废旧钢桶翻新自动化生产线系统设计(5)-系统调试与试验
文/解俊强
第5章 系统调试与试验
系统的调试方案主要分为三个部分:实验室模拟调试、控制柜调试和现场调试。系统调试的整体构成如图5-1所示。三个部分调试的工作内容和目的不同,模拟调试是验证控系统的软件系统部分可行性;控制柜调试是测试系统组成部分是否能正常工作,比如传感器能否正常工作等问题,排除掉坏通道等故障,保证软件系统的正常运行;完成以上两个调试部分已基本排除系统的硬件和软件两方面的逻辑以及故障等问题,下一步进行系统的现场调试,现场调试要完成五项调试工作:PLC硬件调试、控制柜现场调试、上位机监控软件调试、控制系统联合调试和控制柜、电气柜的联合调试以及整体和现场的最终调试。 系统实验是在调试工作完成的基础上对控制系统进行的测试实验,验证控制系统是否满足工艺要求。
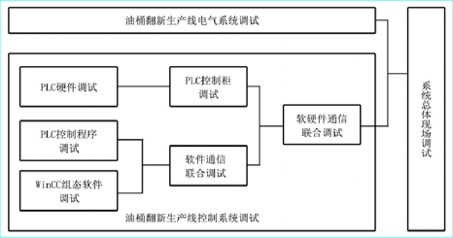
图5-1 统调试的整体构成
5.1 实验室模拟调试
本文主要从实验室模拟调试和现场运行调试两大方面进行调试工作。实验室模拟调试是通过仿真软件PLCSIM对设计完成的PLC程序进行调试。
本文现场位于天津市滨海新区天津瑞驰船舶机械有限公司厂房内,由于生产线的机械结构仍在优化阶段,所以控制系统的调试处于测试阶段,而且现场环境伴随着噪声、灰尘、高压电流等复杂恶劣因素,调试现场与实验室距离又远,通过PLCSIM进行实验室模拟调试的方式既安全又经济。依照系统调试方法分别设计了单独调试和联合调试两步调试方案。单独调试方案是应用PLCSIM软件分别模拟PLC和WinCC组态运行。单独调试内容方案如表5-1所示。
表5-1 单独调试内容方案

联合调试内容方案如表5-2所示。
表5-2 联合调试内容方案

实验室模拟调试需要的设备包括:计算机、触控屏、WinCC组态软件、S7-200编程软件、一条交叉网络线和一条MPI通信线等。调试目的是保证触控屏、PC与PLC的正常工作,尤其是三者之间的正常通信,验证三者之间I/O点分配的一致性。
5.2 控制现场调试
在模拟调试的基础上进行现场调试工作,现场调试是先对各模块进行单独调试。在模拟调试基础上,现场调试工作依照以下流程进行:
1)I/O点调试
具体工作方法是先进行计算机与PLC现场通信,将控制程序下载到PLC中;然后将PLC的状态调到STOP位置,通过计算机对程序中变量的控制验证生产线中I/O点是否与程序一一对应,实际工程中也可以从直流开关电源引出一条24V+的调试线,通过核对I/O点统计表用点动调试的方式验证输入输出是否一一对应。
调试过程中如果出现不对应的点位,需要从三个方面进行修正:第一方面要查看生产线的输入输出是否正确,原因可能出现在执行机构,例如气缸的气路接反,也可能会出现感应开关损坏等问题;第二方面要查看接入控制柜的外围线路是否正确或者有无松动等现象;第三方面确定控制柜的接线状况,例如PLC有无损坏,接线端口有无坏点或者松动等情况。在调试过程中会出现其他方面问题,例如调试过程中出现在三号控制柜的PLC指示灯非正常闪烁问题,虽然在调试中没有显现对程序运行的影响,但确是不可忽视的安全隐患。在排除PLC等硬件故障后,通过示波器找到了信号干扰是由于外围线路复杂,而其中几条信号线使用的是非屏蔽线,导致强电电缆对信号线形成了干扰,通过工程人员更换带屏蔽信号的信号线解决了信号干扰问题。
2)运行调试
因为调试过程会出现不可预测的情况,调试时需要3-4人配合工作。核对好输入输出点位后,运行程序之前先将PLC状态调到RUN,让PLC处于运行状态;然后按下控制柜的启动按钮,生产线按照程序自动运行。运行过程中出现紧急情况要按下急停,解决故障问题之后,先对生产线复位再运行。调试具体调试方法如下:
第一步,对生产线进行空载自动运行。
调试内容:工艺流程调试、紧急停止和复位。工艺流程调试是在空载条件下测试控制系统的运行是否满足生产线工艺流程;紧急停止要保证当生产线处于任何工作状态时都可以通过急停按钮让生产线停止运行,从而保证生产线不会因为故障而出现更大损失;复位要求要能满足生产线在复位过程中动作安全合理,例如在任意时刻复位时不能发生机械结构之间钩挂碰撞等现象。
调试问题:空载自动运行工艺节拍如下表5-3所示:
表5-3 实验调试工艺节拍
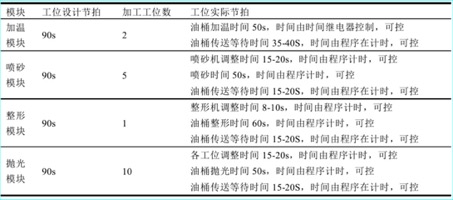
解决方法:系统整体的节拍要通过在程序中设定计时器的值控制输出的动作时间实现的。调试时流程工艺节拍紧凑,达到了厂方的控制要求,而存在与生产线设计时间节拍不一致的原因在于执行机构为气缸、油缸和电动机,因为气缸或油缸的动作时间由控制回路的压力决定的,解决方法是保证控制回路的压力在一定范围内即可让节拍符合控制要求,同时为保证各模块之间的配合稳定安全,留出了一定的时间余量。
第二步,对生产线进行加载自动运行。
调试内容:模块加载调试、全线加载调试。模块加载调试是对油桶加温模块、油桶喷砂模块、油桶整形模块和油桶抛光模块分别进行工艺调试,因为各模块之间是相对独立的,在空载运行调试符合控制要求的基础上,对某一模块单元进行加载调试不会影响到其他模块的正常运行;全线加载是在每个工位上都加上油桶,对生产线进行自动运行测试,测试生产线是否满足实际功能控制要求。各模块调试现场如图5-2所示:
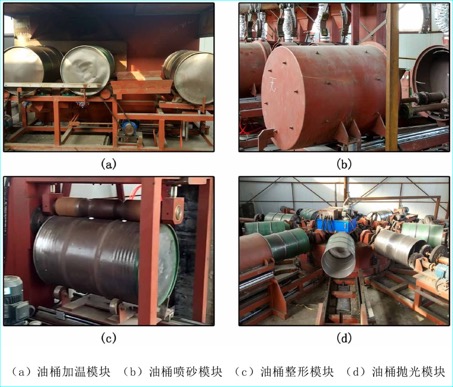
图5-2 各模块调试现场
调试问题:整体加载运行调试的问题较多,但主要包括两方面:生产线本体设计和控制系统设计。例如喷砂模块油桶的输送,在最初的设计中是依靠气缸控制翻桶架将油桶在喷砂机之间进行输送,这样的输送方式在程序复位时不能满足生产线控制要求,而且由于油桶的特性,在生产线运行过程中往往会出现油桶弹出工位的状况,更严重的是油桶输送不到位会导致喷砂机直接夹扁油桶。因此生产线本体的设计把翻桶的输送方式变为桁架机械手输送,从而达到了更好的运行和控制效果。
5.3 系统测试试验
试验设备与材料包括:油桶翻新生产线、生产线控制系统、待翻新的油桶100支;试验环境为天津市滨海新区天津瑞驰船舶机械有限公司设备厂房;试验人数13人。
试验方法:
1)生产线分配3名工人操作,油桶翻新生产线理论上一支油桶用时为33min,当油桶布满全线时加工节拍为每1.5min出一支桶,翻新50支油桶用时为33+1.5(50-1)=73.5min。以73.5min为时间定量,测试在规定时间内加工50支油桶,是否能到达“有效工作率=有效加工数/油桶总数≥80%”的测试指标,得出系统的有效工作概率。
2)选择10名油桶翻新工人对50支油桶进行人工翻新,每名工人分配10支油桶,以73.5min为时限,统计油桶翻新效率。下表5-4生产线加工50支油桶,试验10次得到的效率统计;表5-5为10名工人加工50支油桶,试验1次得到的效率统计。
表5-4 生产线加工50支油桶的有效概率
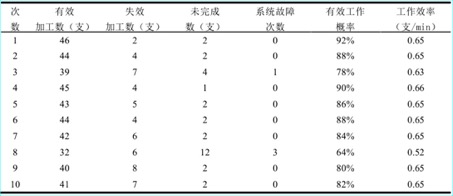
表5-5 人工加工50支油桶的有效概率
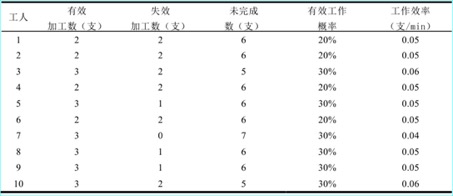
从试验数据中可以看出:
1)油桶翻新生产线自动运行对50支油桶进行10次加工测试试验,除了出现故障的两次试验,生产线的有效加工率达到80%以上,达到厂房研发阶段的控制要求。但问题也很明显:出现的两次系统故障,第一次故障原因是抛光工位机械手爪未加紧油桶,在抛光时导致油桶弹出失效;第二次故障是由于生产线加工时的振动两次导致传感器松动失效,一次由于油桶变形严重导致在整形机出不能整形失效。
2)与人工翻新相比,生产线的工作效率是人工翻新效率的10倍左右,有效工作概率是人工的4-5倍左右。试验结论:达到测试阶段阶段控制要求,控制系统还需要进一步从以下几方面完善:
1)模块的程序结构需要优化,通过这次试验暴露了一些工艺流程中存在的问题,如整形模块,在控制整形机时,由于整形机的整形辊子为悬臂梁结构,见图3-4,而且在整形时油桶处于单边受力的状态,导致油桶整形很不稳定,在控制上要对油桶采用分段整形的方式才能完成油桶整体整形。
2)生产线振动严重,容易导致控制系统失效,机械结构需要优化。
3)程序结构需要做调整,从试验中可以看出在正常工作情况下总是有两支油桶不能在规定时间内加工完成,需要进一步分析工艺流程优化程序结构,提高加工效率。
5.4 本章小结
本章完成了油桶翻新生产线控制系统总体调试工作,并在此基础上对油桶翻新生产线进行了测试试验,在废旧油桶翻系生产线现在的研发阶段内,实现了基于PLC的废旧油桶翻新生产线控制系统设计,但控制系统需要在以后的工作中继续从优化模块的程序结构方向上继续完善,提高系统的可靠性。
结论与展望
本文经过一年多的研究与实践,已基本完成了废旧油桶翻新生产线的各项功能控制目标。主要研究任务是PLC控制系统和监控系统设计与实现,并且经过了对系统的仿真调试及现场调试,达到了生产线控制要求。在项目研发中,经过对PLC,Win CC和以太网知识进行系统的学习,在调试系统过程中也积累了的一些实践经验,现总结如下:
1)根据油桶翻新生产线的功能要求和工艺流程,通过系统模块化设计方案解决了油桶翻新存在的设备功能单一、生产效率低等问题。
2)完成了废旧油桶翻新生产线控制系统总体方案设计。搭建了基于DCS的三层架构控制系统;利用MPI、PROFIBUS-DP、PROFINET等通信技术完成了系统层级之间的信息交互,提高了系统通信效率;采用上位机+PLC为控制模型,实现了控制系统可视化操作。
3)完成了该生产线的控制系统设计。以模块为单元对工艺流程进行深入研究,根据控制流程分配了系统的I/O点,设计了控制柜的整体结构,完成了控制柜硬件设计;开发了基于PLC的控制系统和监控系统:利用STEP7设计PLC梯形图程序,二次开发WinCC组态软件设计了该生产线的人机交互界面。
4)完成了系统调试与试验测试。基于PLCSIM仿真软件对该生产线进行了仿真分析,完成了对生产线设备的现场调试,通过对生产线油桶翻新测试试验的设计与研究,试验结果表明该生产线的工作效率可以达到每支桶1.5min,相比于人工每支桶15min,可以提高10倍左右的生产效率,而且提高了油桶的翻新质量。
本文对废旧油桶翻新生产线的研发完成了初步调试工作,目前实际运行的各项系统功能需要继续完善:
1)需要对生产线的实际加工情况进行跟进总结,进一步优化系统结构。
2)需要加强实时监控功能。引入CUD摄像头以后将现场情形直接反应到工业电视上,界面更加直观方便。
机械本体研发还存在很多问题,例如振动、噪声等需要解决;控制系统的设计也只是实现了研发阶段的功能测试,还需要跟随着生产线的本体优化继续升级,进一步保证系统可靠性同时,优化模块的程序结构,加快生产线加工效率。
|