相对复杂,首先,需要在边缘压出褶皱与桶身的翻边尺寸配合,这就要求材料在压模过程中有更大的拉伸量;其次,为达到与桶身固定的目的需要在拉伸面冲压出“凸起”以把和桶身。经过试验分析:一次压制成形很难达到拉伸、压形、冲压的效果,而是需要三次压模过程。剪裁好的圆形板材通过第一次“拉伸过程”的作用得到足够拉伸量的桶盖毛坯(见图9);通过二次“成形过程”的作用形成边缘褶皱,表面带筋的成品桶盖;再通过第三次“冲压过程”在桶盖与桶身的接触面通过手动冲压机(见图10)等距离压出十个“凸起”,达到把合桶身的作用。
为保证第二次压模的质量,需要在压力机与上模间垫两层牛津块(见图11),使上、下模接触后仍有进一步压下的空间,以形成桶盖边缘的褶皱构造。
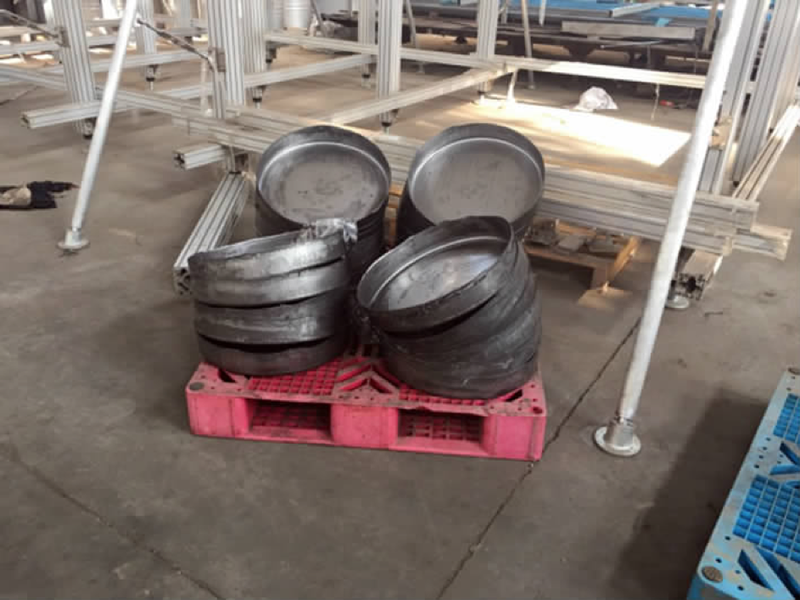
图9 一次成型的桶盖毛坯

图10 手动冲压机模具
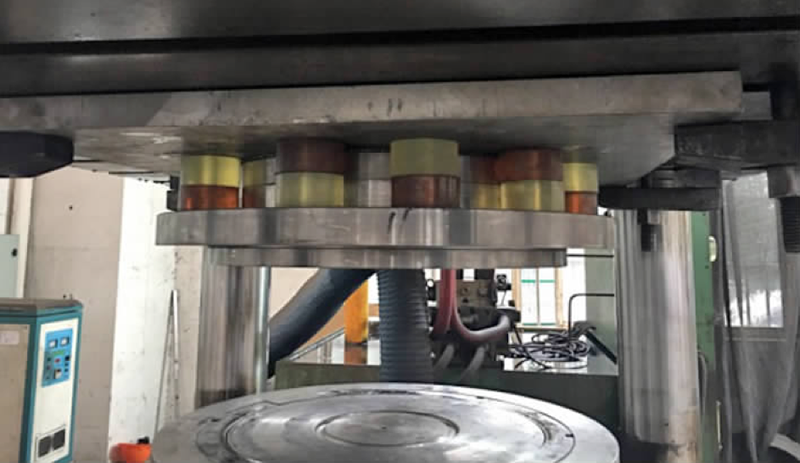
图11 桶盖二次压模模具
5 结语
本文以160L桶为例,从桶底、桶身、桶盖的制作、焊接,重要尺寸的保障等方面介绍核废料桶的制造工艺,对于其他规格的桶有一定的借鉴意义。随着核电技术在世界范围内的广泛应用,各国对放射性废料处置及存放的要求将不断提高,高端核废料桶制造业也将向更加自动化集成化方向发展,推动制桶设备的不断升级和制造工艺的提高,在放射性废料处理领域将会有广阔的市场前景。
|