卧式双面挤压折边机
景志平
国产XJY112型双面挤压折边机已研制成功投入使用。它的问世,体现了中国制桶界对于钢桶卷边质量,具体为桶身折边质量的高水准追求。
大约十年之前,我国制桶行业还几乎全部采用滚压工艺对闭口桶身进行折边。至于开口桶身卷管则更无一例外地采用滚压工艺且沿用至今。滚压折边卷管工艺的致命缺陷在于其成形精度过低。
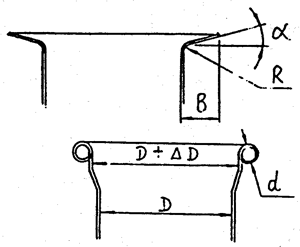
图1 折边和卷管的工艺参数
如图1所示,滚压折边所形成的折边宽度B、折边园弧R和折边倾角.a的精度往往不尽人意。如边宽B的重复精度(包括在一个桶身圆周上的各处边宽误差和不同桶身间的边宽不一致误差)常达±0. 5~1mm以上。对于开口桶身卷管,传统的滚压工艺所产生的卷管直径d重复精度很差。更严重的是,由于滚压卷管一般是在卷边机上完成的,而卷边机封口盘和卷管滚轮之间的空间位置干涉,造成"喇叭口"即卷管后的桶口桶径大于桶内径(图1 ,中的D+△D,为表示清楚图中有所夸张),且桶径增大△D为一不定值。这将影响开口桶的顶盖密封质量。滚压卷管用于镀锌桶身时,滚轮往往破坏卷管镀锌层,导致桶口锈蚀。
作为包装容器的钢桶,密封性是第一位的技术要求。它可分解为两个要素,即钢桶顶底的尺寸精度和桶身折边或卷管的尺寸精度。目前在制桶行业,钢桶顶底已普遍采用冷冲模冲压加工,尺寸精度可达±0. 1mm。但对于桶身而言,传统滚压工艺所产生的折边和卷管精度±0.5~1mm显然不能与顶底进行匹配,成为制桶行业的一个技术缺陷。
1987年,我国第一台"三合一"桶身联合形机研制成功。该机采用的挤压折边技术使桶身折边和卷管的重复精度达到±0.1mm,在制桶行业得到普遍应用。由于"三合一"机在一次上料中完成折边、波纹和环筋三道工序,机床结构复杂,成本较高,在目前钢桶市场疲软形势下,许多企业希望能发挥该机的挤压折边技术优势,研制成本较低的多功能挤压折边机。
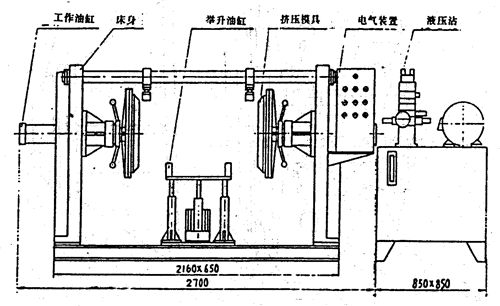
图2 双面挤压折边机
图2为1998年5月问世的国产XJY112型挤压折边机的总体结构。为实现加工过程的自动化,便于用户用于生产流水,机床仍采用了卧式双面动力的总体布局。焊接式底座、两端铸造立柱座体和两根顶梁构成框架式床身。机床两端各设置一部用以产生折边挤压力的挤压油缸。位于底座中央的举升机械手和安装在顶梁上的弧形定位档板用于将各种规格的桶身定位在机床工作中心高度,并在工作完毕模具撤退时夹持折边部位以防止桶身左右移位。模具安装座上的轴向调整装置和举升机械手下方的径向调整装置可使机床在更换模具后的加工范围满足GB325- 91中所列的20~200升全部规格的闭、开口桶身的折边与卷管加工,即料厚、径和桶高分别可在(0.4~1. 5) x (φ280 -600) x (300~1000)mm范围内进行调整。其中料厚调整主要依靠液压系统工作压力的无级调节功能。桶径调节则通过变更举升机械在油缸座T形槽中的高度,以及顶梁上的弧形定位挡板的高度位置来实现。由于桶高度化范围较大(达700mm),机床设置了两个环节来实现其调整。图3左侧剖示出机床模具的轴向大幅无级调整装置。空心话塞杆1内装有一足够长度的调节丝杠2,松开锁紧螺母3,转动滑座4时,通过另一锁紧母5与滑座4固联的丝杠2即随滑座同时转动,从而在活塞杆1的螺孔中作轴向位移,以获得桶高在300~1000mm范围内变化时所需的模具轴向位置u滑座4在轴向调整后若伸出螺套6过多,则须将螺套6通过手柄7旋出座套8,以保证模具支承导向剐度。
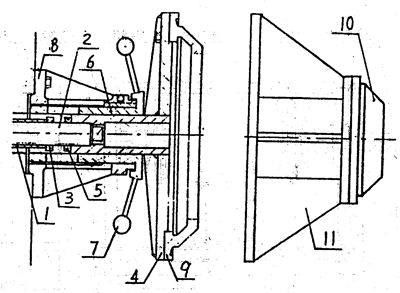
图3 桶高的大幅度调整环节
图3右侧剖示出机床模具轴向大幅分级调整装置。这种装置特别适合从较大规格(如高度以为890mm的200升钢桶向较小规格(如高度为350mm的20升钢桶的跳跃式变更。这时,可直接将200升模具9卸下,换以与20升模具10固联的过渡模座11,而用丝2作微调环节即可。
上述针对料厚、桶径和桶高的大幅调节功能,显著提高了机床的性能价格比值。它使本机可以适应GB325—91规定的20~200升任规格的闭、开口桶桶身的折边和卷管成形加也能适应即将执行的0571.5桶径系列的国际标准钢桶桶身的生产。这样,本机恰似一台通用的冲床,更换模具即可迅速变更加工规格,生产市场需要的钢桶品种,且模具投入费用很少。
由于挤压成形有机理等同于冷冲压,本机所获桶身折边和卷管尺寸精度±0. 1mm恰与顶底冷冲压尺寸精度实现匹配,这就为三重卷边提供了十分理想的质量基础。挤压卷管不仅有着光滑圆整的外观,其尺寸和形状十分规则,桶口不出现滚压卷管难免的"喇叭口",也不破坏卷管上的镀锌层。图4所示为机床的液压传动系统。高压双联泵2产生的压力油分别经两个ISO4401国际标准系列叠加阀组,控制工作油缸和辅助油缸的运行。泵2中P路泵压力由外控顺序阀6限定,高压P1路泵压则由电磁溢流阀13调整。增 1减系统工作压力P或P1时,可借助压力表开关15和压力表16进行观察调整。当工作负荷未达到外控顺序阀6压力时,工作油缸由双,泵同时供油高速运行。系统达到或超过阀6压力时,P1外控油路压使阀6导通令P路自动卸荷,电机功率集中用于驱动高压泵工作,而实现准恒功率控制。无论机床处于调整状态,或完成一自动工作循环回复原位后,电兹溢流阀13均使液压系统及时卸荷,以降低 '真系统的发热。图4中的阀5可为机床自动循环提供必要的位置讯号。阀9则为挤压高速往复运动提供背压。举升定位压力可通过图中的阀12、阀15和压力表16进行调整。
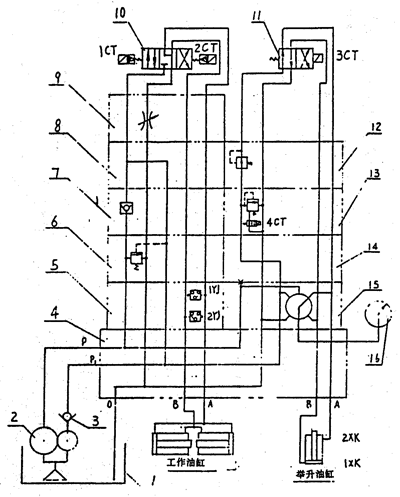
图4 机床液压系统图
机床主要技术参数为:最大加工尺寸(直径X桶高)600x1000mm,操纵方式自动胖自动,机床生产率10件份,机床工作中心高度920mm,电机功率7.5kw,液压系统额定压力14MPa,主机总体尺寸2700x650x1400mm,液压站尺寸850 X 850 x1400mm。
机床的工作状态有两种,即连续工作时的自动循环状态和非连续工作时的手动状态。二者可用电气箱上的状态选择按钮进行选择。自动工作状态时,操作者只须按下自动循环起,动按钮,机床便完成下列自动循环:桶身举升定位——左右模具快速进给到达折边位置—系统自动转入低速进行挤压折边——完成折边后系统保压使材料充分变形——电脑判别成形尺寸合格后模具撤出桶身一举升装置降下完成一个自动循环。手动状态时,可按需要点动相应按钮,分别实现举升、降下、挤压进、挤压退等机床独立运动,用以进行调整或断续加工。
作者单位:西安市机械研究所
|