废旧钢桶翻新自动化生产线系统设计(1)-绪论
文/解俊强
【摘要】
本文研究的油桶为200L钢制油桶,常作为储存化工原料的运输容器。这类废旧油桶属于危险废弃物,常用的处理方式是翻新后进行二次利用。这样的处理方式符合低碳经济节能减排的目标,有利于经济发展过程中的环境保护,提高生态资源利用率。本文设计开发了一条废旧油桶翻新生产线,以提高油桶翻新效率和资源利用率,减轻油桶翻新过程中产生的污染为目标,实现生产线的自动化控制。论文主要研究工作如下:
1、阐述本文的研究目的和意义。详细阐述了油桶行业背景需求和目前油桶翻新方法,并深入分析了油桶翻新生产线的功能要求和工艺流程,针对油桶翻新存在的设备功能单一、生产效率低等问题提出了模块化解决方案,包括系统框架组成、系统设计及实现等。
2、设计了废旧油桶翻新生产线控制系统总体方案。基于DCS系统“集中管理,分散控制”思想进行油桶翻新生产线控制系统层级搭建;利用MPIPROFIBUS-DP、PROFINET等通信技术实现系统层级之间的信息交互,提高系统通信效率;采用上位机+PLC为控制模型,实现控制系统可视化操作。
3、设计了该自动化生产线的控制系统。以模块为单元对工艺流程进行深入研究,根据控制流程分配了系统的I/O点,设计了控制柜的整体结构,完成控制柜硬件设计;开发了基于PLC的控制系统和监控系统:利用STEP7设计PLC梯形图程序,二次开发WinCC组态软件设计了该生产线的人机交互界面。
4、系统调试与试验测试研究。基于PLCSIM仿真软件对该生产线进行了仿真分析,对生产线设备进行了现场调试,通过对生产线油桶翻新测试试验的设计与研究,试验结果表明该生产线的工作效率可以达到每支桶1.5min,相比于人工每支桶15min,可以提高10倍的生产效率,而且提高了油桶的翻新质量。
关键词:油桶翻新,控制系统,可视化,模块化,PLC
第1章 绪论
1.1 课题来源
随着科学技术的迅速发展和生产力水平的不断提高,各行业手工作业的弊端越来越明显,人们越来越重视如何降低劳动强度、提高设备自动化程度。废旧油桶翻新生产线可以提高油桶翻新生产效率,有利于提高资源利用率。本文来源于天津瑞驰船舶机械有限公司委托天津职业技术师范大学共同研发的废旧油桶翻新生产线项目。
1.2 研究背景及意义
中国已经成为世界上原材料生产品种最多、规模最大的原材料工业制造大国,面临的主要问题是能耗高、资源消耗大、高附加值产品少、环境污染大。因此,工业生产必须实现高效化与绿色化,向低碳经济模式转型。低碳经济模式提倡的是一种人与自然和谐相处的智慧经济模式,需要我们建立低碳思维;引进先进的低碳技术;重视低碳经济的转型发展。在工业包装行业,我国每年都会有大量的废旧油桶需要进行回收、翻新、再利用。废旧油桶翻新生产线目的是实现油桶翻新自动化生产,具有以下两方面优势:一方面符合社会发展要求,必须坚持绿色、可持续发展的原则;另一方面符合工业生产面向工业自动化控制的发展趋势。工业上实现自动化主要技术有PLC(Programmable Logic Controller)控制系统、DCS(Distributed Control System)控制系统、FCS(Fieldbus Control System)控制系统、工业PC控制系统等,而伴随着计算机和网络技术的发展,系统变得更具开放 性,系统之间可以通过融合实现信息技术与控制技术的无缝连接,向测、控、管一体化方向发展。实现生产线自动化控制的本质是实现生产线机电一体化,通过开发相关软件使机械与电气相结合,构成一个控制系统。本文设计的废旧油桶翻新生产线控制系统以DCS系统思想搭建控制系统的层级架构,以PLC技术作为该系统控制核心,通过应用现场总线技术和工控机实现系统通信和可视化控制管理。因此,本文的总体研究内容为控制系统设计,控制对象为废旧油桶翻新生产线,生产线加工对象为200L全开口钢桶,如图1-1所示,钢桶规格型号详见 GB/T 325.3-2010《包装容器:钢桶》。
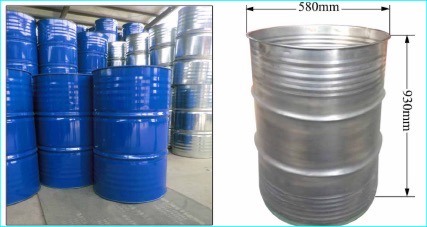
图1-1 200L全开口钢桶
1.2.1 控制系统的发展现状
随着计算机技术特别是微型计算机和网络技术的飞速发展,现代工业的自动化水平得到了极大提高。工业生产中常用的控制系统有DCS系统、PLC系统和 FCS系统,三者有各自的优势和不足,但随着系统更具开放性,可以通过开发软件及通信技术予以弥补。
DCS控制系统集4C技术(Communication,Computer,Control,CRT)于一体,架构包括现场层、监控层、管理层三层结构,应用于现场、工作站、设施与服务器,具有组态方便、分级管理、集中操作、分散控制等特点。DCS在复杂的过程控制中占有很大的优势,例如中小规模控制系统可采用双冗余,即主控制器冗余+通信网络冗余,提高系统可靠性,在制糖生产线等大规模的化工生产中,以DCS控制系统作为制糖生产线的中控系统,可实现对各生产环节进行集中管理以及分布式冗余控制。但是传统的DCS其系统连线复杂、可靠性降低、维护量大、通信速率慢等弊端,而且成本高,各公司产品不能互换,不能互操作;PLC是一种自动控制装置,它的控制方式主要是开关量的逻辑控制、模拟量控制、运动控制、过程控制等四种控制方式,其特点是抗干扰能力强,系统灵活性,通用性强,软件功能强,使用维护方便且成本经济。因此,PLC在国内外应用广泛,不仅常用于在化工、电网、水利等控制系统,在农业、养殖业等行业也常用于控制分拣、包装等。PLC可以作为DCS体系的现场层控制装置,PLC相对于DCS有更好的顺序连锁功能和更开的逻辑执行速度,而且PLC基于现场总线的远程分布式I/ O,体积小 更灵活易用,能有效地节省接线成本。通过系统集成将PLC与DCS有点集于一体,即可以实现更好的逻辑及顺序控制,又能兼具管理功能、体积小、成本低等优点;FCS是在DCS/PLC基础上发展起来的新技术,是3C技术(Communication,Computer,Control)的融合,它最深刻的改变是现场设备的数字化、智能化和网络化,FCS系统比DCS系统更好地体现了“信息集中,控制分散”的思想,而且FCS相对于DCS组态简单,由于结构、性能标准化,更加便于安装、运行、维护。
进入二十一世纪以来,可编程序控制器己成为工业自动化领域中主导控制装置,已跃居工业生产自动化四大支柱(可编程序控制器、机器人、数控机床、计算机辅助设计与制造)的首位。本文总体方案以DCS控制理念搭建生产线控制系统基本架构,即搭建现场层、监控层和管理层的总体结构,采用上位机+PLC 控制模型,并融合FCS总线技术,实现生产线的可视化监控与管理,具体系统设计实现是把PLC、WinCC和PROFIBUS三者结合在一起,实现控制系统三层结构之间的通讯和监控。选用PLC为控制核心因为PLC有很好的应用前景:
1)人机界面更加友好。目前,广泛被应用的是PLC+IPC(Industrial Process Control)+网络的模式。
2)开放性和操作性的发展。系统构成灵活、扩展容易。以开关量控制为核心,能与上位机构成复杂控制系统,也能进行连续过程的 PID 回路控制,实现生产过程的综合自动化。
3)使用方便、编程简单,采用简明的梯形图、逻辑图或语句表等编程语言,而无需专业计算机知识,具备系统开发周期短、现场调试容易的优点,另外可在线修改程序,改变控制方案而无需更新硬件。
4)能适应各种恶劣的工作环境,抗干扰能力强,可靠性高。PLC一般应用于工业环境,工业环境具有电磁环境复杂,许多工作环境具有高温、高湿、振动冲击、电磁干扰、电源电压不稳定、低大气压等极限环境下,PLC必须在各种极限的环境下稳定工作。
1.2.2 油桶翻新行业国内外现状
200L钢桶常用于化工产品包装,本文是以用于石油、化工类包装的钢桶为翻新研究对象,整理的有关油桶行业的国内外现状如下:
1)油桶翻新行业国外现状
如图1-1为2007年统计的国外钢桶的平均每年产量。美国的新钢桶生产量始终保持对稳定,从1985年开始,200L钢桶的平均年产量为2740万只,旧桶翻新量,从1985年的3810万只下降到2003年的3070万只;欧洲,200L钢桶平均每年的生产量为3700万只;在印度,钢桶生产量以每年7%的速度增长,而旧桶翻新工业有小规模的生产经营者,每年的翻新量大部分只有30000只左右;在南美,阿根廷、巴西、智利和哥伦比亚等几个国家是工业包装容器和回收翻新工业包装容器的主要生产国;在亚洲,日本200L钢桶旧桶翻新业正以每年6%的速度在递增。从图1-1中可以看出工业越发达地区油桶的生产和使用量越大。
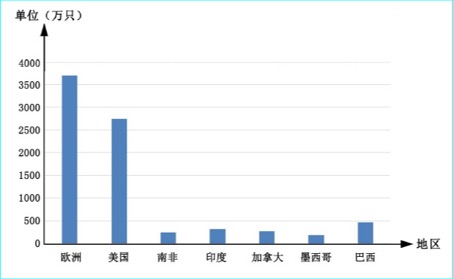
图1-1 国外钢制油桶平均每年产量
在欧洲,布莱格登包装公司是欧洲第二大钢桶制造商,在钢桶及 IBC 容器翻新业务方面位居第一,已经把钢桶制造业与旧桶翻新业联合。把布莱格登建成了一个服务型的公司,为客户提供解决方案,通过“闭路循环法”把工业废桶加工成可再利用的产品或者用于回收再利用的铁屑。
在美国,200L的钢桶一直是化学工业包装的主力,在许多类型的危险品和非危险品的运输包装中,应用最为广泛的工业包装是钢桶。图1-2为2010-2016年美国国内工业生产总值与工业产品和钢桶产量的变化曲线,显示了在美国工业产品对钢桶产量的影响。
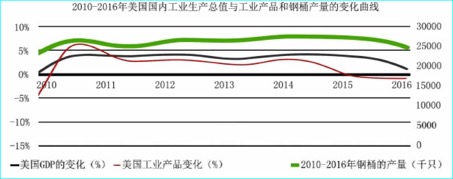
图 1-2 年美国国内工业生产总值与工业产品和钢桶产量的变化曲线(2010-2016 年)
日本将钢桶作为回收再利用的最佳资源。使用过的钢桶,一部分被旧桶回收商修复再利用,而其他部分则直接从消费者手中回收并运送到废品处理站,该方法广泛用于钢桶的回收利用,被称为是循环再造的典范。把直接回收到废品处理站的桶排除在外,钢桶的回收利用率为59.6%。实质上资源回收率是100%。表1-1为日本2011-2016年油桶的生产和回收利用率等数据。
表 1-1 日本 200L 油桶行业情况(2011-2016 年)
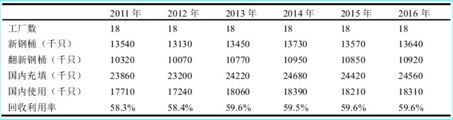
从自然资源的环境保护方面来看,日本的再生桶行业是受到欢迎的。通过日本钢桶协会国际标准化的调查报告,钢桶壁厚是影响钢桶可再生次数的主要原因,1.0mm壁厚的钢桶可再生约1次,1.2mm壁厚的钢桶平均可再生约3.45次,1.6mm 壁厚的钢桶平均可再生约5.2 次。如图1-3为油桶厚度与翻新次数关系。需要注意的是影响油桶的回收翻新次数另外一个关键因素是翻新设备。
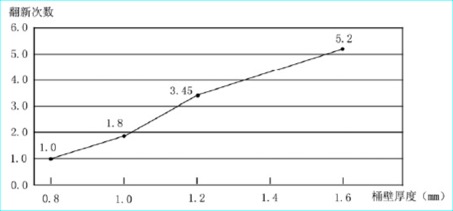
图 1-3 油桶壁厚与翻新次数关系
图1-4是日本2016年4月到2017年3月钢桶回收利用流程图。
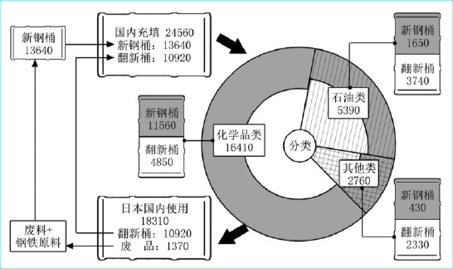
图1-4 日本2016年4月到2017年3月钢桶回收利用流程图(单位:千只)
综上所述,可以看出油桶的产量与化工行业的产值有着密切关联,在国外钢制油桶行业越来越重视废旧油桶资源的回收利用,日本对油桶的回收利用流程方式可以实现100%的回收利用,反映出油桶翻新研究的对油桶资源回收再利用重要性。
2)油桶翻新行业国内现状
根据中国包装联合会的指示和国家统计局(2015)46号文件精神,2015年全国钢桶产量统计情况如下:
调查中共统计了145家钢桶包装企业,从统计的情况看,包装企业之间的相互渗透越来越多,钢桶企业中生产200L、100L及中小型和大型(IBC)吨箱的企业越来越多。均采用多品种,多渠道的经营模式,虽然统计的145家企业占全国钢桶企业总数的20%,但他们生产钢桶的数量占全国钢桶市场总量的70-80%。145家钢桶企业共生产200L钢桶8168.32万只;中小钢桶1185万只;200L塑料桶2416万只;40-100L塑料桶500万只;16-20L的塑料桶450万只;0.1-20L的塑料桶罐1176万只;IBC塑料吨箱200万只。根据行业专家分析,2016年全国200L钢桶的总产量已经达到1.3亿只。与2015年统计产量相比,200L钢桶全国总产量均长了约 1000万只。200L钢桶的产量分布情况如表1-2 所示。
表1-2 200L钢桶的产量分布情况
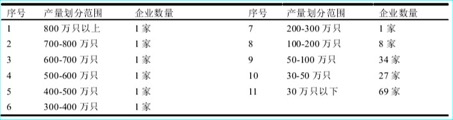
国内油桶行业在回收处理方面还存在以下几个问题:
a)缺少可靠的旧桶来源。国内的回收业发展极不平衡,至今没有统一的钢桶回收管理系统,没有专门从事这项工作的管理机构,所以旧桶翻新业由于没有稳定的旧桶来源而难以发展。
b)资源消耗量大。钢桶包装所使用的资源以钢铁为主。在产品的成本中,钢铁材料所占的比例达到70%-80%。所以说,钢桶包装业是资源消耗的大户;钢桶包装业在生产中对能源的需求量也很大,比如在钢桶的涂装生产中,因为需要进行烘干,所以需要消耗大量的电能、天然气、煤或油等。
c)缺少先进的旧桶翻新技术和设备。近年来新钢桶生产设备技术发展很快,但少有人涉足旧桶翻新设备的开发和制造,不少有条件进行大规模旧桶翻新业务的企业,由于找不到先进的旧桶翻新设备而放弃回收。目前从事旧桶翻新设备生产的少数企业,由于设备技术落后,生产率低,难以满足现代化生产的需要。没有高效率的设备,旧桶翻新工作就难以产生效益。
d)环境污染比较大。在钢桶包装的生产过程中,还存在严重的环境污染问题,在钢桶生产中,由于清洗磷化产生废水而造成水的污染;在钢桶涂装和烘干中产生大量废气造成的污染等。
e)回收利用问题很多。薄型钢桶包装产品多为一次性使用,再利用率比较低;厚型钢桶一般可多次使用,但在回收利用时都要进行再次的清洗和翻新,同样要消耗大量的能源和造成污染。废旧钢桶包装物回收后多数都是回炉重炼,这不符合节省资源和能源的原则。
1.2.3 油桶翻新设备研究现状
关于油桶翻新生产线的研究现状,经查阅相关文献,1991年发表的一篇研究成果是为改变200L废旧油桶的人工修复和涂覆作业方式,设计了油桶表面自动除锈喷漆生产线,研究成果主要包括桶壁的除锈和喷漆加工工艺分析和CCS实现的生产线自动控制;以及2004年的一篇研究成果,它简要阐述了油桶翻新的主要工艺流程:油桶整形、桶内清洗、桶外清洗、表面烘干和表面喷漆;从2004年到现在,存在一些关于油桶清洗、油桶整形等方面的进一步研究成果,最新研究成果是 2012年的关于油桶清洗的研究,对本文的研究都有很重要的参考价值。
经过对以前的油桶翻新相关研究成果的整理发现,相关文献资料有以下两大特点:一是文献多数过于陈旧;二是研究缺乏系统性。这导致关于油桶翻新生产线的研究不够深入也是市场上的油桶翻新设备不够成熟规范的重要因素。因而现在存在的翻新设备往往都是以单一功能的加工设备被设计出来使用的,如油桶传送线、抛光机,整形机,卷边机等,如图1-3所示:a为一种油桶传送线,b为一种抛光机,c和 d为两种不同形式的整形机。这些设备也都受相关研究的匮乏的影响,虽然能满足油桶翻新加工的功能需求,但是设备设计以及加工产品不规范,生产效率低,浪费生产资源而且对环境产生严重的二次污染。
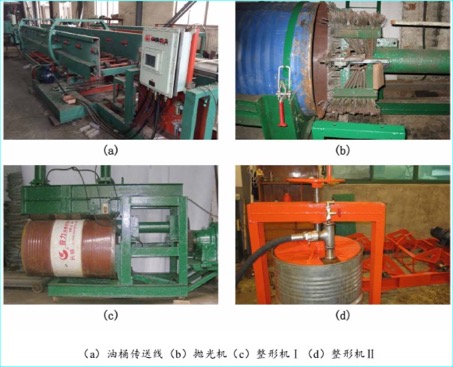
图 1-3 现有翻新设备
经过对相关资料调研,确定了油桶翻新生产线设计的必要性与可行性。本文研究的是废旧油桶翻新生产线的控制系统设计:油桶翻新生产线作为一种现代工业设备产品,以绿色可持续设计原则,以节约资源、提高资源的利用率为研究目标,以实现自动化控制、降低成本提高效率,促进油桶翻新生产线规范化、标准化为研究方向,对整个生产线进行模块划分,将生产线系统设计标准化,保证生产线功能实现的同时利于生产线后期的优化升级。综上所述,本文的研究意义有以下几点:
1)油桶翻新行业翻新油桶需求量大,但自动化加工水平低,有必要进行自动化系统生产线设计。
2)PLC技术作为工业控制系统组成功能强大,集成度较高,技术成熟,控制系统稳定,而且相对其他控制技术成本更低。
3)符合社会发展要求,即建设资源节约型社会,因为油桶翻新利用的方法在一定程度上有利于提高资源利用率。
1.3 主要研究内容及关键问题
研究内容主要包括以下几个方面:生产线工艺流程分析,PLC 系统总体方案设计,系统硬件设计,系统软件设计以及系统调试与试验。
1)生产线工艺流程分析
经过对油桶翻新生产线分析,这条生产线设计包括四个关键的加工工艺:加温工艺、除锈工艺、整形工艺和抛光清洗工艺。加温目的是使油桶桶壁附着物碳化,提高喷砂质量和喷砂效果;除锈工艺采用的的是喷砂除锈,是通将磨料( 喷丸玻璃珠、钢砂、石英砂、金刚砂、铁砂、海砂等) 高速喷射到待处理的桶壁表面,利用磨料本身的硬度、冲击韧性和棱角,将桶壁表面的各种锈迹祛除,除锈等级可控制在Sa2.5到 Sa3之间;整形工艺是利用液压系统让压辊对桶壁进行挤压实现整形的目的;抛光清洗工艺是用电机带动钢刷对桶壁抛光,抛光之后的油桶还需要对油桶进行自动清洗和擦干。这四个工艺形成一个完整的油桶翻新工艺流程。
2)PLC系统总体方案设计
本文的废旧油桶翻新生产线控制系统设计目的是实现生产线的机电一体化,实质是将机械技术与电子技术相结合,其结构组成要素包括生产线本体、计算机、传感器、执行器和系统动力。系统总体设计之前要对整个方案的可行性进行论证,系统的设计首先要满足用户的基本要求,其次加强系统的可靠性,在此基础上优化设计降低设计成本。因此,废旧油桶翻新生产线的控制系统总体方案设计包括三个主要方面内容:控制系统总体架构、系统硬件设计、系统软件设计。
3)系统硬件设计
系统硬件构成以DCS控制系统为架构搭建系统的现场层、监控层和管理层,以PLC为控制装置搭建现场层级的PLC主控制系统,通过MPI、PROFIBUS以及工业以太网等通信技术实现三个层级的信息交互,在监控层开发WinCC组态软件,实现生产线在线实时监控、分析和诊断线路故障。系统硬件设计主要包括四个方面内容:传感器和执行器选型、PLC控制系统模块选择、控制柜的设计等。
4)系统软件设计
系统软件设计包括两个主要方面:控制软件和监控软件。控制软件是利用 STEP7软件设计PLC的程序梯形图,采用模块化设计方法,根据生产线的功能模块编写模块程序,通过主程序调用子程序方式简化生产线逻辑;监控软件是对WinCC组态软件进行二次开发,搭建生产线组态,以PROFIBUS建立PLC与上位机之间的通信连接,达到废旧油桶翻新生产线的可视化监控目的。
5)系统调试与试验
对系统的I/O点调试,排除硬件上的故障,用PLCSIM软件对PLC控制程序进行仿真调试排除软件上的故障,通过现场调试测试控制系统,完成测试试验。
综合以上内容,本文基于PLC的废旧油桶翻新生产线的控制系统设计需要完成以下工作内容:
1)分析生产线的工艺流程与控制要求;
2)完成控制系统总体设计,包括:控制系统结构组成分析与设计;软、硬件系统主要配置组成;给出系统评价方法;
3)完成系统硬件与软件的设计,包括:硬件设计,包括工艺流程分析、硬件配置选型、编制I/O分配表及端子图、卡件接线;软件设计,包括编写PLC梯形图、操作站人机界面的设计等;
4)设计试验,完成控制系统的调试。
1.4 本章小结
阐述了本文的研究背景及目的意义,概括了控制系统的发展、油桶翻新行业国内外现状以及油桶翻新设备的研究现状,总结了本文的研究内容。
|