钢桶行业生产与技术发展得失谈(1)
李吉生
二十年来,由于国家正确的产业政策再加上行业主管部门的正确导向及生产厂家的努力,我国的钢桶生产装备与技术水平有了很大提高,产品质量得到了显著改善。我国钢桶行业的综合技术水平与发达国家的差距较二十年前有了明显的缩小。
笔者作为一名工厂技术主管,长期从事钢桶技术工作,目睹并亲身经历了钢桶业二十年来的变迁,耳熏目染之余,以解放军第3602工厂钢桶生产与技术的发展历程为例,分析我国钢桶行业生产技术发展的得失,将有助于我们更好地总结过去,以展望未来。
需要说明的是,文中所述仅为一人之见,若有错误还望行家里手予以批评指正。
一、我厂钢桶生产与技术的发展历程
我厂的前身是本世纪30年代美孚石油公司在上海开设的中国第一家钢桶制造厂。解放后,由国家收回交解放军总后勤部管理。其产品主要是200升钢桶。品种较为单一。在计划经济时期作为军品供军队使用。
七十年代初,我厂淘汰了三十年代的美国焊机,代之以3台当时较先进的按苏联图制造的半自动缝焊机,使我厂的桶身缝焊质量有了较大提高。
从前,我厂桶体油漆采用人工涂刷,自然干燥,工人劳动强度大,质量不稳定,工作条件恶劣,且不安全。曾有一次发生火灾,给工厂造成了较大损失。鉴于此,七十年代末工厂投入巨资,引进国内较为先进的静电喷涂生产流水线,漆膜的硬化在烘道内进行,通过悬挂输送链完成桶体的运输。机械化程度大大提高,漆膜厚度均匀,外形美观,附着力好,质量稳定;另外,工人的工作环境有了明显改善,大大降低了劳动强度。
当然,静电喷漆也有其不足之处,如:由于静电屏蔽的作用,部分死角喷漆不太理想,需要人工补漆;对油漆的电性能,漆粒的细化程度等要求较高。另外,操作工人素质的高低也直接影响到喷漆质量。利用烘箱烘干油漆,由于烘箱较高,热气上升,造成烘箱上下部温差较大(即便采用热风循环等措施缩小上下部温差,但由于烘箱过长、过大,效果也不明显),故易造成桶体上部烘糊而下部却烘不干的现象。静电喷涂的这些缺陷都应在生产过程中采取措施予以减轻。
静电喷涂线的建成,再加上工厂对制桶中端设备技术改造的完成,使我厂实现了生产200升钢桶从板材到成品不下线的流水作业。在八十年代初200升钢桶即具有了单班年产40万只的生产能力。由此,我厂200升钢桶的生产规模与自动化水平跃居同行业的前列。
过去,我们一直使用红糖骨胶做封缝材料。由于我厂的产品遍布全国,北到黑龙江,西至新疆,南到海南岛,南北气候温差最多可达到60℃以上,致红糖骨胶固有的缺点(如遇热软化,遇冷脆化及致密性欠佳等)引起的钢桶渗漏现象时有发生。为此,我厂相继使用了天津市钢桶密封材料厂的812密封胶,西安交通大学化工厂的WS型密封胶,厦门开元乳胶厂的白鹭牌密封胶替代红糖骨胶,这些密封胶综合性能较红糖骨胶有了明显提高,较好地满足了我厂产品对环境适应性的苛刻要求,提高了钢桶密封的可靠性。当然,这些胶也有不足之处,如有的耐候性较差,有的固化后失去了弹性,有的工艺性还有待提高等等。这些都是摆在封缝胶厂家面前尚需改进的课题。
进入八十年代后期,我国由计划经济体制开始向市场经济体制转化,市场竞争日趋激烈,原来我厂钢桶独占军队市场的地位受到迅速崛起的地方钢桶企业的有力挑战。另外,随着军队企业相继转向生产民品,原来我厂产品单一的生产格局已不能适应市场竞争的需要,还有被市场淘汰的可能。因此,大力开发新品种,保住军品市场,奋力挤入民品市场,以满足用户日益苛刻的要求,列入我厂的工作日程。
要开发新品种,首先需研制圆弧卷边钢桶。我厂钢桶卷边以前是单一的五层矩形平卷边。这在皇帝女儿不愁嫁的时期,还可高枕无忧,现在如果不改为圆弧卷边就有饿肚子的危险。刚开始搞圆弧卷边时,由于缺乏材料,与同行之间无信息交流,我们基本上是盲人骑瞎马,仅凭自己的直觉闭门造车,虽投入不少人力、物力与财力,但效果却很不理想。在这种情况下,我厂于1990年选派出工程技术人员参加了制桶分会在营口制桶厂举办的制桶技术学习班。在为期两个月学习班里,虚心向兄弟单位及任教老师请教,又反复到营口制桶厂的生产现场观摩学习,终于揣出了圆弧卷边技术的精髓,使圆弧卷边钢桶投入生产,为我厂产品的多品种开发消除一只拦路虎。另外,在系统学习制桶技术的同时,我厂工程技术人员与来自全国数十家钢桶厂的学员坦诚交流制桶心得与经验教训,促进了同行之间的信息与感情交流,为以后我厂与同行间的技术交往打下了良好的基础。制桶分会的这一功德及营口制桶厂的无私心胸受到了收获颇丰的学习班成员的一致称赞。
我厂利用领悟到的圆弧卷边技术,依靠自制的设备,相继完成了材料厚度分别为1mm、1.2mm、1.25mm、1.5mm及容积分别为100L、150L、200L等规格钢桶,采用圆弧卷边的小批量研制。圆弧卷边性能满足了钢桶国家标准的跌落试验要求。
总结圆弧卷边的研制经验,我们认识到,尽管圆弧卷边卷层结构达到了要求,钢桶的跌落性能有了明显提高,但桶体三角区处仍是跌落渗漏的薄弱区,究其原因,还是焊缝搭边(达10 – 16mm)在作怪。两种焊缝形状差异见下图:
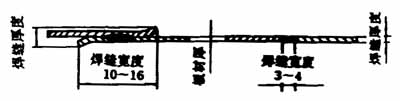
图1 半自动焊机和自协焊机的焊缝示意图
因此,要彻底解决钢桶三角区渗漏问题,还需采用搭边值小,焊缝薄的全自动焊机进行桶身缝焊。于是,工厂投资50余万元购进南京矿山机械厂消化吸收的FN – 250型全自动缝焊机。其设计功率为250kVA,焊接搭边仅为3mm,焊缝厚度接近母材,采用PC编程控制器控制焊机的程序动作,焊接电流在桶身缝焊起始、中途、结尾处能自动做出上下坡调整。设计生产能力可达到600只/小时。进厂后,经反复调试,焊成合格的桶身。由于其焊缝厚度接近母材,因此用这样的桶身进行圆弧卷边后,钢桶基本上不会发生三角区渗漏的问题。
但是,由于焊机仿制过程中不可避免的一些缺陷,使得焊机的不少设计性能打了或多或少的折扣。例如:为避免产生半自动焊中常见的焊缝前段易焊裂,尾段易脱焊的缺陷,该焊机焊接电流曲线设计成马鞍形。它半自动焊机的焊接电流曲线的区别见下图。
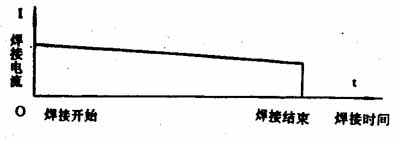
图2 半自动焊机焊接电浪曲线示意图
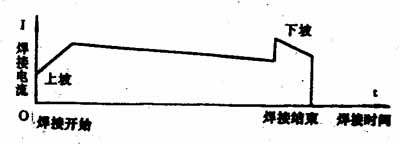
图3 自动焊机焊接电流曲线示意图
其设计思想为:在开始焊接时,为避免电流过大产生焊裂,起始焊接电流为小于正常工作时的焊接电流;在焊接至焊缝尾端时,由于阻抗的变化,需用高于正常工作时的焊接流方能保证焊缝不脱焊。这一过程,由复杂的焊机可控硅(SCR)触发角控制部分来完成。尽管设计者煞费苦心,但实际效果并不理想,焊缝前端开裂,尾端脱焊的现象仍时有发生。
再如,焊机虽表明使用国产热轧钢板也能达到较好的焊接效果,实际上,对于国产热轧板的种种缺陷及磨边剪板中常见的质量波动即便自动焊机也不能妙手回春,因而焊接结果总是不能令人满意。
由于圆弧卷边桶对桶身扳边质量要求较高,原来一直采用的旋压式的扳边机已不能满足要求,于是,我厂又投资70万元购入广东新会会城通用机械厂生产的焊缝压边切边机、扳边涨筋机、三合一装配机。
焊缝压边切边机设计工作机理为:焊好的桶身送到位后,在PC控制下,液压油缸对桶身两端超过母材厚度的缝焊经两端的辊压轮同时进行强力压薄,然后另外的油缸驱动剪下焊缝铁舌。此机的目的在于消除焊缝对卷边处的影响,减少卷边三角区的渗漏率。
扳边涨筋机工作机理为:在PC控制下,主油缸首先分次涨出两条大筋,然后主油缸驱动扳边盘,对桶身进行纵向挤压,从而完成桶身的扳边。
三合一装配机的工作机理为:将桶顶(底)卧放桶身两端;传输链将其送到位后,装配机两大盘相向运动夹起桶顶(底)和桶身由慢至快旋转起来;在凸轮机构的驱动下预卷首先进给,实现桶顶(底)的预卷;预卷完成后,由光电开关控制喷胶系统动作,对刚预卷完的桶顶(底)均匀喷上封缝胶;然后,第二、三卷边轮依次动作,完成钢桶的三重圆弧卷边。
对这三台中段设备,总结数年的使用经验,我们有以下认识:
焊接压边修边机对半自动焊机完成的焊缝(搭边值达10 – 16mm)的压边效果不大。据测算,要实现焊缝处的明显变薄,至少需百吨以上的冲击力,而该机的滚压力充其量不过十来吨。因此,用这样的力量对搭边10mm以上的焊缝进行压薄,无疑是隔靴搔痒。因此,对宽搭边的焊缝不能达到减少三角区渗漏的目的,而全自动缝焊机的焊缝即便不进行压边,其厚度也接近母材厚度,另外其焊舌也很小,用手砂轮即可轻易消除。在此情况下再使用压边修边机无异于用高射炮打蚊子,真有点大材小用,因此该机对提高钢桶防渗漏能力的作用不大。
扳边涨筋机动作简单明了。只是由于结构所限油缸行程过长,限制了工作速度的提高。另外,对不同厚度的桶身,为保证其圆弧卷边质量,就需要不同尺寸形状的扳边,这就需要配备不同尺寸形状,造价高昂的扳边盘,较之旋压扳边,这种扳边成本高。扳边盘磨损后修磨也很麻烦。生产多品种时工人增加了反复卸装调试工装的辅助工作量,影响了车间的劳动效率。当然,这一缺陷不能归咎于扳边机生产厂家。
三合一装配机把预卷、中卷直至成型三重卷边及喷胶工序集中在一台装配机上完成。从设计角度来看,这种设计较之那种把预卷与终卷分开的模式能提高劳动生产率,但从制桶行业密封胶的密封机理上分析,就能有欲速则不达的感受。总结我们自己生产经验并收集同行经验,我们知道:三合一模式的装配机,再配自动喷胶时,由于整个过程持续时间极短,喷出的封缝胶液不能马上固化,在随后的中卷、终卷过程中极易被挤出卷层,这样就不能在圆卷边的卷层中部形成有较好弹性并具有一定强度的橡胶密封条,从而影响到卷层的密封性能。经我们了解,凡圆弧卷边桶跌落性能较好的生产厂家,大都把预卷喷胶工序作为一个单独的工序。这,经预卷桶顶(底)转入下工序前封缝胶有一段固化的时间形成具有一定强度与弹性的密封带。
由于钢桶设备生产厂家与钢桶厂家之间缺乏技术交流而产生的弊端又一次反映在注定有缺陷的制桶设备上。(未完待续)
相关链接:钢桶行业行产与技术发展得失谈(2)
|