机器人自动包装码垛生产线的研究与设计
文/林蒙丹 赵雪林
摘要:目的.为了提高固体颗粒物料的包装及包装袋码垛效率,降低企业工人的劳动强度。方法.以西门子PLC S7-1200 为控制核心,结合数字输入SM321、数字输出SM322 等模块,设计一套自动包装码垛生产线,用于粮食、化肥等物料的自动包装和码垛。通过设计伺服电机驱动、传感器输入模块、触摸屏人机交互界面等来实现对生产线的自动控制。结果.在完成生产线固体物混料装置、包装袋称量装置以及码垛机器人的基础上,进行化肥的包装实验,记录了包装袋称量误差以及码垛的中心误差,分析发现中心抓取误差小于0.2 mm。结论.该生产线系统可靠性强、包装码垛精度高,能够大大提高包装和码垛效率,具有很大的市场应用前景。
关键词:包装码垛生产线;PLC;上位机;码垛机器人
工业自动化技术的迅速发展,使得越来越多的传统型人工作业被智能化的机械设备所取代。自动化技术应用于包装码垛系统中,可用来提高粮食、化肥等颗粒物料的包装和码垛效率,发挥着越来越大的作用。我国人工包装的工作情况还较普遍,与发达国家相比还有较大差距。
包装码垛生产线主要应用于粮食、化肥等行业中物料的自动包装,实现包装过程的自动化。PLC因其抗干扰能力强、通用性好、可靠性高等优点,得到了广泛应用。文中采用西门S7-1200 作为控制系统的核心,配合数字量输入输出模块以及伺服电机驱动系统、称重系统等,设计一套自动包装码垛系统,共同完成生产线上的混料、称量、包装和码垛。
1 自动包装码垛生产线的工艺流程
包装码垛生产线中包括混料以及铰刀电机驱动系统、自动称量秤装置、倒袋和装袋以及输送系统、质量检测以及不合格包装袋剔除系统、包装袋输送系统、码垛机器人、伺服电机控制系统等。自动包装码垛产线基本组成见图1,其工艺流程可总结为:首先物料在混料系统中通过铰刀电机的转动进行充分混合,待物料混合均匀之后,自称量系统的料斗打开,物料进入包装秤的给料装置中。装料系统不断判断压力传感器的数值来检查当前物料质量,若当前物料质量已经达标时,传感器发出信号给PLC,此时PLC 控制装料系统停止装料。当自动装袋机完成上袋后,PLC 控制卸料门开启,给料装置中的物料落入下方的包装袋中,当物料全部落完后,PLC 启动自动折边机对装完物料的包装袋进行折边,然后通过封装装置进行封口。此后,质量检测装置再次检测包装袋的质量,并对不合格的包装袋进行剔除。若包装袋质量符合标准,则将包装袋通过打贴标签,最后到达输送流水线,然后通过码垛机器人按照事先设定的排列方式进行自动码放。包装码垛生产线工作流程见图2。
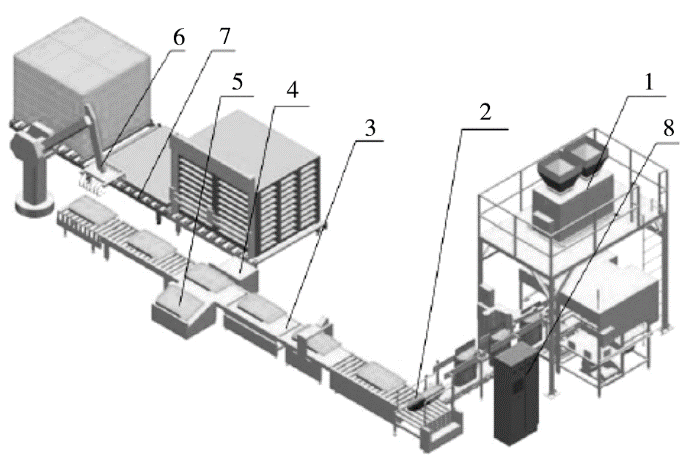
1.自动称量机 2.倒袋机 3.输送机 4.质量复检机 5.剔除机 6.码垛机器人 7.托盘输送机 8.控制柜
图1 包装码垛生产线示意
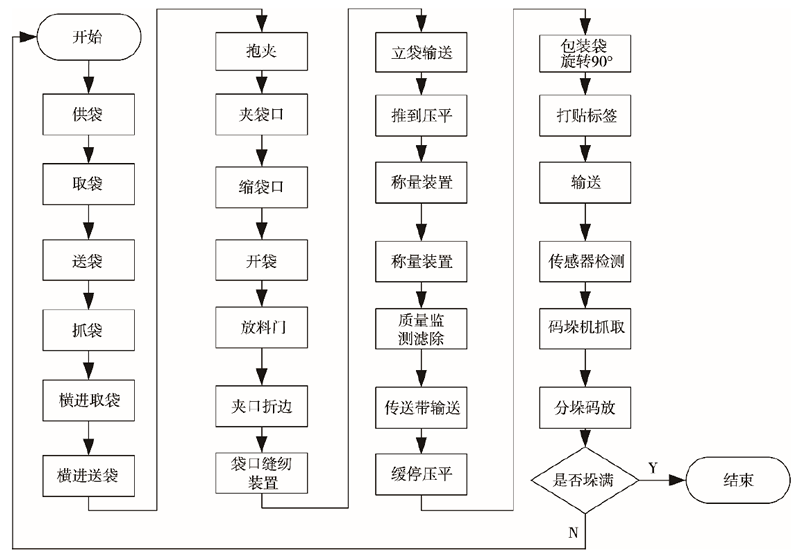
图2 包装码垛流程
2 包装码垛系统设计
2.1 包装码垛控制系统功能要求与组成系统
根据生产线的工艺流程,包装码垛控制系统应满足以下几个要求:各工序能够协调控制,能够使混料、称量、包装和码垛稳定可靠高速运行;动态响应性能好,可以随时根据各种传感器的信号进行实时反馈;理性化的人机界面, 便于工人操作以及监控。“HMI+PLC”的控制系统见图3。PLC 结合触摸屏、伺服驱动系统以及输送流水线和码垛机器人等各个功能模块,共同完成包装袋的抓取和自动码放。
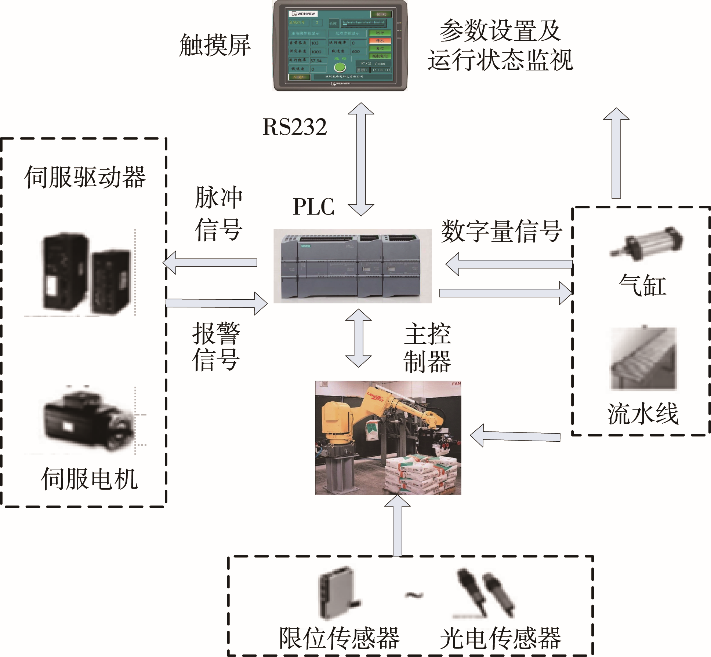
图3 包装码垛控制系统硬件框图
2.2 码垛机器人机械结构
在包装码垛生产线上,码垛机器人是一个重要的组成部分。文中应用的码垛机器人总体结构见图4。码垛机器人通过机身下面的底座来带动机器人的腰部结构进行旋转运动,机器人末端抓手部的伺服电机带动抓手绕自身轴旋转,同时另外2 个伺服电机还可以控制机器人末端抓手进行水平和竖直方向的运动,以不断调整抓手在流水线上抓取包装袋的位置。机器人的水平运动和垂直运动的驱动电机,都是通过控制同步带轮来控制滚珠丝杠,带动滑块沿丝杠运动,从而实现抓手的运动。
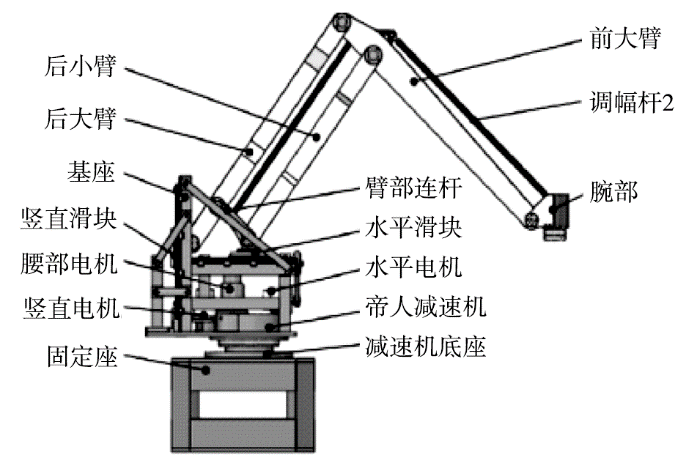
图4 码垛机器人结构
3 控制系统关键点设计
3.1 自动称量装置
自动称量装置主要由秤体和电子称量系统2 个结构构成。其中,文中采用的秤体部分又由混料机、储料仓、料门、称量斗、夹袋器、包装袋等组成。电子称量系统则是由1 号和2 号秤的称量传感器、仪表显示盘和触摸屏控制柜等组成,见图5。
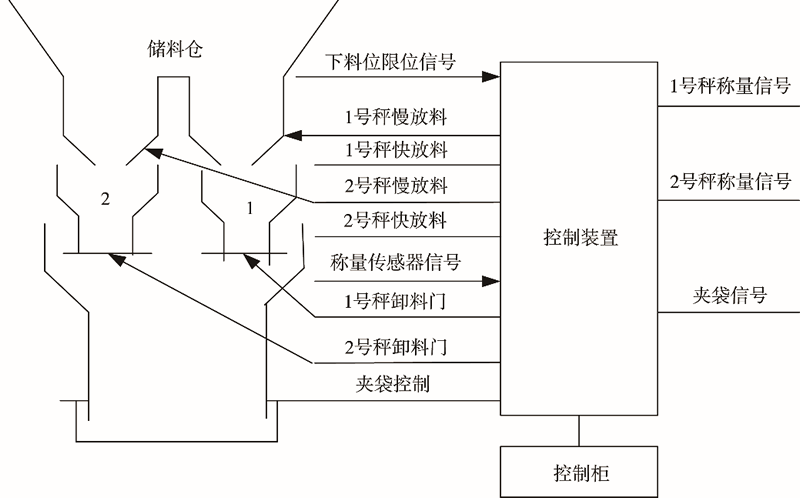
图5 自动称量装置
自动称量控制系统中,压力传感器的使用和实时信号检测是非常关键的一个环节。称量控制的示意见图6。压力传感器采集的信号通过模拟量输入口实时输入到PLC 中,而且称量过程中,PLC 控制器不断检测启动按键、停机键、夹袋夹紧、斗门状态等开关量信号。夹袋器、放料电磁阀、进料电磁阀和一些显示信号等,通过PLC 的输出量模块进行输出。称量斗门关闭以及夹袋夹紧检测,采用欧姆龙E2E-X2P1-N 接近开关作为信号输入,称量斗门、缓冲料门和夹袋,通过PLC 控制电磁阀来带动气缸工作。
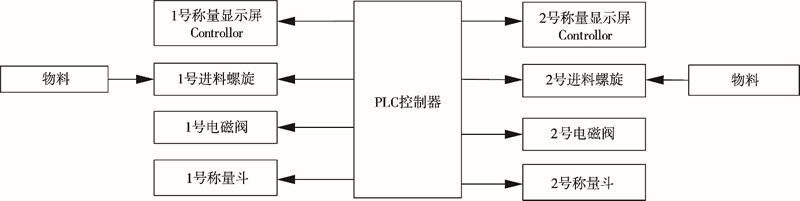
图6 称量控制示意
3.2 包装过程码垛机器人的控制算法
包装码垛生产线主要包括以下几个模块:自动混料及进料模块、倒袋及装袋模块、包装袋输送模块、质量检测模块、不合格包装袋剔除模块以及码垛机器人模块等。码垛机器人的控制流程见图7。首先,包装袋在完成包装之后,由包装输送传送带进行输送。当包装输送传送带光电传感器有信号到来时,说明此处有包装袋到来,若此时码垛机器人抓手已经准备好时,便可以控制机器人通过预先设定的程序进行抓取;若此时码垛机器人没有准备好,则传送带停止运动,等待码垛机器人的抓取码放。其中,若某个环节按下急停按钮时,则程序停止并且复位,等待下一步操作。
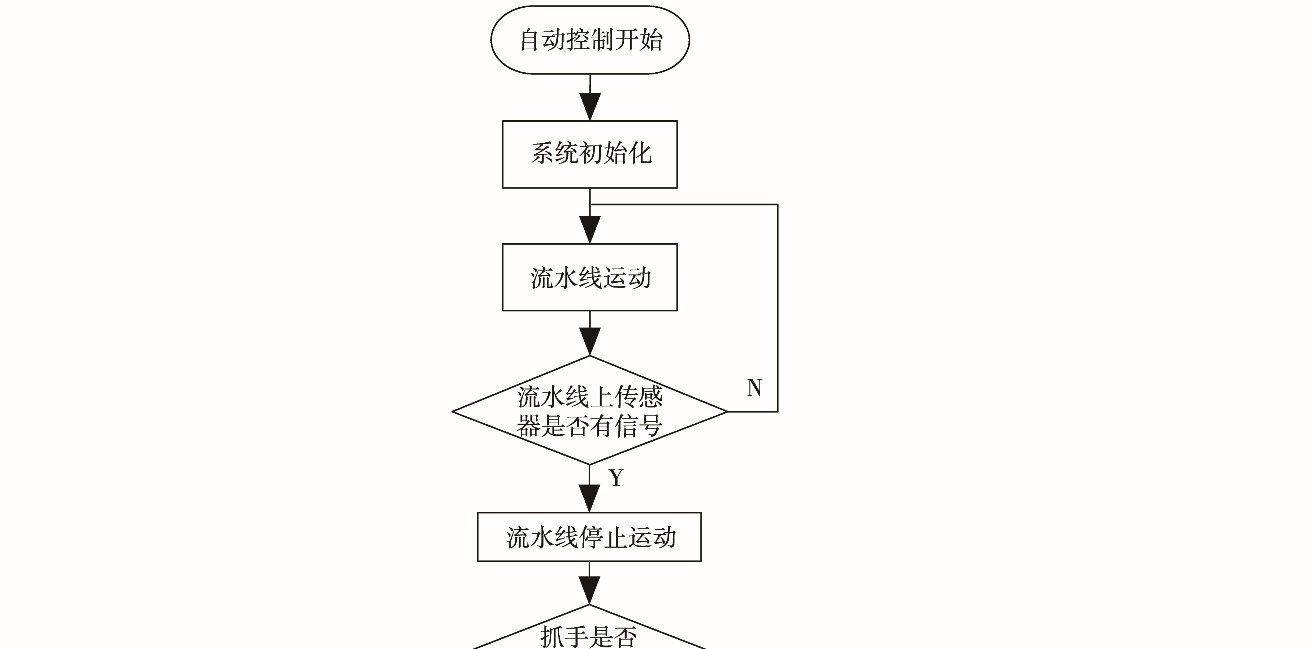
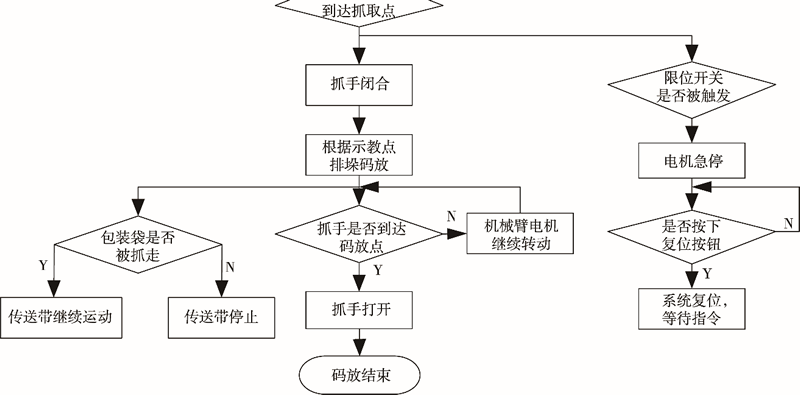
图7 码垛机器人的工作流程
3.3 伺服电机运动控制
为了对包装码垛过程中包装袋精确抓取和码放进行准确定位,系统采用伺服电机对传送带以及码垛机器人和混料机等的运动进行控制。伺服驱动器可以通过接收PLC 控制的伺服驱动器的外部脉冲和模拟量,实现对传送带速度和码垛机器人运动速度的定位控制。该系统要精确控制码垛机器人的运动,并通过接收到PLC 发出的脉冲的个数,精确控制伺服电动机的速度与方向。伺服驱动器的硬件连接电路见图8。
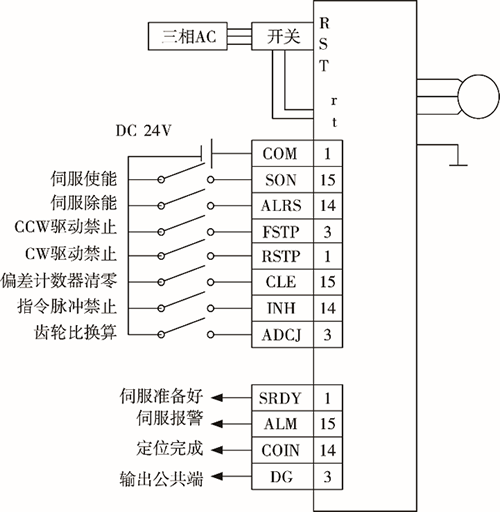
图8 伺服电机控制系统
为了保证电机的同步运行,在包装袋封口处、码垛机身转向处、底贴处安装欧姆龙接进开关,其信号通过SM321 采集并送给S7-1200,并且每个伺服电机后端接一个增量式旋转编码器,实现单回路PID 闭环控制,其控制原理见图9。
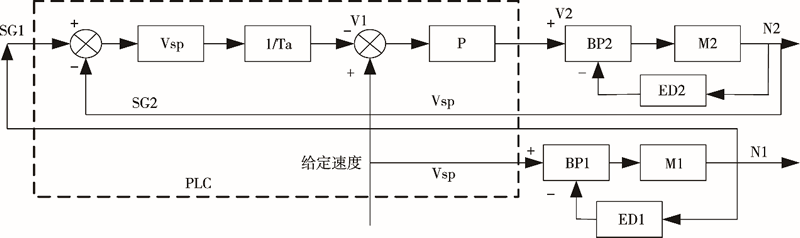
图9 控制原理
4 实验验证
4.1 码垛中心点误差实验
为验证自动包装码垛机器人在包装生产线上抓取包装袋的位置精度,进行包装袋码放位置的检测试验。以原点传感器为中心,码垛机器人在执行动作时的抓取位置与中心原点之间会存在超前、重合、滞后3 种情况,见图10。进行多次试验,重点试验了在不同的传送带速度下,随机测量间距delta 的数值,并进行数据记录,结果见表1。
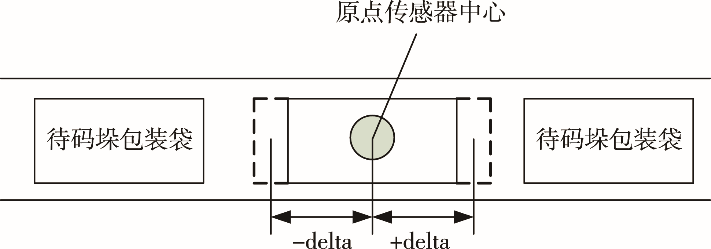
图10 包装袋与码放中心位置示意
表1 包装袋中心点误差统计(mm)
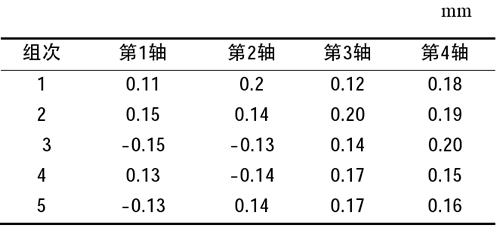
实验前,首先对码垛机器人的抓取点和码放点进行示教,以码垛机器人机身所在的位置为绝对位置零点,以包装袋和堆垛码盘的9 个位置点进行示教。此时控制器将抓取点和每个码放点的脉冲和方向记录下来。实验过程中,当光电传感器检测到包装袋流水线上有包装袋运输到码垛机器人的抓手末端下方时,控制器将抓取命令传送至执行器,控制抓手末端抓取包装袋。
表2 实验结果
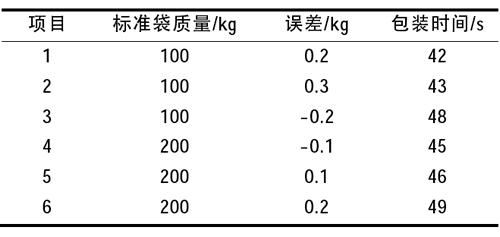
通过表1 的数据分析发现,码垛机器人在抓取包装袋的中心点位置时,误差范围为0.11~0.20 mm,平均误差在0.17 mm 左右,误差小,控制精度高。由此可以看出,设计的自动包装码垛机器人能够实现包装量进行实时检测,通过不断与标准质量进行对比,来达到自动称量的鲁棒控制。
5 结语
文中设计了用于固体颗粒物的自动包装码垛生产线,能够长时间稳定运行。在完成生产线固体物混料装置、包装袋称量装置以及码垛机器人设计的基础上,进行了化肥的包装实验,记录了包装袋称量误差以及码垛中心误差。结果表明,设计的生产线可靠性强、包装码垛精度高,能够大大提高包装和码垛效率,具有很大的市场应用前景。 |