冲裁模调试过程中问题分析
文/李少飞
【摘要】阐述了冲裁模调试内容,对调试过程中出现的毛刺、变形、分离不彻底、带料及废料不下滑等问题进行了研究,分析问题产生原因及处理方法。
关键词:冲裁模;调试;毛刺;废料
1 引言
冲裁是利用模具在压力机上使板料分离的一种冲压工艺,包括切断、落料、冲孔、修边、切口等多种工序。一般来说冲裁模主要是指落料模和修边冲孔模,冲裁模结构如图1所示。
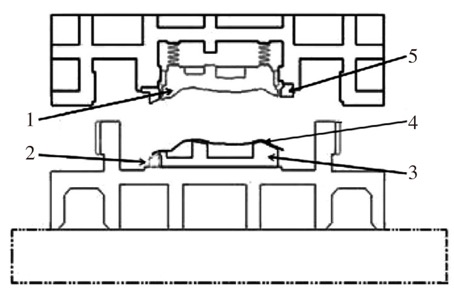
图1 冲裁模结构
1-压料芯;2-废料刀;3-下模;4-制件;5-上模凸模
2 冲裁模调试
2.1 模具调试目的
发现模具设计及制造中存在的问题,以便对设计、加工与装配中的工艺缺陷加以改进和修正,并排除影响生产、安全、质量和操作的各种不利因素,从而制造出合格的制件。
2.2 冲裁模调试技术要求
冲裁模调试技术要求如表1所示。
冲压件的毛刺高度允许值如表2所示。
表1 冲裁模调试技术要求
序号 |
项目 |
技术要求 |
1 |
模具外观 |
冲裁模调试前,应对模具外观质量及空载检验,合格后才能进行试模,其检验方法应按照冲模技术要求进行检验。 |
2 |
试模材料 |
试冲材料必须经过检验,其性能及尺寸需符合技术协议的规定要求,冲裁模允许用材料相近、厚度相同的材料代用。 |
3 |
试冲设备 |
试冲设备必须符合工艺规定,设备精度必须符合要求。 |
4 |
冲压件质量 |
冲压件断面应均匀,不允许有夹层及局部脱落和裂纹现象,冲压件毛刺不得超过规定数值(见表2)。 |
表2 冲压件的毛刺高度允许值(mm)
精度等级/
材料厚度 |
F |
M |
G |
≤0.3 |
≤0.03 |
≤0.05 |
≤0.07 |
>0.3~0.5 |
≤0.04 |
≤0.06 |
≤0.08 |
>0.5~1.0 |
≤0.05 |
≤0.08 |
≤0.12 |
>1.0~1.5 |
≤0.06 |
≤0.12 |
≤0.18 |
>1.5~2.5 |
≤0.08 |
≤0.16 |
≤0.32 |
>2.5~4.0 |
≤0.25 |
≤0.37 |
≤0.50 |
2.3 冲裁模调试要点
冲裁模调试要点如表3所示。
表3 冲裁模调试要点
序号 |
项目 |
调试要点 |
1 |
凹凸模刃口刃入量及间隙调整 |
(1)冲裁模的上、下模要吻合,应保证凸模与凹模刃口相互咬合,刃入量要适中,一般刃入量取2~4mm,以冲裁出合适的零件为准,依靠调节压力机连杆长度来实现。
(2)凸、凹模间隙要均匀,对于有导向的冲裁模,需保证导向件运动顺利而无发涩现象即可保证间隙值;对于无导向冲模,可以用塞尺在压机上调整,直到凸、凹模刃口间隙互相对中且间隙均匀后方可进行试冲。 |
2 |
定位装置调整 |
冲裁模定位件形状,应与前工序形状相吻合。在调整时应充分保证其定位的稳定性,检查定位销、定位块、定位杆定位时是否稳定。 |
3 |
废料滑落调整 |
卸料板形状与冲压件符型,且保证卸料板行程足够;上模顶出销设置在废料区,保证弹力足够大;凹模刃口无倒锥以便于卸件;滑料板角度满足设计要求(一级滑料板≥25°,二级滑料板≥15°);废料滑料顺畅,保证废料一件一滑,冲孔积料不许超过3片。 |
3 冲裁模调试过程中问题分析
冲裁模调试过程中存在的问题类型如表4所示。
表4 冲裁模调试过程中问题分析
序号 |
问题类型 |
产生原因 |
1 |
制件毛刺 |
修边刃口崩刃、修边间隙不合适、工艺排布不合理。 |
2 |
制件变形 |
压料芯压料力不足、压料芯距修边线距离过大、修边间隙不合理。 |
3 |
分离不彻底 |
修边接刀不齐、闭合高度不够、废料刀高度不够、修边间隙不合理。 |
4 |
修边带料 |
压料芯受力不均、压料芯退料力不够、制件变形。 |
5 |
废料不下滑 |
废料刀设计不合理、废料口空间小、滑料板角度小。 |
3.1 制件毛刺
判定标准:
(1)A类缺陷为装配面上的粗毛刺(大于料厚的50%)。
(2)B类缺陷为非装配面上的粗毛刺。
(3)C类缺陷为中等或小毛刺(为冲压件料厚的25%~45%)。
处理方法:
(1)修边刃口崩刃:模具热处理达不到要求及刃口间隙不合适,导致模具刃口寿命降低,出现崩刃、损伤等现象,对崩刃处进行补焊并打磨,上机研配调整间隙并保证刃口垂直度。
(2)修边间隙不合适:凹、凸模刃口间隙(见图2)过大或过小,冲压件断面质量都会变差,理论间隙合理值应为5%~8%的料厚,实际工作中,钳工一般根据经验来判断间隙的大小,修边间隙小的进行打磨,间隙大的进行补焊,然后进行研配,间隙取在凹模上。
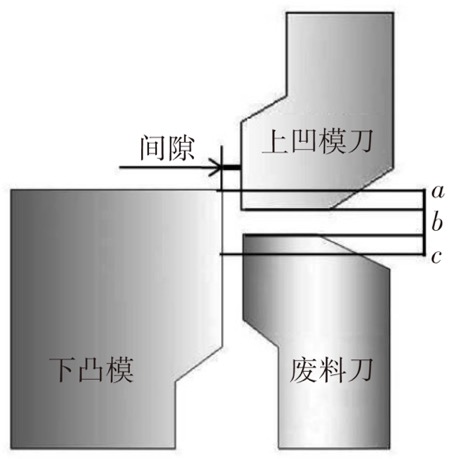
图2 凸、凹模间隙示意图
(3)工艺排布不合理:工艺设计时要尽量避免出现立切修边的结构,如必须使用立切修边,立切角度θ可参照表5所示。
表5 θ角选取
t/mm |
0.6 |
0.7 |
0.8 |
0.9 |
1.0 |
1.2 |
1.4 |
1.6 |
1.8 |
2.0 |
θ°≥ |
5.7 |
8.0 |
9.2 |
10.3 |
11.5 |
13.9 |
16.2 |
18.6 |
21.1 |
23.5 |
如立切角度θ角不满足表5要求,需改造凹模刃口,此外应注意检查压件器行程是否满足最大立切工作行程的要求。
3.2 制件变形
处理方法:
(1)压料芯压料力不足:压料力根据制件料厚、形状不同而变化,一般为冲裁力5%~20%,实际生产中,根据制件料厚及形状复杂程度选取合适的压料力。
(2)压料芯距修边线距离过大:压料芯距修边线距离理论值为0.5mm,直边修边选取0.5~1.0mm,拐角处修边在2mm左右。
(3)修边间隙不合理:合理选取修边间隙。
3.3 分离不彻底
处理方法:
(1)修边接刀不齐:接刀处一般采用圆弧进行过度,因为送料误差很可能由于重切而产生毛刺,工艺缺口处建议用方形,使交接点直角交切,最不易产生毛刺。
(2)闭合高度不够:一般发生在调试阶段,由于模具状态不稳定,需要多次调试确定合适的闭合高度。
(3)废料刀高度不够:废料刀高度过低,导致修边时出现上下刀口接触不良,可补焊废料刀或者增加废料刀的安装座的高度。
(4)修边间隙不合理:合理选取修边间隙。
3.4 修边带料
处理方法:
(1)压料芯受力不均:可能是由于导向不正导致的,可调整导板与导滑面间隙使压料芯受力均匀,保证压料芯与凹模刃口间隙,一般值为0.5mm;同时为保证修边质量,要求修边刃口剪切前先对制件进行预压紧,压料芯预压紧行程≥10mm。
(2)压料芯退料力不够:可更换弹力较大的弹性元件,退料力根据制件板厚、形状的不同而变化,一般为冲裁力的4%~20%,冲裁力与修边长度、料厚和材料剪切强度成正比。
(3)制件变形:由于模具研合不到位导致制件变形,可对模具进行研合,解决制件变形问题,必要时增加弹顶销(在废料区域),将制件顶出压料芯。
3.5 废料不下滑
生产过程中,废料的处理至关重要,直接影响生产效率,也可能因废料无法排出导致模具损坏,存在较高的安全隐患。
处理方法:
(1)废料刀设计不合理:
①废料刀布置优先考虑刃口方向相同,若刃口相对,则刃口角度设计为开口形式并增加强制卸料部件(见图3);
②考虑废料刀布置位置,废料的形状不能为U形(对于特殊形状的制件工艺设计时进行确认),废料对角线长度不大于600mm;
③废料滑道设置方向需与废料滑出方向一致,便于排料顺畅;
④修边废料一件一滑,冲孔积料不许超过3片。
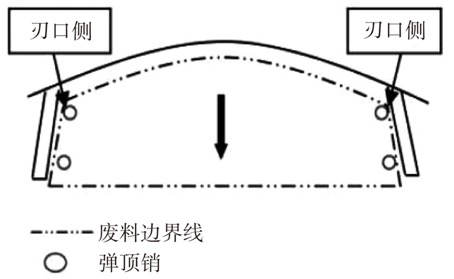
图3 增加强制卸料部件
(2)废料口空间小:废料滑落过程中确保排料顺畅,在不影响模具强度的条件下,尽量增大废料口空间。
(3)滑料板角度小:滑料板角度设置,一级滑料板滑料角度不小于25°,当滑料角度小于20°时,滑料板上增加滤油网板,二级滑料板滑料角度不小于15°。
4 结论
本文分析的问题是冲压制件生产过程中常见的问题,制件毛刺和变形影响制件的品质,制件与废料分离不彻底、修边带料、废料不下滑影响制件的生产效率。通过分析和研究,在设计阶段和调试过程中针对不同的问题制定相应的对策,提高制件的品质和生产效率。
|