奥瑞金覆膜铁技术自主研发: 在技术封锁之下,为中国人争一口气
文/奥瑞金
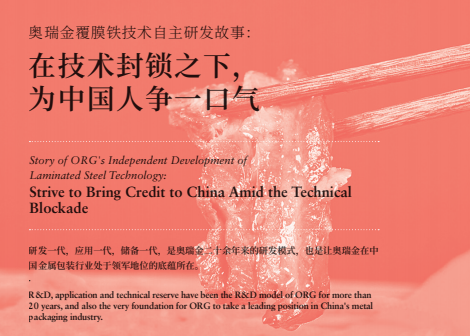
研发一代,应用一代,储备一代,是奥瑞金二十余年来的研发模式,也是让奥瑞金在中国金属包装行业处于领军地位的底蕴所在。
“暮色苍茫,声雷动,回肠气荡。望东海,宇楼空空,雨烟莽莽。波浪吞涯惊魅魉,云霞红天折峰嶂。待何往,凌顶众山旁,毋相忘。河水长,山丘砀。原野旷,灵泉杖。看貔貅天降,曜骧踏浪。采药君房宫下飨,鉴真东渡天平仰。守国疆,四海五洲强,苍穹攘。”
2013年,奥瑞金董事长周云杰填下这一阕壮怀激烈的《满江红》,看似自抒胸臆,实则另有深意——该年11月14日,奥瑞金就DR材、覆膜铁以及食品安全研发及应用推广在上海召开“技术研发项目应用推广研讨会”,邀请金属包装行业众多专家参会,并发布了奥瑞金自主研发的第一个覆膜铁罐。
那是一个小小的539#罐,但其份量却是沉甸甸的。自2007年正式调研立项以来,奥瑞金已在覆膜铁材料研发和应用之路上奔走了6年;如果把行业专家和科研工作者的探索也算在内,这一时间则可以回拨至更早的数十年前。
“所以那次会议多少带有一种向金属包装行业的专家们致敬的意思,”周云杰回忆,“我在会上掉泪了,因为我觉得我们没有辜负他们这老一辈人的期望——我们中国人真的把覆膜铁这个产品做出来了。”
当年国内最早提出和呼吁覆膜铁研发应用的章文灿教授也在参会之列,接受本刊专访时他回忆那一刻的心情“十分欣慰、感慨和兴奋”:“我对周云杰董事长说:‘你们有志气,讲科学,在别人严密封锁下,做出了第一个合格的覆膜铁罐,为中国人争气了’。”
男儿有泪不轻弹,能让两位在各自岗位上都有着不凡成就的先行者如此激动、感慨的覆膜铁究竟有什么不同凡响之处?独立自主研发这一金属包装新型材料,意味着什么?
对此,周云杰的答案是:“覆膜铁的研发成功,最重要的是展现了奥瑞金人乃至中国人敢于创新、敢于拼搏的勇气和精神。”
不搞出覆膜铁,死不瞑目
中国与覆膜铁的故事,可追溯到上世纪70年代。
当时罐头出口创汇是中国一项较重要的任务,要保证罐头产品质量,罐内涂膜与金属薄板的结合力即附着力这一技术难题,就必须得到解决。
由于职责所在,时任中国食品发酵工业研究院制罐及防蚀检测研究组组长的章文灿广泛搜索国际信息,发现美国西北大学教授T.E.Mullen发表的论文《金属与薄膜之间的附着力研究》中指出,其在实验室已实现了内涂膜与金属薄板之间的附着力实际达到1000公斤/平方厘米,并推论结合力的理想理论值,可以达到这个数值的10倍。
在亚洲,当时制罐业比较发达的日本,内涂膜与金属薄板之间的附着力,最好也只有100公斤/平方厘米左右;中国在这一数值上相距更远,一般只有30~40公斤/平方厘米。
因此,找寻提高附着力的方法,就成为保证罐头产品安全的重要任务。然而,这一过程不可谓不曲折——上世纪80年代,日本东洋制罐首先发展出覆膜铁技术,但对于前去日本参观交流的中方人员,日方对这一技术严格保密,不透露丝毫信息;中国希望向英国等欧洲国家寻求信息帮助,也被客气地拒绝。
“在世纪之交,眼看着别人的进步,难道我们中国只能墨守成规,不能迎头赶上?”作为相关技术的领头羊,章文灿首先提出:我国应该探索研究建立自己的覆膜铁生产线。他不断向各方面呼吁,并介绍这种新技术对我国的意义。“我懂得,中国除了自己研究苦干,别人是不会帮忙的。一提到覆膜技术,外国人就顾左右而言他。”
制罐企业,印铁厂家,大小钢铁公司,当时已快到退休年纪的章文灿一一游说,希望这些厂家能组织整合力量,实现覆膜铁技术的国产自主研发和应用,他甚至誓言:如果中国不搞出覆膜铁,我死不瞑目。
这句话,让周云杰大为震撼;而最终实现了章教授这一夙愿的,正是奥瑞金。
他们能干,我们也能
奥瑞金初次认识覆膜铁材料,是在上世纪90年代末。当时,奥瑞金为中国出口番茄酱提供制罐服务,最多时高达90%的出口番茄酱罐都出自奥瑞金之手。为了解决番茄酱罐耐腐蚀性等问题,奥瑞金延请章文灿作为技术顾问,并组织行业专家,成立专家委员会,对覆膜铁进行分析调研,同时与国际领先企业进行交流,深入了解覆膜铁的实践应用。
彼时,国际上只有日本及德国企业拥有相对成熟的覆膜铁技术,而仅有日本企业在应用端拥有相对完整的体系,国内企业只能以高价进口覆膜铁原材料及覆膜铁应用(制罐)生产设备。
改革开放 40 年来,中国庞大的市场为技术创新和应用提供了巨大的发展空间,正是蓬勃的中国市场培育了中国企业敢于创新的动力。
2006年,周云杰带队前往一家日资企业的在华工厂进行谈判,希望就覆膜铁技术在中国的应用开展合作。“我记得上午谈得还是非常愉快的,中午还一起吃饭,喝酒,祝贺双方谈判成功,”结果下午回到谈判桌,日方拿出正式合同,周云杰傻眼了:“我们谈的是花600万美金购买这一技术在中国的使用权利,结果合同上还有三个条款:1、只能使用该公司产品;2、不能自行研发该产品;3、不能使用第三方或与第三方合作开发该产品。”
如果接受这些条款,原本的“技术引进”就会变成“技术封锁”,“相当于我们花了600万美金买了一套枷锁,这显然是我们根本无法接受的”。
谈判戛然而止;但周云杰至今忘不了日方人员的傲慢,“摇着小扇子,对我们不屑一顾的样子”。失望郁闷的周云杰一行晚上在一家日料馆吃饭,大家都喝得有点多,当时奥瑞金的工程技术负责人赵宇辉忽然说话了:“我们自己干——给我5000万,我就干!”
他的理由很简单:“日本人能干,我们也能。”
5000万并不是一个小数目,几乎相当于当时奥瑞金大半年的利润。周云杰想了想,答应道:“好,豁出去了。”
“但是这5000万也可能打水漂。”赵宇辉不忘给周云杰“打预防针”。
但周云杰心意已决:“打水漂也干,要不然就彻底没有机会”。
“这个事情我们不做,就没有人驱动行业去做”,日后,周云杰如此解释奥瑞金“赌上一口气,自己研发”的原因。“中国的产品想要在市场上占有一席之地,仅靠原有的技术是不行的,必须要承担风险往前走。虽然当时奥瑞金还没有上市,整体来看资金处于比较紧张的状态,但是我们在整个制罐行业中利润已经是最好的,具备承担风险的基础,所以我们敢于创新,主动承担责任。”
此外,他有着更大的底气:“改革开放40年来,中国庞大的市场为技术创新和应用提供了巨大的发展空间,正是蓬勃的中国市场培育了中国企业敢于创新的动力。”
最难的,是坚持
2007年,奥瑞金开始覆膜铁项目的调研立项,2009年完成立项,正式自主开发覆膜铁材料。赵宇辉、陈玉飞接连担起项目主要负责人。
奥瑞金在上海成立了产业技术开发小组,与高校合作组建高分子团队、建设硬件基础,在合作单位的支持下,在实验室里首先用最简单的手工的办法来实验膜的配方,技术人员反复进行试验,积累大量数据进行配方的改进。
这是一个从零开始的尝试,“整个过程跟发明创造差不多,”赵宇辉说,由于日本对技术信息的严格封锁,奥瑞金只能照猫画虎地去做,“但能做到什么程度,谁都不敢讲。”此外,根据日本东洋制罐官方网站的介绍,其代表性的覆膜铁罐TULC(终极之罐)于1991年面世,研发投入巨大,“所以5000万能搞成什么样,我们当时心里其实是没有数的。”
直到初步开发工作完成——覆膜铁薄膜专用树脂合成、覆膜铁专用薄膜制备、热台手动覆膜、覆膜铁罐盖样品完成试加工,大家心里才终于有了底。
时间飞速流走,2011年6月,试验线机组调试完成,同年完成近150吨的罐/盖用覆膜铁样品的覆膜测试,还开展了应用技术的评估。2012年,定制的覆膜铁DRD罐试制线在北京工厂安装完毕,对加工DRD罐进行小批量应用验证,获取客户反馈及实罐数据,为覆膜铁材料的进一步优化提供技术支持。2014年,凭借近5年的不断开发测试及验证评估的积累,覆膜铁加工及应用技术日趋成熟,开始市场化推广。同时,在绍兴上虞建设的中试线产品也顺利下线。
2014年,“食品包装用覆膜铁的研究开发”项目荣获北京市怀柔区技术奖励一等奖,“浅冲食品用覆膜铁材料”荣获2015年度中国罐头工业创新大奖。从2016年开始,奥瑞金调整市场策略,聚焦客户、聚焦产品,进入稳步发展阶段。
周云杰表示,奥瑞金覆膜铁的研发应用有千难万阻,但其中有两点值得特别指出:“一是我们对覆膜铁技术和产品的认知,不仅在研发阶段,到了生产阶段,还需要不断提高对它的认识;二是市场规模过小,没有足够的生产量,你就无法发现生产中可能出现的问题。”
举例而言,“生产1000吨和生产2万吨覆膜铁完全不是一个概念。生产1000吨的时候实验做得好好的,什么事也没有,但可能到2000吨、3000吨的时候问题就出来了,而且很多问题是需要靠连续生产去发现和解决的,当时这个矛盾压得我们有点喘不过来气来。”
整个研发、投产过程,是一次次发现问题、解决问题的过程。在持续地实验、摸索、优化、调整的过程中,奥瑞金对覆膜铁的认识在不断地更新、提高。回忆整个研发故事,赵宇辉感慨最难的其实就是“坚持”。
“因为时间跨度太长,如何让大家对项目保持信心?遭遇失败后,如何让大家正确看待?需要不断给大家打气,不能气馁,不断尝试。而且中间还有人员的变化,有些技术研发的工作就会中断,还要找新人。但是现在回头来看,关关难过关关过,最重要的其实就是坚持下来。而这背后离不开公司领导层一直以来的耐心和支持。这个项目之所以到现在还在不断往前推进,跟周云杰董事长对公司的长远规划和对公司的信心是紧密相关的。”赵宇辉说。
至今,奥瑞金覆膜项目已经走过了15个年头,在研发上总计花费近2亿元。截止到2021年底,奥瑞金覆膜铁累计产量超5万吨,覆膜铁包装产品应用量超25亿罐,综合精品率达到97.83%。除此之外,奥瑞金覆膜铁技术已取得授权专利40余项,其中发明专利17项,一项荣获第十七届中国专利优秀奖,并主导制定了国家《食品容器用覆膜铁、覆膜铝》的相关标准。
“这是一个很大的成绩,也做到了为国争光。覆膜铁厂的建立使整个食品制罐行业的技术提升了一个台阶”,章文灿教授这样点评奥瑞金在自主研发覆膜铁技术上的贡献。
2020 年,随着国家“30·60”双碳目标的提出,低碳环保、节能降耗的生活理念深入人心,可持续也成为包装创新的一个重要主题。而覆
膜铁显著的优势恰好契合和满足了未来包装行业“智能、绿色、转型、创新”的发展趋势和要求。
研发一代,应用一代,储备一代
膜铁产品技术门槛和研发成本高,但初期的市场需求却不大,因此,奥瑞金的覆膜铁项目既考验前瞻的视野,也考验坚持的定力。
奥瑞金的选择是,“不要等风来,那时候再去研发就来不及了”,赵宇辉说。事实证明,奥瑞金“十年磨一剑”是对的,“从2010年开始,国家开始更加重视食品安全和绿色环保,行业也开始加大投入高精尖产品的生产,大的市场需求催生了对新技术、新材料的应用,这时候风就来了。”
义乌市易开盖实业公司是奥瑞金覆膜铁相关产品的重要客户之一,其副总骆江波早在2013年覆膜铁应用技术研讨会上就提出十分看好覆膜铁技术在行业的应用前景。接受本刊采访时,他表示目前公司应用覆膜铁技术的产品主要还是以蔬菜罐头和鱼类罐头为主,这源于覆膜铁在食品安全方面更有保障的天生优势。其有一个南美客户的高端产品,因为罐头内容物是高蛋白食物,需要高温杀菌,对罐头的制造工艺要求很高,是罐头里很难做的产品类型,需要抗腐蚀、耐高温且安全,而覆膜铁技术则完全满足要求。“使用了奥瑞金的覆膜铁罐头,客户很认可,基本上没什么投诉。”
2020年,随着国家“30•60”双碳目标的提出,低碳环保、节能降耗的生活理念深入人心,可持续也成为包装创新的一个重要主题。而覆膜铁显著的优势恰好契合和满足了未来包装行业“智能、绿色、转型、创新”的发展趋势和要求。
与传统涂料铁罐相比,覆膜铁DRD产品由于采用干式覆膜和制罐的干式冲压成型,因此省去了涂铁及制罐工程的清洗、涂装和烘干过程,具有节能、减排(废水,CO2和其他有害气体,以及固性废弃物)的特性。它可降低68.89%的能源消耗和69.95%的二氧化碳排放量,100%省去工业用水消耗,减少99.7%的固体废弃物,100%节省锡资源。
周云杰认为:“金属包装相较于其他形式的包装产品,环保是一大优势。如果回收工作做得好,可以达到100%回收及再利用。具体到覆膜铁,其中的覆膜涂料,在回收以及再生的过程中,并非形成废物废料,而是进行了一次价值转换。从回收乃至环保的角度看,无疑具有很大的优势。”
因为覆膜铁技术可满足蒸煮后附着力、不变色、好加工,以及根据内容物满足相应的抗酸、抗硫、抗盐等耐腐蚀要求,所以从灌装内容物角度,已经成功应用覆膜铁技术的包括燕窝、鱼胶、海参等高档补品,黄桃、桔子、椰果等水果,金枪鱼、茄汁沙丁鱼等海产品,芦笋、马蹄等蔬菜,辣椒酱、香油、牛肉酱等调味品。其他应用领域还有蛋白饮料、八宝粥、啤酒,等等。
奥瑞金也将覆膜铁产品应用在了自身的预制菜业务上。采用覆膜铁材料开发的奥瑞金碗系列,既能解决塑料袋、塑料盒等透气透氧效果不佳影响风味的问题,又解决软包产品运输破损的问题,做到只需将产品稍微加热就能享用美食。
“在食品包装领域中,如果覆膜铁产品有进一步的大发展,那么奥瑞金作为金属包装领域的上市企业、覆膜铁较早的研究者和探索者,更应该体现行业担当,承担更多的社会责任。”中国罐头工业协会理事长刘有千在接受本刊采访时表示。
当下,奥瑞金直面由于产业链协同深度不足、产量相对较低、应用端设备改造需要投入等方面的影响而造成的覆膜铁相较于涂料铁成本较高的制约因素,通过差异化产品的开发应用,最大化将覆膜铁的优势发挥出来,碗罐系列、啤酒罐顶盖、水果DRD罐等产品不断面向市场并引起瞩目,希望集整个行业之力共同应对挑战。
此外,奥瑞金项目团队也在不断收集数据,积累经验,推动覆膜铁的持续优化。赵宇辉认为,前面的路还很长,奥瑞金现在做的仅仅是第一步,“因为目前在运作的覆膜铁生产线还仅仅是个中试线,还在不断完善的过程中。而我们在日本参观的生产线,产能和自动化程度都非常高,生产品质稳定,能够适应各种各样的工况和应用,整个的产业链体系也很完整,所以他们适应产品的能力、产品改进的效率都要远远地高过我们。他们已经搞了40年,现在还在继续开发。而我们在国内是第一家,有着充分的先发优势。”
“奥瑞金要做的,不仅仅是践行行业领军企业的责任,更关键的是要在市场上保持永不落后。”周云杰表示,“研发一代,应用一代,储备一代,是奥瑞金二十余年来的研发模式,当市场有需求的时候,我们能迅速推出产品满足需求;当市场上出现了跟奥瑞金有同等技术水平的产品时,我们又能不断推出新的产品,背后的重要原因就是我们有技术储备——当你有10个概念性产品存放在技术档案里的时候,一旦市场有需求,你一延展马上就出来了。”
某种程度上,奥瑞金覆膜铁技术和产品正是这一模式的最佳体现,是让奥瑞金在中国金属包装行业处于领军地位的底蕴所在。
|