基于PLC的开卷校平剪板生产线控制系统设计
文/季本山
摘要:介绍了开卷校平剪切生产线的组成,提出了一种应用PLC、变频器及光电传感器实现开卷机、校平机与横切机之间速度跟随控制的方法,设计了生产线控制系统,PLC与变频器通讯采用LS-BUS协议,板材长度由旋转编码器间接测量。
关键词:PLC;LS-BUS;定长;剪切
1 开卷校平剪板生产线
开卷校平剪板生产线用于将不同规格的冷轧或热轧卷板等卷料,经过开卷、校平、剪切工序后成为所需长度和宽度的平整板材,广泛应用于包装钢桶加工行业。该生产线主要由开卷机、校平机、横剪机组成,如图1所示,按功能分为开卷、校平及剪切3个工序。
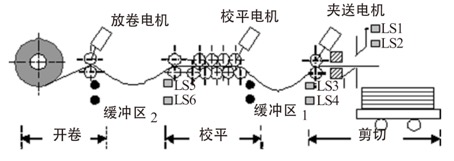
图1 开卷校平剪切生产线示意图
开卷工序将卷绕板材在开卷电机驱动下平铺释放。板材在一对放卷压辊作用下,牵拉卷材绕开卷轴从动旋转,为防止卷材与放卷压辊间的带材松弛下挂,在开卷轴上装有摩擦带,由液压缸拉紧包压在开卷轴上,形成恒定阻力,避免板材挂地划伤表面。开卷后的板材经缓冲区2进入校平工序校平工序将开卷后板料通过辊式校平机上交错排列的辊子,利用多次辅以一定拉伸力的横向交变弯曲而使板料得到校平,可用于各种金属板料的冷态校平,是较为理想的板料和板件校平方式。校平后的板材经缓冲区1 进入剪切工序。
剪切工序将校平后的板料通过测量辊计算出送料长度并按设定长度进行切割,剪切液压缸带动压板和切刀动作完成定尺切断。
由于3道工序组成的生产线较长,为缩短传动链长度,各工序均采用独立电机驱动,为保证生产线协调工作,解决各电机之间的速度控制和板材定尺剪切成为生产线控制系统的关键。
2 开卷、校平、夹送电机的速度控制
开卷、校平、夹送电机均使用由变频器控制的普通三相异步电动机,开卷、校平电机的速度随夹送电机速度而自动调节电动机转速,公式为:
N=60f(1-s)/p (1)
式中:f——频率;s——转差率;p——极对数。
生产线工作时,夹送电机驱动板材按设置的线速度(主速度)做走停运动,其它电机做速度跟随控制,夹送电机驱动板材的线速度V1为:
V1=πD1N1=60πD1f1(1-s)/p (2)
理论上,3道工序若协调有序工作,校平电机和放卷电机驱动板材速度必须与主速度保持一致,据此计算出校平电机和放卷电机的运行频率为:
f2=D1f1/D2 (3)
f2=D1f1/D3 (4)
(2)、(3)、(4)式中,D1、D2、D3为夹送辊、校平输出辊及放卷压辊的直径。
生产过程中,由于加压后辊子存在变形以及各工序阻力不同等原因,按照上述(3)、(4)式频率控制的板材线速度不能与主速度完全保持一致,影响剪切精度,因此,在工序之间,增加了缓冲地坑,安装了4对(LS3、LS4、LS5、LS6)对射式光电传感器,用于检测工序间板材裕量,开机前,保证板材在缓冲区内能挡住LS3、LS5传感器,正常运行时,若板材裕量超过上限,增加缓冲区后道电机的运行频率,若板材裕量超过下限则减小缓冲区后道电机的运行频率,确保板材在两个缓冲区有一定裕量。
3 剪切长度检测
校平后的板材需要按生产工艺要求剪切成长度L的板料,长度选用旋转编码器间接测量,编码器与夹送辊同轴安装,分辨率为2000P/R,夹送辊与板材间做纯滚动运动时,夹送辊旋转一周,板材直线移动距离等于夹送辊周长,编码器每个脉冲对应的板材长度为:
Δs=ΔD1/2000 (5)
剪切长度为L的板材时,编码器产生脉冲数为:
n=L/Δs (6)
通过PLC的高速计数器计量编码器发出的脉冲数,等于n时,停止送料并剪切。
4 控制系统硬件设计
4.1 控制要求
(1)能方便修改工艺参数:包括剪切长度、板材夹送速度及加、减速时间;
(2)上电后自动检测各工作机构的状态,控制生产线各工作机构处于初始位置;
(3)送料:控制系统控制夹送辊作双速运动,待剪板材长度接近剪切尺寸,减速爬行,到达剪切尺寸,送料停止;
(4)压紧和剪切,待剪板料长度达到设定值后,由液压缸带动压料器和剪切刀具,先压紧板料,然后剪断板料;
(5)系统具备手动和自动两种操作模式及必要的保护报警功能。
4.2 控制系统硬件设计
根据开卷校平剪板系统的结构及控制要求,PLC选用LS公司的MASTER K120S系列,人机交互选用eview MT4300C触摸屏,变频器选用LS-IGX系列,控制系统如图2所示。
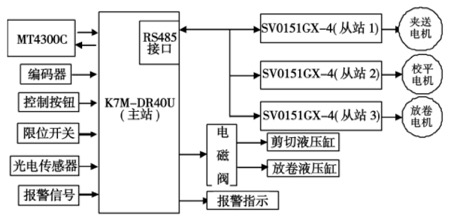
图2 控制系统框图
系统有输入信号20个,输出信号5个,K7M-DR40U有24个输入点和16个输出点,而且自带RS485通讯接口,可用直接与IGX变频器通讯,满足控制要求,PLC 的输入、输出分配如表1所示。
表1 PLC输入、输出分配表
地址 |
输入信号 |
P0 |
旋转编码器A相脉冲 |
P1 |
旋转编码器B相脉冲 |
P2 |
手动/自动选择 |
P3 |
启动 |
P4 |
停止 |
P5 |
夹送正向点动 |
P6 |
夹送反向点动 |
P7 |
校平正向点动 |
P8 |
样平反向点动 |
P9 |
开卷正向点动 |
PA |
开卷反向点动 |
PB |
剪切上限位LS1 |
PC |
剪切下限位LS2 |
PD |
缓冲区1上限位LS3 |
PE |
缓冲区1下限位LS4 |
PF |
缓冲区2上限位LS5 |
P10 |
缓冲区2下限位LS6 |
P11 |
放卷缸限位开关 |
P12 |
变频器报警 |
P13 |
紧急停止 |
P40 |
剪切液压缸伸出 |
P41 |
剪切液压缺缩进 |
P42 |
放卷液压缸伸出 |
P43 |
放卷液压缸缩出 |
P44 |
报警灯 |
生产线上的夹送、校平、放卷电机均由变频器控制,PLC作为主站,变频器为从站,采用RS485接口和LS-BUS专用通信协议实现主、从通信,对变频器进行数字控制,系统具有结构简单、抗干扰能力强、通讯距离远及响应速度快等特点,控制精度达最大频率的0.01%。
5 控制系统软件
控制系统软件包括PLC程序和触摸屏程序。触摸屏程序设计操作画面,完成对PLC控制及参数输入及显示。PLC程序包括初始化、手动、自动、通讯、高速计数及报警程序。
初始化程序完成校平及放卷电机运行频率和剪切长度对应脉冲数计算,各工作机构返回初始状态;手动程序在手动模式下控制各电动机正、反转及液压缸点动工作,便于生产线各机构调整;自动程序完成放卷、校平、夹送及定长剪切的自动循环控制;报警程序检测变频器及生产状态是否正常,异常停车并通过灯光报警;通迅程序确定通信协议,完成PLC主站与变频器从站之间通讯,控制变频器运行方式及运行频率。通信协议是按照一定的数据格式交换数据的一种约定,通信双方均按照这种格式进行发送和接收数据。IGX系列变频器的通信帧格式如表2所示。
表2 帧格式
头码为发送请求‘ENQ’、应答回复‘ACK’及拒绝回复应答‘NAK’:站号是变频器的编号,从01H至20H;特征字符有读取‘R’、写入‘W’、监控请求‘X’和监控作用‘Y’;数据是通讯时读取与写入的数据或者是错误码;求和是把站号、特征字符及数据的内容先转换为十六进制数后再转换为ASCII码相加,取结果的低8位,用以检测通信错误;尾码为帧结束标志。高速计数程序完成编码器脉冲计数,确定板材送料长度。
由于编程软件KGl_WIN中内嵌有通讯及高速计数模块,用户在编程软件中直接填写相关参数即可完成编程,大大减少了软件编写工作量。图3为PLC编程软件中高速计数器0通道参数设置对话框,剪切长度对应的脉冲数存在掉电保持数据寄存器D3500中,板材高速运行时,由于惯性较大,为提高剪切精度,变频器采用两段速度运行方式,在计数当前值D3600大于减速开始值D200时,电机低速运转,当D3600与D3500数值相等时停止送料,开始剪切。
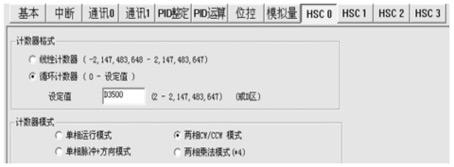
图3 高速计数器参数设置对话框
通迅参数在通讯0或通讯1中设置,首先选择允许通信,然后设置PLC的站号、通信波特率、数据位、校验位及停止位参数,协议与模式选用变频器专用方式,通信通道选用RS485接口,对话框如图4所示。
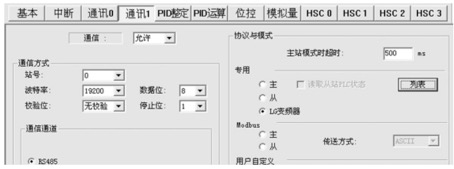
图4 通信方式及协议选择
点击图4右边的‘列表’,出现图5所示的PLC与变频器通讯参数对话框,夹送变频器设为“1”号从站,校直变频器设为“2”号从站,放卷变频器设为“3”号从站,主站数据寄存器D500-D502、D600-D602、D700-D702分别发送到3个变频器从站的H0004-H0006 地址中,地址H0004 中内容为“1”时,允许向变频器中写入数据;地址H0005中为给定变频器的运行频率,单位0.01Hz;H0006的内容为运行指令,写入0000H,变频器停止运行;写入0002H,变频器正向运行;写入0004H,变频器反向运行。
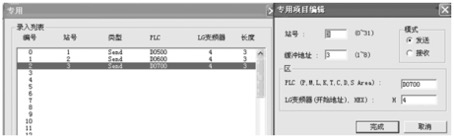
图5 通讯参数对话框
6 结论
以可编程控制器、变频器为核心的放卷、校平及剪切控制系统工作稳定可靠,控制系统成本低,多道工序之间速度跟随控制效果较好,变频器采用多段速度控制能提高剪切精度,板材剪切≤0.1%,操作简单,工艺参数调整方便。
|