静电粉末喷涂设备的发展历程
文/金浩
近年来,政府大力推进环保事业,静电粉末喷涂技术作为喷涂领域的绿色技术,符合VOC节能减排等环保政策的要求,越来越多的受到了客户的青睐。本文结合当前的行业状况,对静电粉末喷涂设备的前身,现状和趋势进行阐述,期望帮助读者加深对静电粉末喷涂技术的了解,从而能够充分应用该技术为国家环保政策的落实,“中国制造2025”的推进添砖加瓦。
一、静电粉末喷涂原理
1、静电粉末喷涂
对于我们采用的静电喷涂的方式而言:工件需要接地,即零电位,不带电荷;粉末由静电喷枪进行充电。从图1可以看出,粉末被喷枪喷出并在喷枪出口区域被充电,同时被施工的工件必须在接地的状态下。雾化的粉末颗粒在空气动力、重力和电场力的共同作用下,异性相吸,朝工件飞去,并因为带有负电荷而吸附在工件的表面。
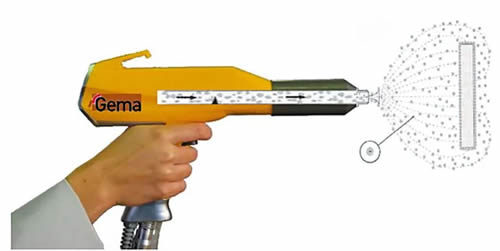
图1 静电粉末喷涂示意图
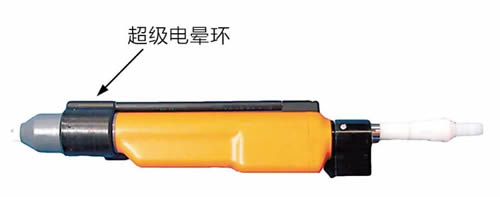
图2 超级电晕环
2、超级电晕环
粉末充电的过程之后,我们可以采取一些措施来影响喷涂结果,使其往我们希望达到的喷涂品质靠拢。超级电晕环(图2)就是这样的一个重要部件,作用于影响喷涂效果的因素。除了一些基本的组成:工件、输送链、喷枪、控制器,我们还在工件上连接了一个电流表,同时将另一个电流表连接到了超级电晕环装置上,如图3所示。
图4中的红色线条描述了在粉末喷涂进行的过程中,自由电子因为有超级电晕环的存在而被带走,有效规避了其对工件喷涂效果的影响。标注的蓝色小点则是被接地中和的自由电子。
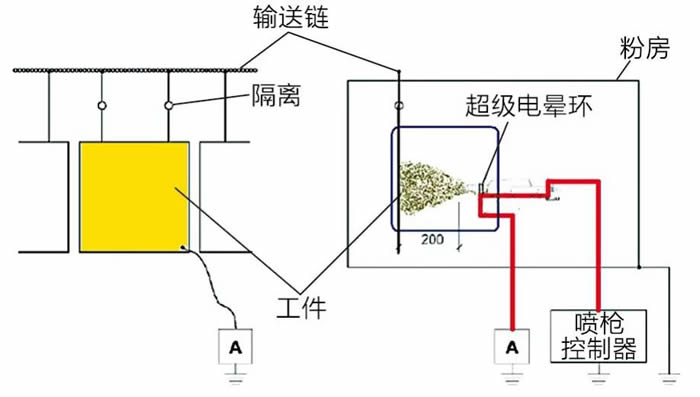
图3 超级电晕环工作原理图(a)
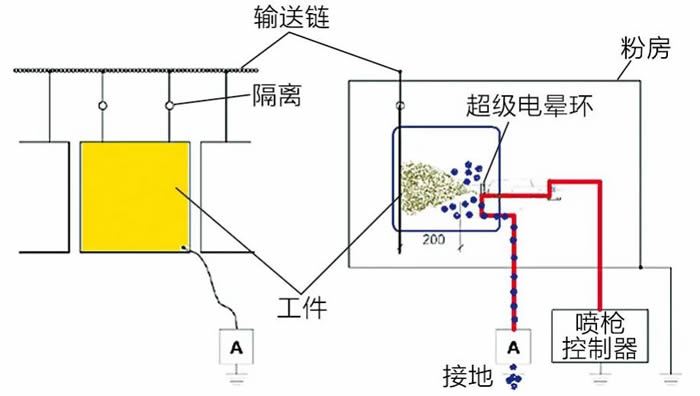
图4 超级电晕环工作原理图(b)
通过测量分析,我们可以看出使用和不使用超级电晕环的区别。在同样的施工条件下,超级电晕带走了大量的自由电子。测得的电流值明显的表现出了差异,甚至达到了10倍之多。原本应该会停留在工件表面的这些过多的电子占据了空间,造成边框,橘皮等不良效应。超级电晕环的应用意义在于将大量的自由电子带走,消除橘皮、边缘过厚等常见的粉末喷涂瑕疵,帮助我们获得更均匀的涂层效果。当然超级电晕环的使用也会存在一些不适用的场合,这就需要工程师帮助客户调节来获得最佳的喷涂结果。
静电喷涂中还有一个普遍存在的现象,称之为法拉第效应,即对于一个金属笼,静电场是无法穿透的。现实中如果存在小于90°夹角的工件,法拉第效应很大程度上就会影响该工件的上粉率。
屏蔽场会把带电的粉末颗粒挡在外面,那么这个时候超级电晕环就能彰显它的效力,从而大大减少飞向工件的自由电子,这意味着法拉第屏蔽的场强也相应地降低了。粉末颗粒得以进入到我们称之为死角的位置从而取得较满意的喷涂效果(图5)。
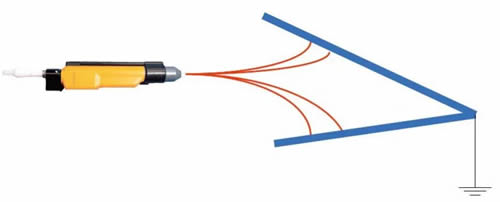
图5 法拉第效应
二、静电粉末喷涂设备
1、喷枪
静电粉末喷枪是静电粉末涂装设备中的重要组成部分,也是粉末涂装的关键设备。回顾整个静电粉末喷枪发展历史,1967年,瑞士金马公司研发出世界第一把静电粉末喷枪(图6)。当时,高压发生器为外置式,体型比较庞大,操作性和灵活性也相对较差。1973年,瑞士金马公司革命性地将高压静电发生器集成到了喷枪的内部(图7)。
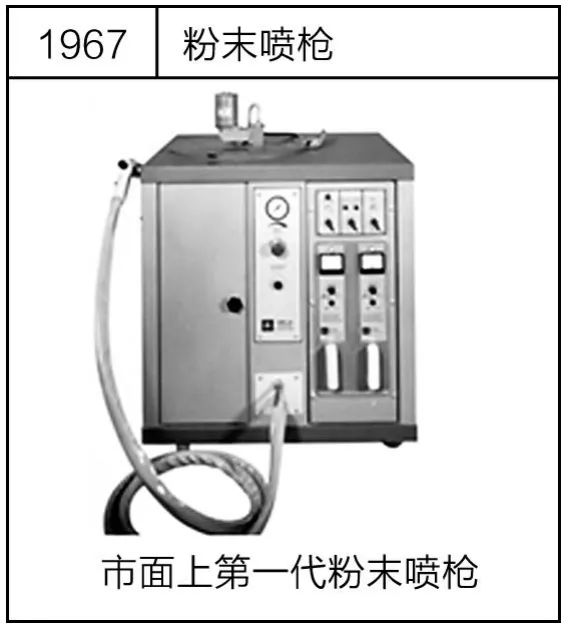
图6 第一把金马喷枪
这一突破性的研发,成为了静电粉末喷涂设备发展历史上重要的里程碑,沿用至今。
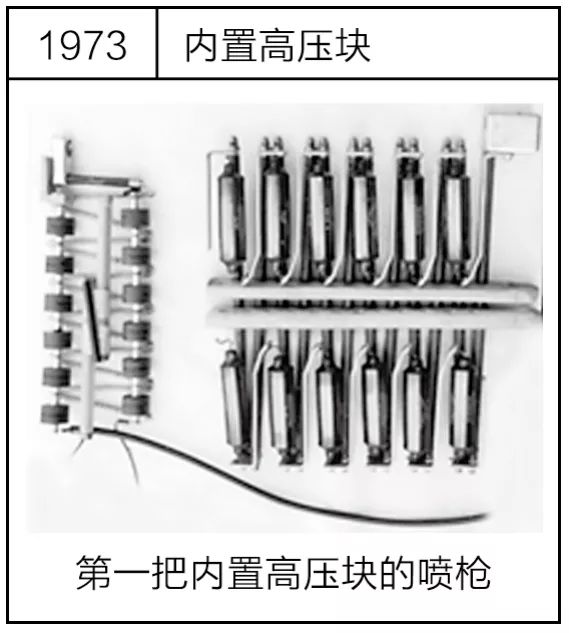
图7 第一把内置高压块的金马喷枪
前文所提到的法拉第屏蔽效应,会很大影响到复杂工件喷涂的上粉率。但是精准电流充电技术能够通过高精度的闭环控制十分精确的设置到10μA以下,并且以0.5μA为单位进行调整,电流甚至能控制到1μA以下。该技术能够有效地针对不同形状的工件,设定最精确的参数,达到最高的一次性上粉率,并且还能够有效地克服法拉第屏蔽效应,解决死角位的喷涂,同样也保证了粉末喷涂的均匀性。
喷枪控制器方面发展至今,也取得了许多技术性的突破。20世纪90年代末,所有静电喷枪的控制器都采用旋钮式的控制技术,操作界面非常复杂,并且没有程序储存功能。随着研发的进步,如今控制器都采用数字化的参数控制,屏幕界面采用液晶显示器,操作方便,并且拥有255组程序储存功能和自动检测代码报错功能。
数字化阀门控制技术(图8),其原理是通过数字化步进马达控制针阀的进退,精准的控制压缩空气量的大小,达到最精确的粉末输出量和最好的喷涂效果。
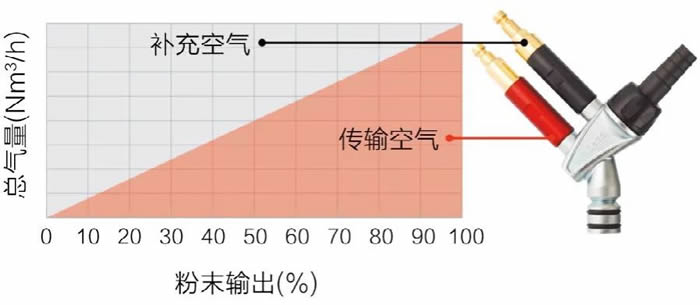
图8 数字化阀门控制
2、粉泵
粉泵,与粉末发射器共同应用于喷涂设备。粉泵的主要作用是从大旋风/后过滤系统中回收过喷粉末,并将废粉重新输送回新粉添加装置。第一代粉泵(图9)的设计与脉冲相关,为了减少脉冲,第一代粉泵配备了2倍延迟工作腔室。目的是保持短时间稳定的出粉率,混合粉末会流经整个粉管的内径。这种先进的设计理念已经取代了传统的以重力为工作原理的密相粉泵技术。其优势为容易自动清理、双向传输、大粉量传输。
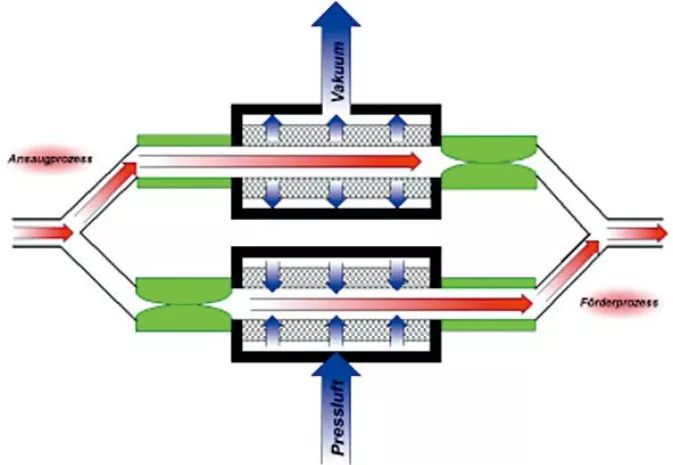
图9 第一代粉泵

图10 最新一代的粉泵采用的是双腔式挤压阀技术
最新一代的粉泵采用的是双腔式挤压阀技术(图10),数字化控制,含有自动清理模式、双向传输。粉末输送能力3.5kg/min至5kg/min,最远传输距离可达25m。同时设计紧凑,便于操作且维修保养十分简便。其自动清洁模式能适用于快速换色系统,包括金属粉末和搪瓷粉末。
在粉末传输方面,粉末发射器的设计也有了很大的变化。最新设计的135°角粉末发射器能够更好地提高粉末喷涂时的雾化效果,减少粉末输送的阻力,降低文丘里管的磨损,提高其使用寿命。
从静电粉末喷涂最初研发至今,一直有个核心问题:“如何将粉末持续不断且恒定地传输到喷枪?”粉末发射器也在不断被改进。普通的粉末发射器提供了良好的、持续不断的分流,粉量易于调节,易于清理,维护成本也较低。其不足之处也显而易见:粉末传输能力受粉管长度影响较大,出粉量大小受文丘里管磨损的影响等。为此,瑞士金马公司首先将密相阀技术应用到了粉末发射器上,研发了真正意义上的粉泵,用于将粉末传输至喷枪。
直排双腔室的内部结构,利用少量的压缩空气结合挤压阀技术,达到持续稳定的出粉量。大大减少了压缩空气的使用量,并提高粉末传输效率、延伸传输距离。其技术原理为:第一步,先关闭副腔的挤压阀,使得主腔室变成真空状态,配合少量的输送空气将粉末传输到主腔室内。第二步,关闭主腔室的挤压阀,打开副腔室的挤压阀,让粉末传输至喷枪。完成整个过程只需0.33秒,也就意味着1秒钟内,能够完成3次粉末传输的步骤。
密相阀技术的运用,使得粉末传输至喷枪的优势更加明显:传输频率高、出粉量持续稳定、压缩空气消耗少、粉雾柔和,同时配合使用的粉管长达30米。
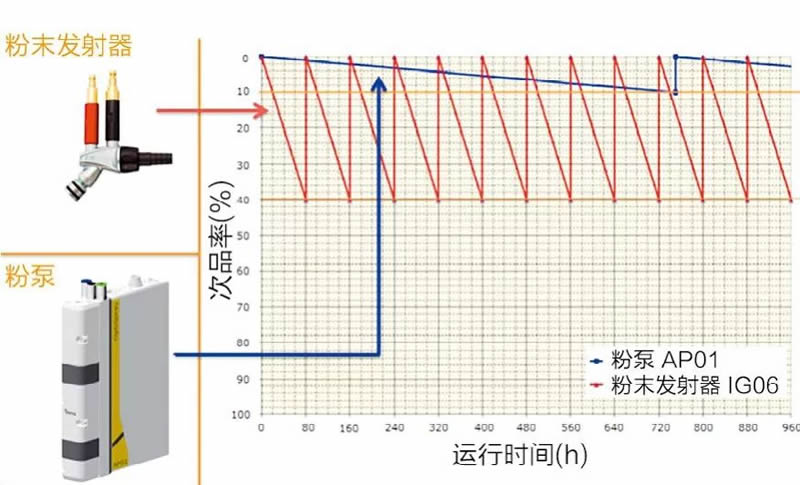
图11 粉末发射器与粉泵的易损件使用时间对比
易损件的使用寿命一直都是最终用户关心的重点之一,如图11所示,粉末发射器与粉泵的易损件使用时间对比,可以很明显的看到:粉泵易损件的使用寿命远超于粉末发射器。同时我们还能看到一个至关重要的方面:表格纵向表示易损件的损坏程度,横向表示操作时间。由此可以看到,即使在使用750小时后,粉泵的易损件磨损程度仍然远小于粉末发射器。众所周知,粉末发射器的易损件为文丘里管,文丘里管的磨损程度直接影响到粉末输出能力。恒定的粉末输出量对工件表面的喷涂均匀性起着至关重要的作用。也就是说,粉泵技术能够保持更稳定的粉末输出量,达到更好的喷涂效果。
3、供粉中心
供粉中心集粉末回收装置、自动粉筛和粉末流化功能于一体,主要负责将粉末输送到喷枪同时通过抽吸管路,自动进行反吹清理和一系列电气自动化控制。
在粉末涂装发展的早期阶段,粉桶是抽吸粉末和粉末喷涂前进行流化的主要部件。随着粉末涂装行业的发展,为满足大规模涂装的需求,国内开始在粉桶上增加电磁振荡或搅拌装置,但仍然无法有效解决粉末抽吸过程中由于粉末堵塞产生的不出粉等问题。此外,粉末的流化效果不佳或者回收粉末与新粉混合配比不佳都会直接影响喷涂效率和喷涂效果。
特别是近年来,粉末喷涂作业中“多色喷涂”成为了主流,而传统的粉桶换色需要的清理时间长、换色难度大且换色过程中产生的粉末浪费以及粉末外溢等环境污染问题,引发了喷涂行业对喷涂效率、粉末成本以及环境污染问题的思考。
作为一种新型的智能供粉中心,需要将粉末连续、均匀、可定量地输送到喷枪,自动实现新粉与回收粉末之间的混合配比并投入循环使用,且整个过程中粉末振动以及流化需要密闭并且安静,以防止粉末外溢污染和噪声污染(工作过程噪声应小于75dB,换色过程噪声应小于95dB)。
供粉中心需要能够适应粉袋或采用原包装粉箱,以便保持流化均匀。供粉中心的智能化发展将体现在能够识别粉末可用量和具备自动控制新粉添加功能,并具备脉冲式反吹装置,以确保喷枪与管路的自动清理更为便利和迅捷,尤其是在粉末换色过程中兼顾维护厂房环境。
智能化供粉中心主要配置的特征如下:
⑴粉袋圆锥体或振动平台能够支撑25kg粉袋,通过粉管与粉末振动泵来实现粉袋流化。
⑵具备高精度粉末位置检测装置,实时检测粉末的当前位置。
⑶密闭式粉末流化箱和自带粉筛相互配合使用,能够支撑6~7kg粉末并满足24~30把喷枪同时作业。新粉与回收粉能够按照程序设定比例进行循环使用。
⑷超声波振动筛可支持不同尺寸的筛网孔径。
供粉中心采用程序控制,通过触摸屏操作(图12),设备作业的实际状态、报警信息、参数设置、手动或自动操作均可选择,也可以根据工件的不同设置多项参数。当供粉中心预测粉末不足或无粉时,需要及时发出警报,提醒操作人员进行加粉或更换粉箱,同时能够记录系统信息。当系统出现故障或者参数错误时,能够及时显示故障或警告信息。需要换色时,只需将吸粉管接到粉末回收接口,操作界面按下“粉末回收”键,即可简单实现“一键换色”。
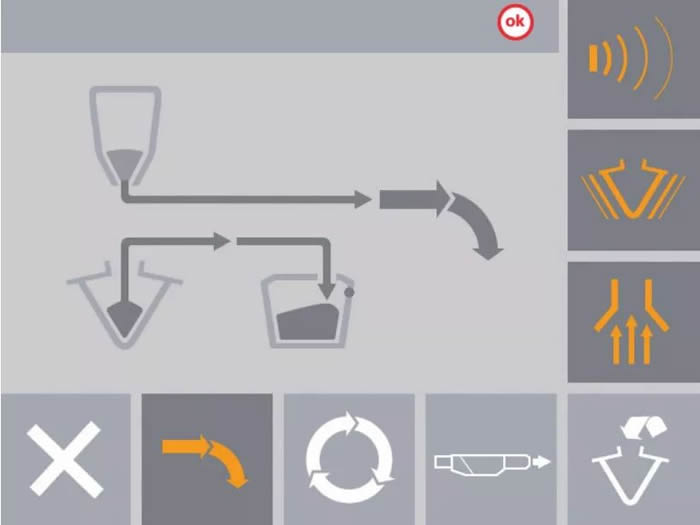
图12 供粉中心的触摸屏
4、粉末回收系统
与传统的溶剂型涂料相比,粉末涂料具备可回收利用的优势。粉末喷涂作业必须控制在一个半封闭的环境中进行,同时对于喷涂作业人员和环境要给予充分考虑。为提高回收系统的效率,相关政策执行力度必须加强。
粉房将整个喷涂工艺包裹在一个相对封闭的环境内,经过精确地计算以及合理的制作加工,粉末在其中不会外溢,不会对环境造成污染,同时可以循环使用。通常的粉房材料有PP、PVC材料等,近年来PP材料因其易燃特点在欧美已被禁止使用。
通常的回收装置有滤芯式或旋风式两种形式。滤芯式回收依靠高性能过滤装置(滤芯),能够回收使用99%以上的粉末喷涂量,其结构简单,维护方便。旋风式回收装置主要在换色粉房系统中使用,由于它能够带来较快的换色效率,所以换色需求频繁的企业一般都会选择使用旋风式回收装置。
静电粉末喷涂工艺中采用的回收方法常见有两种,即单级回收和双级回收。单级回收只采用过滤器完成粉末回收,双级回收是利用旋风分离器与过滤分离器相连接,形成回收系统。单、双级回收系统由于各具特点,因此应用范围也有所不同。
一般来说,单级回收系统适用于产品颜色种类少(一般不超过两种)的企业,在这种情况下,如果能充分满足客户对粉末粒度、空气湿度和温度方面的要求,则单级回收系统比双级回收系统具有占地面积小,设备能耗低、粉末利用率高等优点。但是,单级回收系统只有一级回收,因此不可避免存在不少缺点。双级回收系统则是采用旋风分离装置与滤芯共同完成粉末回收工作,合格的回收粉末被收集至旋风下的回收粉桶,超微粉则被选送至双级回收下的收集粉桶。因此具有换色方便,滤芯损耗低和自洁的优点。单、双级回收系统特点的详细比较如表1所示。
由于单级回收系统存在诸多缺陷及安全隐患,因此在1995年由劳动部、国家技术监督局颁布的《涂装作业安全规程—粉末静电喷涂工艺安全》国标第5-1-3条明确指出:“不宜使用喷粉室与易积聚粉末的单级过滤式回收及交换装置组合一体的喷涂装置”。
大旋风即旋风分离器,通过入口结构的设计使得气流切向进入旋风分离器内并产生旋转运动。入口一般为矩形截面。气流在做旋转运动的同时,沿着分离器的外侧空间作向下运动。在分离器的椎体段,内部的气体缓慢进入分离器内部区域,然后气体沿椎体中心轴向上运动。由此,锥体内将产生双漩涡,即沿中心轴向下运动的外漩涡和向上运动的内漩涡。所以,带有粉末的混合气体将在旋风分离器内离心力作用下沿边壁运动,粉末由重力作用向下进入粉末排尘口,随后净化气体从分离器的顶部排出。
从运行的旋风分离器中排出粉末,利用回转输送装置(密相输送方式),每隔一定时间,将粉末利用空气从中间管通过输送软管输送到粉末容器。在粉末输送过程中,在输送软管中必须存在一个小的空气运动,以免发生堵塞。此处一般不建议采用传统文丘里粉末发射器来传输回收粉末,因其结构原理会造成对于旋风内部压力的改变而影响旋风分离效率。
表1 单、双级回收系统比较
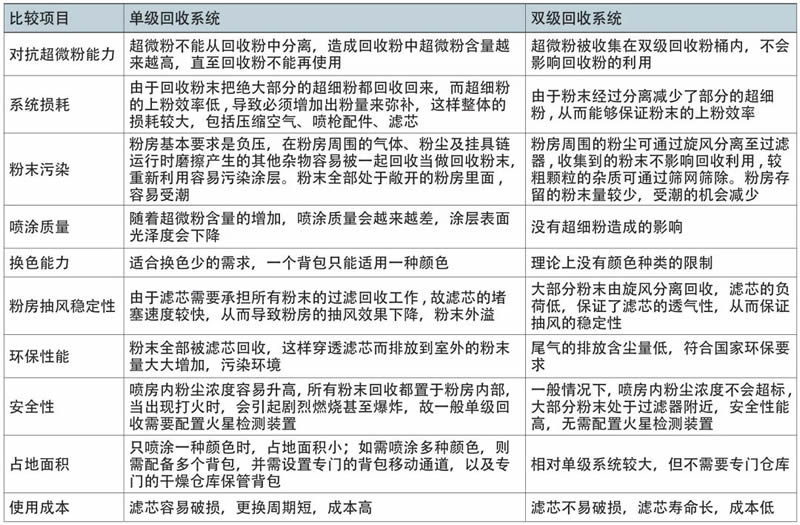
三、进展
从客户的实际需求、产业发展、新材料新工艺的成熟应用以及环保法规的要求出发,我们可以预见静电粉末喷涂设备未来的发展路线以及生产方式的转型。以往大企业高量产的模式正在悄然变化,利润降低,成本优势不再,这也是大势所趋。但涂装生产仍然不可缺少,由此产生的喷涂代工需求显而易见。如果对比国外行业,我们发现国内喷涂代工行业的规模以及水准都相差很远,绝大部分以手工生产为主,品质和产能都难以保证。而眼前国家控制污染的举措又把这些低门槛的作坊型企业拒之门外。不过长远来看,这有利于代工行业的升级换代和未来的健康发展。我们呼吁国家对此增加关注力度并提供政策扶持,让专业的厂家做专业的工作,减少不必要的浪费和投资,并完善品质和提高效率。
国家从环保角度出发大力发展环保型表面前处理、水性涂料涂装、粉末涂料涂装、光固化涂料涂装和高固体分涂料涂装等技术,对于粉末喷涂行业来讲,这将是一个前所未有的机遇。除了传统的粉末喷涂领域之外,很多新行业将会由溶剂型油漆转型到粉末喷涂上来,这个趋势尤其值得大家关注。
|