提高卷封滚轮使用寿命的研究
文/郭松
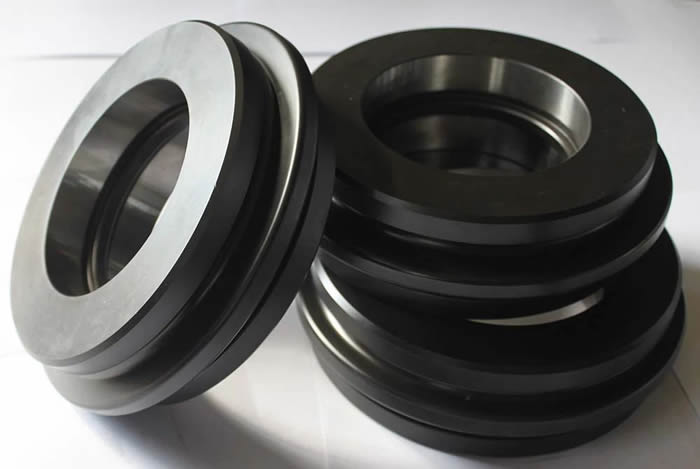
摘要:通过对卷封滚轮的失效分析, 对由Cr12MoV 钢制造的金属容器卷封滚轮采取预处理(反复镦锻+球化退火+调质)、热处理(淬火+深冷处理+回火)、曲线精度控制、表面处理等多项措施, 可有效地提高其使用寿命。
关键词:金属容器;卷封滚轮;热处理;深冷处理
金属容器卷封滚轮材料主要采用Cr12MoV 钢。由于目前各企业所采用的卷封滚轮的卷封曲线及材料热处理方式的不同, 滚轮寿命也各有不同, 与国外相比还有较大差距。本文从研究热处理工艺、曲线形状、表面处理工艺等诸方面着手,探讨提高卷封滚轮使用寿命的问题。
1 卷封滚轮的失效模式
图1 为卷封轮沟槽表面损伤的微观形貌。从图中可以看到, 国内外卷封轮沟槽表面均存在点状麻坑剥落, 进口轮的麻坑较细小。国产轮沟槽表面还存在较为明显的划道及犁沟。
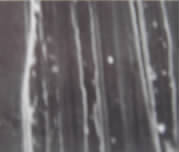
国产滚轮:Cr12MoV
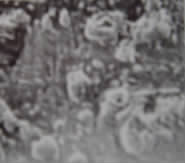
进口滚轮:D2
图1 卷封滚轮沟槽表面损伤形貌(扫描电镜片) 2000×
国产轮犁沟粗而深, 这与国产轮材质较差有关, 如硬度低、碳化物分布不均、碳化物颗粒粗大等明显的塑性流变痕迹及舌状花样, 表明粘着磨损的存在。
卷封滚轮在封口作业时, 受力情况比较复杂。沟槽曲线表面在无润滑的状态下要承受钢板强烈的刮、挤和摩擦磨损。由于材料本身中硬脆碳化物颗粒的剥落或硬颗粒在压应力作用下, 在其工作表面(曲线沟槽表面)形成较深的的空洞及其周围基体金属的碎裂而引起磨粒磨损。在磨粒磨损的同时, 相应摩擦副表面某些磨损处, 在高挤压力的作用下, 氧化膜遭破坏后而产生金属粘结。这些粘结点处的强度往往高于基体金属的强度。在随后的相对滑动时,破坏便发生在强度相对较低的地方。粘结的不断形成和破坏, 就造成了粘着磨损。
国外卷封轮沟槽表面光滑, 微观形貌呈片状花样, 不存在犁沟与舌状花样特征, 表现为典型的氧化磨损。众所周知, 磨粒磨损, 粘着磨损的磨损速率大大高于氧化磨损, 因此, 国产卷封轮曲线沟槽表面的失效特征主要为:磨粒磨损+粘着磨损+氧化磨损。
2 卷封滚轮的热处理工艺
2.1 原材料的锻造与退火
Cr12MoV 钢的优点是高的耐磨性、高抗压强度、微变形、高淬透性, 油冷临界淬透直径达φ80~200mm。缺点是, 由于它属于莱氏体钢, 碳化物大且分布不均。为此, 可进行合理锻造加以改善。
表1 锻造工艺
材料
|
始锻温度
|
终锻温度
|
冷却
|
Cr12MoV
|
1080~1120℃
|
850~900℃
|
砂冷
|
改锻时宜采用反复镦锻的方法, 单次锻造比为2~5, 总锻造比大于10。锻造工艺为:
锻后进行退火处理, 主要目的是消除内应力, 调整碳化物形状, 获得合适的硬度, 以利于随后的加工, 同时也为最后的热处理提供良好的组织基础。Cr12MoV 的退火工艺如图2 所示。图3 为球化退火后的组织。
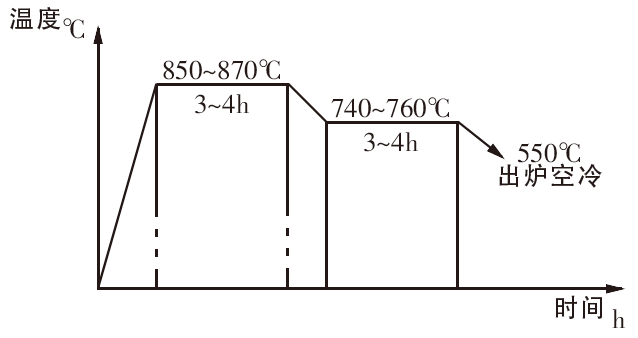
图2 Cr12MoV 钢等温球化退火工艺
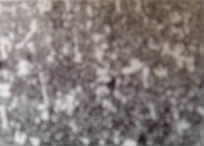
图3 Cr12MoV 钢球化退火组织500×
2.2 调质
卷封滚轮粗加工后, 增加一道调质预备热处理, 对提高使用寿命十分有利。由于高温加热时弥散碳化物的析出, 不但能进一步改善碳化物的分布, 而且能够提高钢的强韧性。大量的试验结果表明, 采用高温固溶微细化预处理,对于提高钢的强韧性能效果较为显著。因此调质淬火温度通常要比常规高30~50℃, 高温回火温度取720~760℃。
2.3 热处理与深冷处理
基于对卷封模具失效原因的分析, 在所有要求的性能中, 最重要的是抗压性(变形能力)和耐磨性。热处理工艺的制定主要围绕这两点来进行。
Cr12MoV 钢淬火温度通常有低、高两种。采用低温(950~1000℃)淬火和低温回火可以获得高硬度和较高的韧性, 但抗压强度低;采用高温淬火(1100℃)及二次硬化的高温回火(500~520℃)可获得较高的硬度和抗压强度, 但韧性太差。研究表明, 采用中温淬火(1010~1060℃),施加冷处理和低温回火, 可大幅提高模具的寿命。冷处理的作用大体可归结为两点:一是促使残余奥氏体向马氏体转变, 使材料的强度、硬度增加, 塑性下降;二是马氏体基体的变化(微细弥散碳化物的析出、晶体内镶嵌块细化、位错密度增加), 第二类残余应力减少, 马氏体畸变减少。所有这一切增加了裂纹扩展所需能量, 使材料韧性恢复。
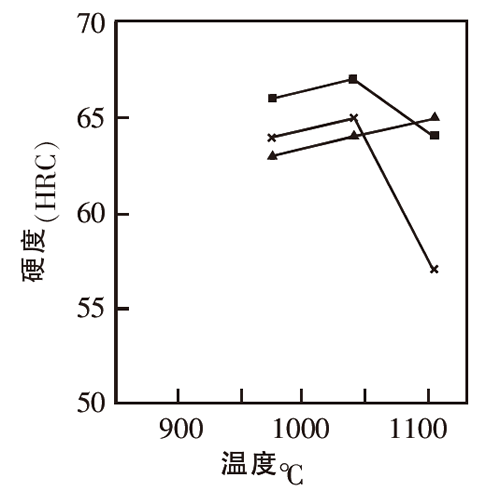
图4 Cr12MoV 钢淬火温度和硬度的关系
图4 为Cr12MoV 钢淬火温度与硬度的关系。1040℃淬火可获得最高的硬度(65.9HRC), 冷处理后可进一步提高到67.6HRC,经170℃左右回火后硬度调整到65HRC 左右。
冷处理温度对硬度的影响(见图5), 随冷处理温度的降低, 硬度逐渐提高。
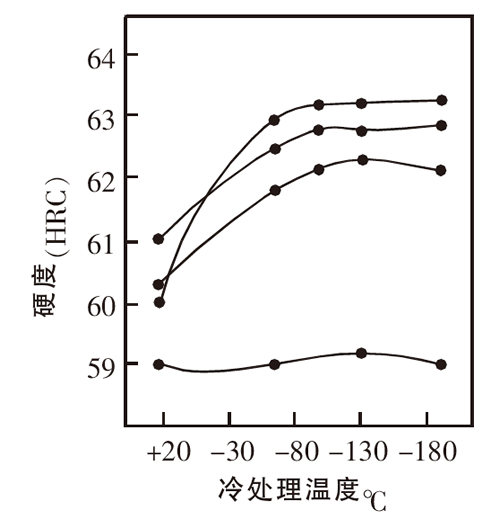
图5 冷处理温度对Cr12MoV 钢硬度的影响(冷处理后200℃回火)
由于材料的抗压强度与硬度存在以下关系:
σbc=120×[HRC]-4440(MPa)
可见硬度越高, 抗压强度也越高。研究指出, 如图6 所示, 冷处理可使耐磨性显著提高。淬火温度越高, 冷处理后的硬度也越高。而中温淬火加热, 可以较多地溶解合金碳化物,使基体中存在较多的合金元素, 以充分发挥合金元素的有利作用。中温淬火的抗压强度比低温淬火要高得多也反映了这一点。
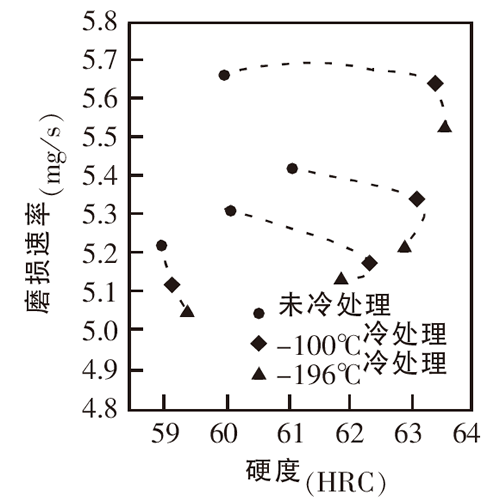
图6 Cr12MoV 钢在不同淬火温度和冷处理条件下,硬度与磨损速率的关系
2.4 热处理工艺
根据上面对Cr12MoV 钢材料的热处理工艺分析, 对卷封滚轮实施如图7 的最终热处理工艺:
热处理后的金相组织(图8)为:隐针马氏体+碳化物(大颗粒共晶碳化物+细小弥散分布的二次碳化物)+少量残余奥氏体, 晶粒度为9~11 级。
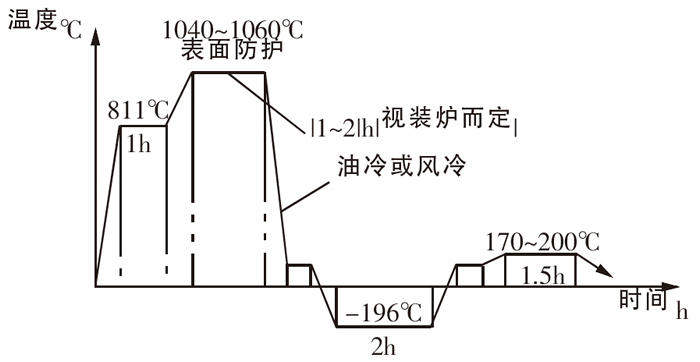
图7 Cr12MoV 钢卷封轮最终热处理工艺
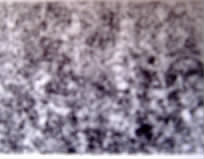
图8 Cr12MoV 钢卷封轮热处理后的组织500×
3 卷封曲线
在卷封技术中, 若第一道卷封不合格, 往往很难靠第二道卷封调整过来。因此, 第一道卷封曲线的设计非常重要。一条好用的一道卷封曲线, 不光能卷封出良好的卷边, 还可以延长模具的使用寿命。如图9 所示, 图中曲线1为理论曲线, 曲线2 为卷封滚轮的实际曲线,曲线3 为磨损后的失效曲线, δ 为实际曲线与理论曲线的偏移量。δ1为实际曲线至失效曲线的可磨损量, δ2为理论曲线至失效曲线的可磨损量、由于δ2>δ1, 使用寿命可大大提高。换言之,实际曲线(曲线2)越接近理论曲线(曲线1), 卷封滚轮的使用寿命就越长。在理论上, 卷封曲线的设计往往要考虑材料力学, 弾、塑性力学,失稳理论, 薄壳理论等基础理论。由于在生产实践中影响卷封质量的因素较多, 较实用的设计方法是针对卷封结构的要求采取理论与实验相结合的方法。
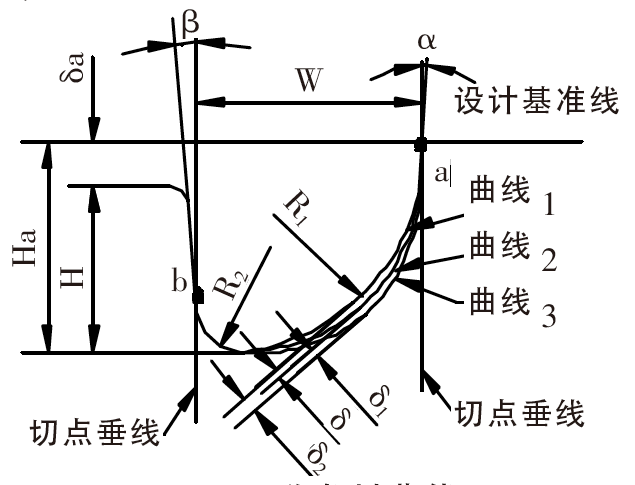
图9 一道卷封曲线
由图9 可知, 从导入切线与R1的切点a 至导出切线与R2的切点b, 卷封曲线的曲率半径曲∞ 变化至Rmin。这一变化过程理论上分析,应以连续变化为佳。连续变化的曲线有渐开线及对数曲线等。图10 为采用渐开线的一道卷封曲线, 从图中可以看出, 该曲线是由两条基圆直径分别为D1、D2的渐开线相衔接, 平滑、连续过渡的卷封曲线。ab 段曲线为第一渐开线,bc 段曲线为第二渐开线, 一道卷边分两阶段连续进行。
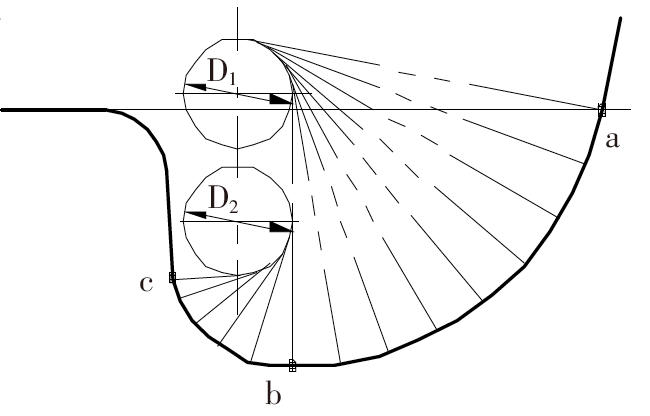
图10 采用渐开线的第一道卷封曲线
因这类曲线在工业生产中加工制作难度很大, 故常以几段圆弧来取代, 圆弧越多, 越接近理论曲线。为分析方便, 令渐开线ab 段的曲率半径近似为R1, bc 段的曲率半径近似为R2,如图9 中的曲线1。图中若曲线中R1增大, 则易引起薄板早期弹性失稳, 而R1减小可使薄板的早期变形较平缓。在卷封曲线卷封实验时,调整两阶段(R1、R2圆弧段)的曲率半径(如图11), 以得到较理想的一道卷封滚轮曲线。曲线确定后, 主要尺寸精度应控制在±0.005mm, 表面粗糙度0.2。
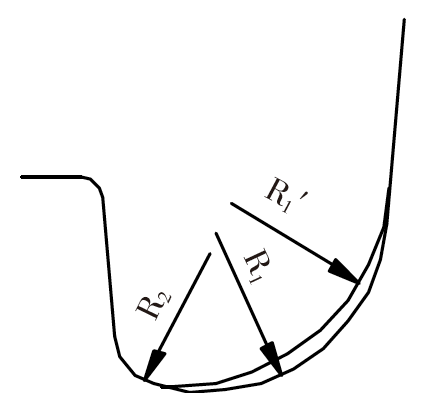
图11 曲线中R1的曲率变化
4 表面处理
采用氮化钛气相沉积法对卷封滚轮成品表面进行处理, 可进一步提高曲线沟槽的使用寿命。实验表明, 500~550℃的表面氮化钛处理,剥层后基体硬度仍能达到61~63HRC。
5 总结
对于Cr12MoV 钢制造的金属容器卷封滚轮,通过采用预处理(反复镦锻+球化退火+调质)、热处理(淬火+深冷处理+回火)、曲线精度、表面处理等改进措施, 可有效地提高卷封滚轮的使用寿命, 达到国外进口同类产品的水平。
|