热轧板制桶经验小议
西宁制桶厂 倪明祥
由于热轧薄板和冷轧薄板机械性能上的差异,导致在制桶工艺上也有所不同。
由于冷轧板塑性、韧性及表面粗糙度均好,容易保证制桶质量。热轧板与冷轧板相比,存有氧化层,韧性差,厚度误差大等缺陷,因此在用热轧板制桶时易出现焊缝裂纹,涨筋处撕裂及冲裁时卡模等现象。如果按冷轧板加工工艺生产热轧板钢桶,容易出现废次品桶。经修复、补焊后虽能满足使用要求,但外观质量差,并要花费大量返修工时和生产费用,加重了工人的劳动强度,增大了成本。
要提高热轧板钢桶的优质品率。我认为要注意以下几点:以200L桶为例。
1.正确掌握下料尺寸
下料对角线尺寸误差应控制在2mm以下,如超差,卷圆后搭缝口处有明显错位。错位短的一边在封口时会产生四层卷边,致钢桶发生渗漏。
2.加热后冲小孔
在冲压桶顶小孔时,由于热轧钢板较脆,极易出现冲口部位破裂,如采用氧气的加热方法,局部加热,边烤边冲,破裂现象基本消除。
3.磨边机的调正
由于热轧板存在氧化层及厚度误差大,所以必须注意磨边厚度。磨边机要做相应的调正。
①进料口导轨的调正。进料口导轨间隙的平行度调正到5mm以内。
下段导轨调正为喇叭形,但中部应控制在8mm以内。见图1。
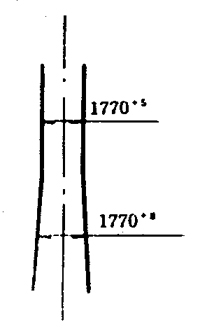
图1
②砂轮的选用和调正。砂轮易采用碳化硅材质,粒度36#。修磨砂轮时应把砂轮两边轮角修成圆角,使中间鼓起,用中间磨两边。磨边宽度一般选15~20mm。
4.桶身卷圆
由于热轧板厚薄不均,要随时根据卷圆误差调正压辊间隙,圆大间隙调小,圆小间隙调大。
5.点焊
热轧板点焊时焊点面积应控制在5.5~5.5mm2。小于5mm2时点焊处易烧穿。点焊以四点为宜。两头焊点距桶边20-30mm较好。
6.缝焊
焊接热轧板时应加快焊轮线速度。焊轮直径不小于令135mm。焊轮工作面宽为6.5~7mm。
焊轮应过盈装配,不能产生松动。如焊缝处有氧化层或杂质,一定要清除后方可焊接,否则会出现焊缝爆裂或击穿现象。
7.翻边
翻边宽度按3/8分,如桶顶边宽25mm,则桶身翻边宽25 x 3/8 =9.375mm。如图2。角度大于90度为宜。
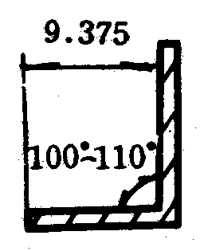
图2
8.涨筋
由于热轧板延伸率差,涨筋时易破裂。我厂曾出现一批热轧板中2-3%的桶在此工序涨裂。如筋高度采用负公差13-2,此现象有好转。
9.封口
封口工序是制桶的关键工序。据多年的经验,生产冷轧板桶和热轧板桶时,头道封口轮的形状有所差异。以200L五层卷边桶(1.2mm)为例。热轧板桶的头道封口轮形状如图3时,封口效果最好。如制冷轧板桶,则各尺寸要略小于图示数据。
其余工序,热轧板与冷轧板相同。
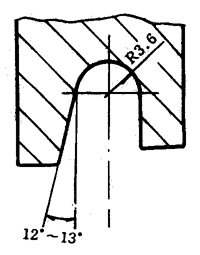
|