直压式钢桶密封性能自动化检测装置的设计
文/唐瑞
摘要:为了实现钢桶密封性能的安全检测,设计了一款基于直压法原理的自动化钢桶密封性能检测装置。该装置主要由气路系统、机械辅助装置及控制交互系统组成,通过实时对比密封钢桶内压力变化值,完成承压能力较小的密封钢桶自动化检测。同时,基于方便、快捷的设计理念,该装置采用一键式检测思想进行设计,通过机械辅助装置实现待检测钢桶的自动化装夹与密封准备,并利用电气比例阀与气体流量控制器的自动控制功能控制充气压力与充气速度,实现充放气过程稳定可控。
关键词:钢桶;安全检测;密封性能;直压法
密封性能检测作为密封容器性能检测的重要环节,在保障产品质量方面有着极其重要的作用。对于有密封性能要求的工业产品,如果在实际使用过程中产品的密封性能没有达到设计要求,将直接影响产品的可靠性与安全性。
直压法检测简便易行且经济性较好,已经广泛应用于容器密封性能检测装置中,但目前采用的直压法检测装置往往采用单一的截止阀或电气比例阀来控制充放气过程,对于有较高充气压力要求的低耐压产品,其最终的充气压力难以保证、充气安全性较差。
为此,本文提出了一种采用电气比例阀与气体流量控制器串联的气路控制结构,并设计 了一套自动化密封性能检测装置,实现了低耐压钢桶密封性能的一键式检测,有效地提高了其检测效率与安全性。
1 钢桶密封性能自动化检测装置
钢桶密封性能自动化检测装置主要由气路系统、机械辅助装置及控制交互系统组成,如图1所示,可实现钢桶密封性能的一键式检测。同时从实用性、美观性的角度出发,将整个测试装置集成在小车式测试平台上,操作面板只设置启动按钮与急停按钮,通过预设程序实现钢桶密封性能自动化检测,最后将测试数据进行存储,并通过指示灯显示检测结果,对操作人员的操作能力要求较低,有效减小了由于操作人员不同导致的测试结果差异。该装置主要用于承压能力较小的密封钢桶检测,因此测试气压与充气流量需严格控制,防止因压力与流量过大导致密封钢桶发生不可逆转的损坏。同时,为减少检测过程的准备时间,装置采用自动化装夹机构,通过钢桶自动化夹紧、移动以及密封动作实现钢桶的检测前准备,缩短待检测钢桶检测准备时间。
2 钢桶密封性能检测原理
直压法测量泄漏量是通过将气体净化、调压以后直接充入被测容器中,当容器内压力达到设定压力时断开压力源,保压后待容器内部压力稳定,开始检测被测容器内部压力随时间的变化量,然后根据压力值与泄漏量函数关系计算出单位时间的气体泄漏量,通过与产品工艺要求的允许值比对,从而判定待检测容器的密封性能。
根据理想气体状态方程可知:
PV=nRT(1)
式中:P为理想气体的压强;V为理想气体的体积;n为气体物质的量;R为理想气体常数;T为理想气体的热力学温度。
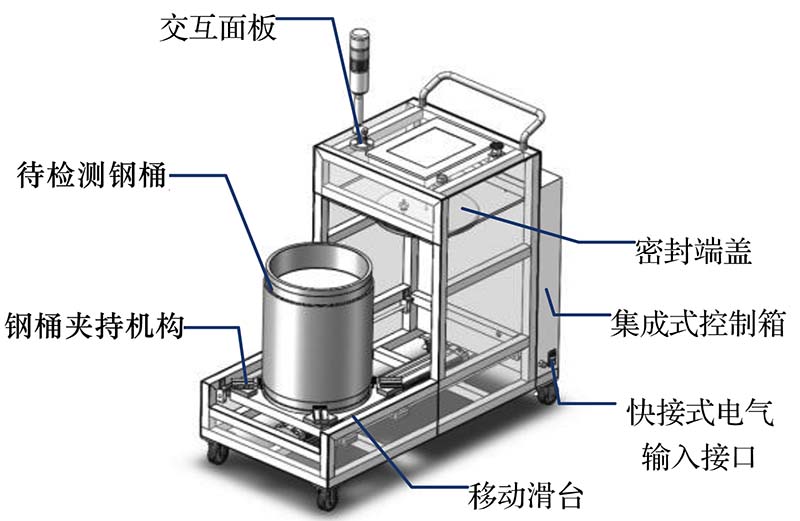
图1 钢桶密封性能自动化检测装置三维示意图
同时,根据玻义耳定律,当n、T一定时V、P成反比。假设气体热力学温度恒定,建立压力值与泄露量的函数关系式为:
P1·V=P2·V+P0·V泄漏 (2)
m=V泄漏/T (3)
式中:P1为被测钢桶的初始压力,MPa;P2为被测钢桶测试时刻的压力,MPa;P0为环境气压,MPa;V泄露为泄露到环境中的气体体积,L;V为被测钢桶内部当量容积,L;m为单位时间气体泄露量,L/s;T为检测间隔时间,s。
本文根据直压法测量原理与自动化控制需求,建立如图2所示的检测装置气动原理图。
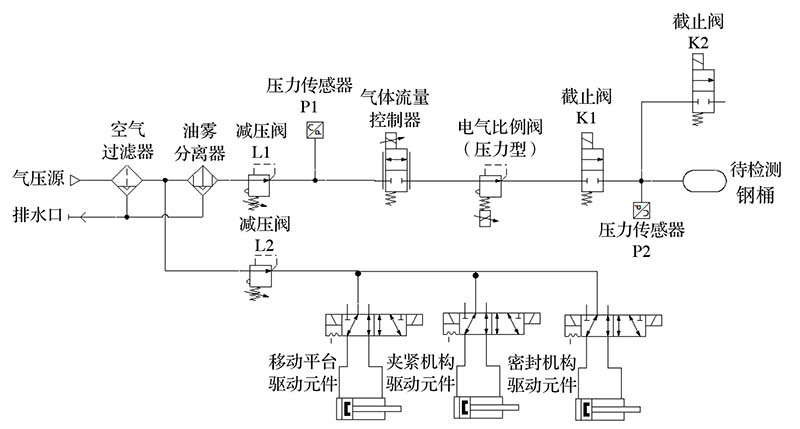
图2 系统气路图
可以看出,本装置气路主要由快插接头(与工房气源进行连接)、空气过滤器、减压阀、电气比例阀、气体流量控制器、电磁控制阀、执行气缸以及气体压力传感器等组成。
整个系统气路主要分为两部分:检测气路与执行气路。为保证检测时充入待检测筒体的气体的纯净度,检测气路增加了气体油雾分离器,实现输入气体的再净化。
该系统的测试周期分为恒流量匀速充气期、恒压充气期、保压测试期以及排气期,测试流程如图3所示。
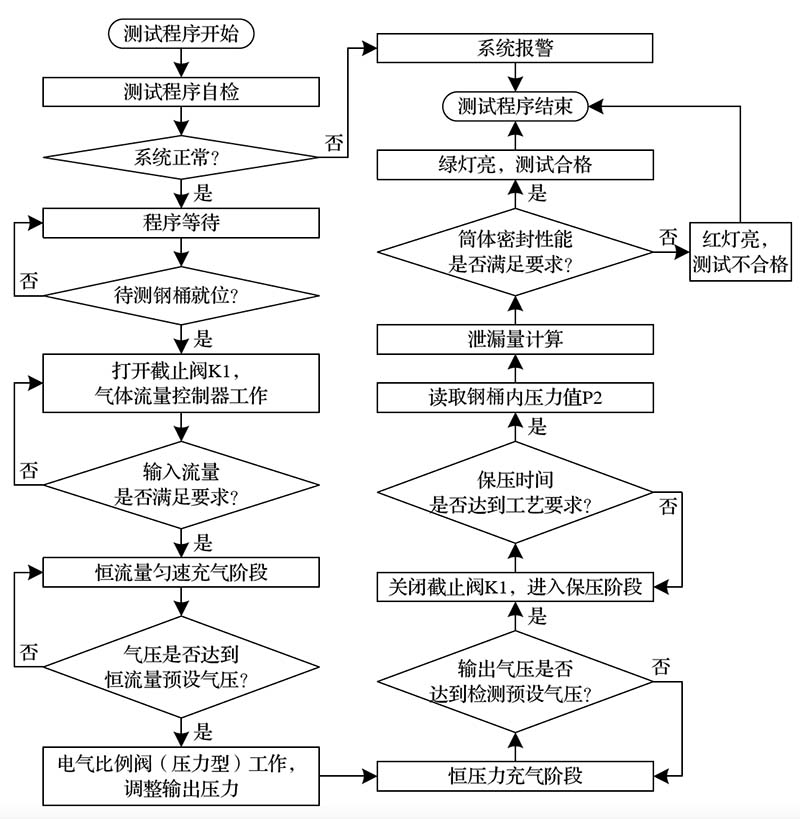
图3 钢桶密封性能自动化检测装置测试流程图
恒流量匀速充气期:电气比例阀(压力)保持最大开度,气体流量控制器实时控制充气流量,以均匀充气流量完成恒流量匀速充气期。
恒压充气期:当钢桶内压力接近测试初始压力后,电气比例阀(压力)根据压力反馈将出口压力调整至工艺要求的钢桶检测初始压力,气体流量控制器保持最大开度,从而保证钢桶内最终的充气压力安全到达工艺要求的检测初始压力。
保压测试期:恒压充气期结束以后,关闭截止阀K1,开始计量读取钢桶内气压随时间的变化值。如果产品存在泄露点则钢桶内气压将会不断减小,到达判定时间以后,通过泄漏量计算公式计算气体泄露量?与设计指标进行比对,最终对其合格性进行判定。
排气期:当测试完成以后,通过打开截止阀K2,将钢桶内的气体排出,然后由执行机构将钢桶送出,完成检测过程。
通过上述气路系统设计,该装置不仅能够实现密封腔体的充气、保压以及排气过程可控,同时能够实现钢桶密封性能检测过程的自动化装夹,减少工装准备时间,大幅度提升钢桶密封性能检测效率。
3 O型密封圈静力学仿真分析
为了实现密封性能检测过程中待检钢桶端面的有效密封,本文基于ANSYS Workbench软件对端面O型密封圈受力情况进行静力学仿真分析,从而选取合适的密封机构执行气缸。
本文选用的O型密封圈内径300mm、线径5.3mm,材料为氯丁橡胶。由于橡胶材料具有超弹性能,属非线性材料,本文选用Mooney-Rivlin 超弹本构模型,橡胶材料的不可压缩参数为1.212×10-9Pa-1。由于O型密封圈具有圆周对称性,为减小计算量,提升计算精度,在实际分析中采用二维轴对称模型,图4为O型密封圈等效应力图。
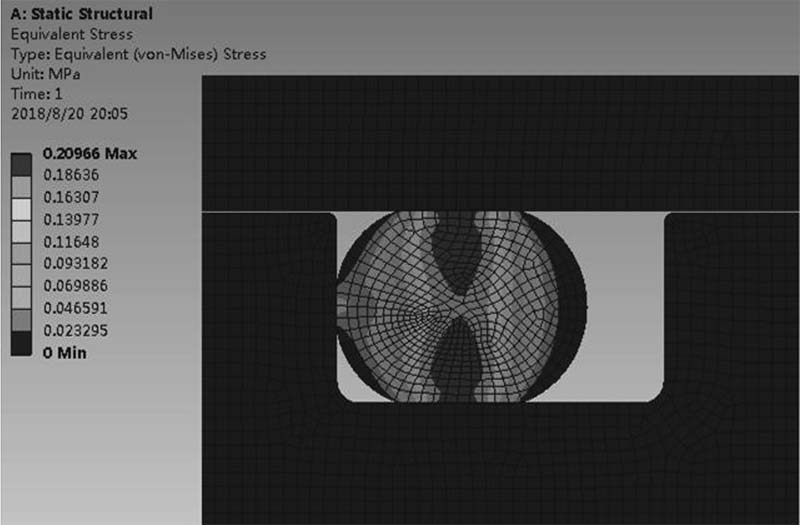
图4 O型密封圈等效应力图
由于密封性能检测过程中,钢桶内部最大压强为50kPa,端盖受压面积为70685.83mm2,故钢桶内部受力为3534.29N。根据ANSYS Workbench反力求解,当O型密封圈压缩1mm时需要472.82N的压缩力。因此,为保证待检钢桶端面的有效密封,密封端盖的推力至少需要4007.1N,当安全因数取1.5时气缸推力需不小于6010.67N。考虑工房内最小供气气压为0.5MPa,同时根据气缸输出推力计算,应选取缸径为125mm的气缸作为密封机构执行气缸。
4 系统硬件及软件设计
密封性能检测设备作为测试仪器,尽管其操作简单,但是如果出现误操作,则很容易使测试结果受到影响,甚至直接损坏设备。另外,对于批量化的检测工作,检测参数往往是固化的,而过多的操作功能与按键反而降低了设备的使用性能。因此,本装置采用一键式的设计思想,对装置的硬件系统进行设计,不仅能从根源上杜绝误操作,而且也大大降低了装置的使用门槛。
该系统框图如图5所示,主要由嵌入式触摸控制屏(TPC1162Hi)、PLC可编程逻辑控制器(CP1E-N40DR-D)、传感器、电磁阀、气体流量控制器、电气比例阀(压力)以及输入输出设备组成。其中,嵌入式触摸控制屏作为上位机实现人机交互设备与主控制设备,通过RS232/RS485分别连接气体流量控制器、压力型电气比例阀和PLC可编程控制器,PLC可编程逻辑控制器实现对于传感器、按钮、指示灯和电磁阀的信号采集与控制,实现钢桶的装夹、传送、密封及密封性能检测操作。
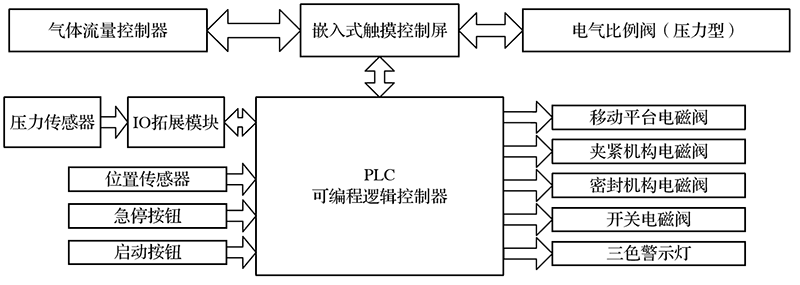
图5 硬件系统框图
5 结论
钢桶密封性能检测工序主要分为待检部件准备阶段、充气阶段、保压阶段、结果判读与数据记录阶段以及仪器恢复阶段。传统的检测方式采用手动密封,极大地限制了生产效率的提升。通过实验验证,采用该自动化检测侧装置后大幅度减少了钢桶密封性能检测的准备与恢复时间,钢桶密封性能检测效率提升62.5%,同时充放气过程更加稳定,检测初始气压误差小于0.5%,保证了该钢桶密封性能检测过程的安全可靠。
|