【专利】包装钢桶缩口机
文/国家知识产权局
申请号 |
|
CN01127882.X |
申请日 |
|
2001.09.26 |
公开(公告)号 |
|
CN1408620A |
公开(公告)日 |
|
2003.04.09 |
IPC分类号 |
|
B65D1/12; B21D41/04 |
申请(专利权)人 |
|
东莞振华制桶有限公司; |
发明人 |
|
车振华; |
优先权号 |
|
|
一、摘要:
包装钢桶缩口机,涉及包装容器生产设备技术领域,特指一种一次上料完成桶身的缩口、翻边、滚筋的缩口机。技术方案为:控制成型滚轮进退的进刀气缸与成型滚轮连接。本发明可以将成型速度由凸轮进刀方式的3-4只/分钟提高到7-8只/分钟,最高可达9只/分钟;可以缩口出表面无痕迹的缩口,外观圆滑、美观,便于后续的表面处理、喷涂、印刷;在成型的过程中,不容易出现板材变薄的现象,极大地降低了成本,而由于将三道工序结合在一起一次完成,节约了生产空间及设备的花费。
二、权利要求书
1、包装钢桶缩口机,包括:机身(10)、电机(20)、减速箱 (30)、成型滚轮(40)、顶紧气缸(60)、顶紧盘(70)、成型模(90), 机身(10)上连接电机(20)、减速箱(30)、顶紧气缸(60);电 机(20)输出轴经减速箱(30)后连接成型模(90),顶紧盘(70) 连接顶紧气缸(60);其特征在于:控制成型滚轮(40)进退的进 刀气缸(50)与成型滚轮(40)连接。
2、根据权利要求1所述的包装钢桶缩口机,其特征在于:成型模(90)的滚筋模(901)、翻边模(902)套于减速箱(30)的 输出轴(301)上,位于滚筋模(901)、翻边模(902)间的弹性元件(903)通过内衬(905)与输出轴(301)相套接,并在弹性元件(903)外圆上套有缩口模(904);滚筋模(901)、翻边模(902) 与缩口模(904)相接的一侧各凸伸一环(9011)、(9021),缩口模 (904)的内圆端亦凸伸有一环(9041)。
3、根据权利要求1所述的包装钢桶缩口机,其特征在于:控 制缩口机动作的PLC控制部分(80)连接于机身(10)上。
三、说明书
包装钢桶缩口机
1、技术领域:
本发明涉及包装容器生产设备技术领域,特指一种一次上料 完成桶身的缩口、翻边、滚筋的缩口机。
2、背景技术:
缩口广泛运用于包装钢桶的生产中,作为钢桶成型过程中的 一道重要的工序,对钢桶端部进行不同直径变化的缩口,有利于满 足集装箱满载运输的要求,提高钢桶强度,增强圆整性,利于后续 处理;良好的缩口将会极大地提高出口钢桶适于长距离海运的要 求;同时,赋予钢桶优良的外观,提升产品档次和竞争力。
目前,国内大多数生产厂家采用的缩口都是单一的对桶口或 桶底进行缩口,不能实现缩口、翻边、滚筋在同一台缩口机上完成, 而且,缩口时均采用凸轮控制的靠模方式完成;这样一来,复杂的 传动机构使得设备占用场地大,凸轮的进刀速度很慢,导致生产速 度只能达到3-4只/分钟,且缩口部分的外观质量不良,有多道环 向的成型痕迹,外观看起来加工很粗糙。
此外亦有部分厂家将缩口、翻边、滚筋三道工序在同一机器 上实现,其结构如专利ZL 92203895.3中所述,具体结构见附图1、2,由机身1、传动装置2、3、气动装置4、压紧机构5、胎模6、翻边滚轮7、波纹滚轮8、缩口滚轮9、翻边凸轮10、波纹凸轮11、缩口凸轮12、凸轮支架13、机械手14组成,胎模6上设有翻边、 波纹、缩口三个模印,凸轮支架13上设有与胎模6相对应的翻边、波纹、缩口凸轮10、11、12,此三个凸轮同时控制机械手14上的 翻边滚轮7、波纹滚轮8、缩口滚轮9的上升和下压;当工件套于 胎模6上后,打开气动装置4,使压紧机构5向前运动,直至凸轮 支架13带动翻边凸轮10、波纹凸轮11、缩口凸轮12同步运转,随着凸轮各自的升降变化,机械手14上连接的滚轮相应的上升或 下压,当与胎模6上的模印相吻合后,则停止传动装置2、3,开启气动装置4,取下工件即可;此种结构,由于是凸轮带动滚轮,通过靠模方式实现一台机器上的翻边、波纹、缩口,存在由支架到凸轮,再到滚轮的多重运动传递,使得成型速度缓慢,生产效率低, 控制精度不高;而且,波纹外翻,无法满足集装箱满载运输的要求。
3、发明内容:
本发明的目的在于提供一种一次上料完成缩口、翻边、滚筋, 生产速度快,质量好,适于集装箱满载运输的缩口机。
本发明是通过如下技术方案实现的:控制成型滚轮进退的进 刀气缸与成型滚轮连接,所述的成型模的滚筋模、翻边模套于减速 箱的输出轴上,位于滚筋模、翻边模间的弹性元件通过内衬与输出 轴相套接,并在弹性元件外圆上套有缩口模;滚筋模、翻边模与缩 口模相接的一侧各凸伸一环,缩口模的内圆端亦凸伸有一环;控制 缩口机动作的PLC控制部分连接于机身上。
本发明成型滚轮由进刀气缸控制其进退,而进刀气缸、进刀 气缸等的动作都由PLC控制部分实现自动控制,极大地提高了成 型的速度,利用本发明可以将成型速度由凸轮进刀方式的3-4只/ 分种提高到7-8只/分钟,最高可达9只/分钟;通过缩口模的偏心 旋转,以及滚筋模、翻边模间的配合,可以缩口出表面无痕迹的缩 口,外观圆滑、美观,便于后续的表面处理、喷涂、印刷;在成型 的过程中,不容易出现板材变薄的现象,极大地降低了成本,而由 于将三道工序结合在一起一次完成,节约了生产空间及设备的花费。
4、附图说明:
下面结合附图对本发明进一步说明:
附图1为现有缩口机结构示意图;
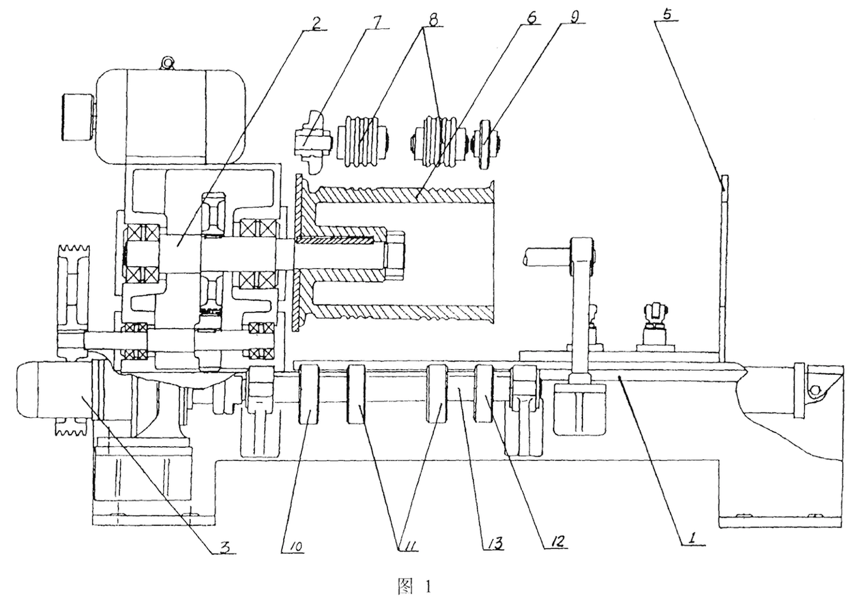
附图2为现有缩口机俯视图;
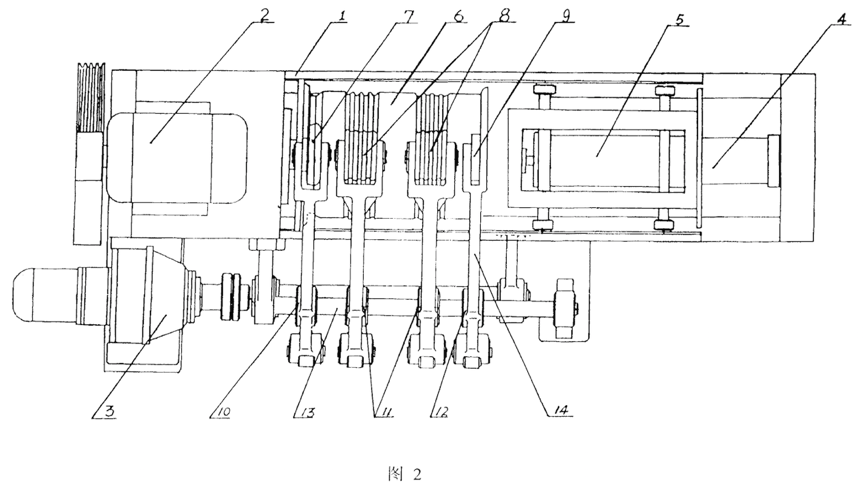
附图3为本发明结构示意图;
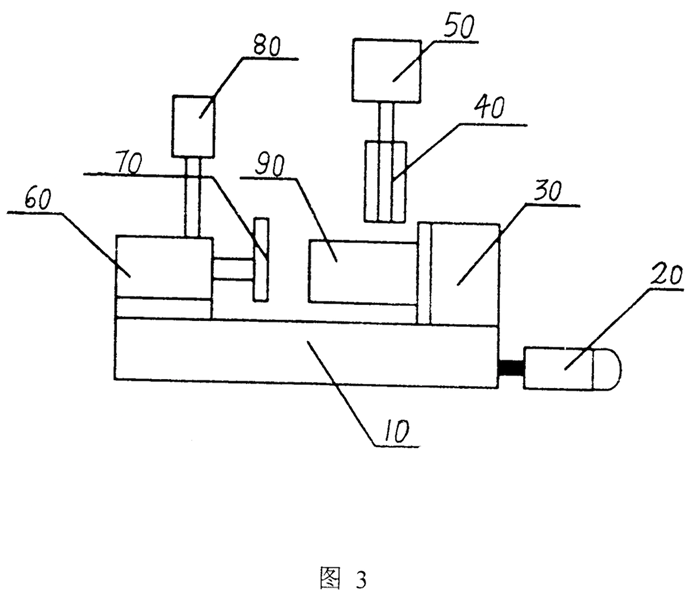
附图4为本发明成型模90剖视示意图。
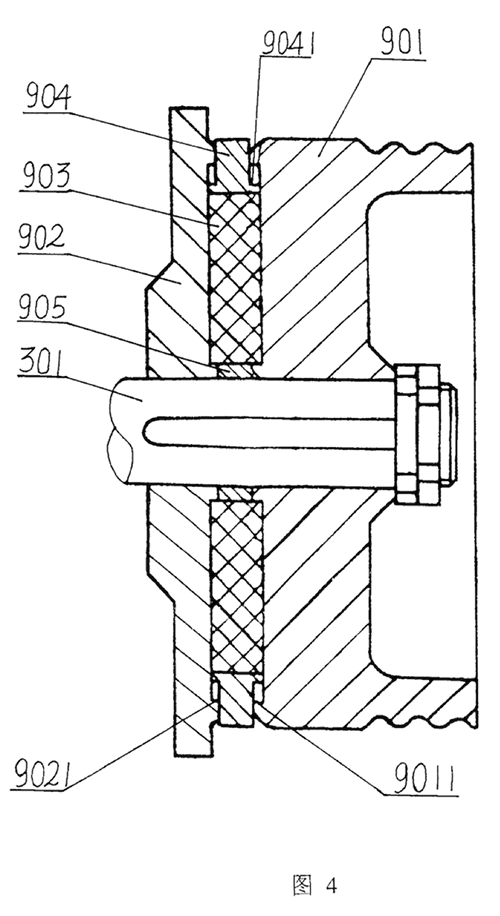
5、具体实施方式:
见附图3、4,本发明包括有机身10、电机20、减速箱30、成型滚轮40、顶紧气缸60、顶紧盘70、成型模90,机身10上连 接电机20、减速箱30、顶紧气缸60;电机20输出轴经减速箱30后连接成型模90,顶紧盘70连接顶紧气缸60;控制成型滚轮40进退的进刀气缸50与成型滚轮40连接;控制缩口机动作的PLC控制部分80亦连接于机身10上;所述的成型模90的滚筋模901、 翻边模902套于减速箱30的输出轴301上,位于滚筋模901、翻边模902间的弹性元件903通过内衬905与输出轴301相套接,并在 弹性元件903外圆上套有缩口模904;滚筋模901、翻边模902与缩口模904相接的一侧各凸伸一环9011、9021,缩口模904的内圆 端亦凸伸有一环9041。
当使用本发明时,先将桶料放于成型滚轮40上,然后由PLC控制部分80控制顶紧气缸60,将顶紧盘70顶紧桶料,电机20启动,通过减速箱30带动成型模90旋转,而成型模90的旋转带动桶料同步旋转;同时,进刀气缸50将成型滚轮40顶进,当进刀到一定的距离后,成型滚轮40的缩口滚部分首先顶住成型滚轮40,继续进刀,通过桶料将缩口模904向内压,弹性元件903被压缩,当缩口模904的外圆与翻边模902或缩口模904的环9011、9021外圆平齐时,缩口到位,且翻边、滚筋亦同步完成;此时,进刀气缸50停止成型滚轮40的进刀,进刀气缸50内的压力控制器达到预定的压力数值,发送一信号到PLC控制部分80,由其控制成型 滚轮40的退刀以及顶紧盘70的后退,取下成型的桶料即可;由于在缩口的过程中,桶料内有随着压力大小而收缩的弹性元件903通 过缩口模904顶住,因而缩口质量好。