叠加阀式液压系统在制桶机械中的应用
贾凯
液压系统是机床制造中普遍采用的驱动与控制方式,然而控制的形式却是多种多样,并且在配装形式上也形式不一,常采用的形式有:管式连接、板式连接、集成块连接以及新发展起来的叠加阀系统。叠加阀是在集成板块的基础上发展起来的新型元件,在组成系统时,它不需要另外的连接件,是以自身的阀体为主直接叠合而成,每个叠加阀既能起到控制元件的作用,又起到通道体的作用,而且每种规格通径的叠加阀主油路的位置和数量都与相对应通径的换向阀相同,这样相同通径系列的叠加阀与对应通径的换向阀叠加起来便可组成一个系统。叠加阀系统与其它形式的系统相比有着显著的优点,现用下表进行对比。
几种液压配装形式特点比较
配管式阀组 |
板式集成块阀组 |
叠加阀阀组 |
1、结构庞大,管路繁多,管路密布。 |
1、元件可直接把在通道体上不需要管接头及钢管。压力损失小并可消除连接产生的共振及压力波动,故效率较高。 |
1、结构紧凑,体积小,重量轻,占地面积小。 |
2、不便于管理维修,也不便于装拆更换。 |
2、便于安装拆卸、维修管理,容易排除漏油。 |
2、安装简便,装配周期短,系统有变化需增减元件时,重新组装方便迅速。配置灵活,外观整齐,维修保养容易。 |
3、漏点环节增多,管接头连接处容易漏油和进入空气,产生振动。 |
3、因回路典型化,便于根据需要选取适当回路组成系统。 |
3、元件之间无管连接,消除了因油管、管接头等引起的漏油、振动和噪声。 |
4、管路长,沿程损失大,效率低。 |
4、结构紧凑,外形整齐,占地面积小。 |
4、可实现集中供油,节电效果显著。 |
5、标准化程度较差。 |
5、通道体可实现系列化、通用化、标准化、便于成批生产。 |
5、已全面实现标准化、系列化、通用化并已与国际标准ISO4401接轨。 |
由上表可见:叠加式集成阀组是克服了管式阀组的诸多缺点,并在板块式集成阀组的基础上发展起来的新型配装方式,在叠加阀组中不但可以将同一通径系列的叠加阀叠加起来称为纵向叠加)组成多种不同的系统(如工进、保压、同步、差动、多缸锁紧、顺序等控制系统)以满足矿山、冶金、工程机械等一般的工作循环要求,而且还能将各阀组通过多联底板块叠加起来(称为横向叠加)以实现多个执行元件(多缸动作或多缸与多个液压马达并用)的集中控制,也可将叠加阀组与板式集成板组合使用,以适应复杂系统或有特殊功能要求的系统以及大型系统的需要。
以下介绍几种叠加阀在制桶机械上应用的实例:
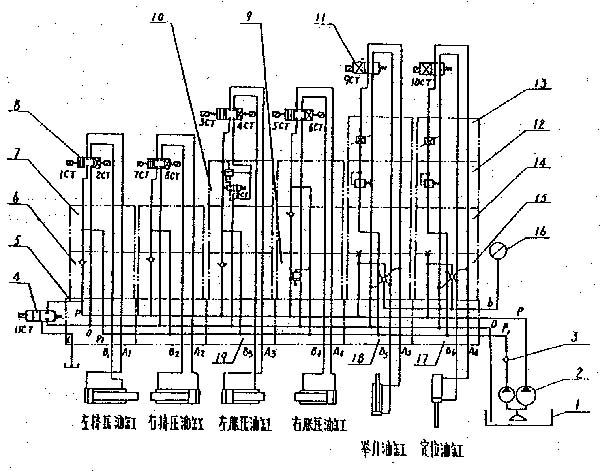
图1 XJY44型"三合一"桶身联合成形机液压系统图
如图1所示为我所研制的Ⅺ44型桶身联合成型机的液压原理图。该系统属于多动力部件集中控制的液压系统典型实例,系统中采用双联定量叶片泵(2)作为动力源,P1油路和P油路分别由电磁溢流阀(10)和外控顺序阀(9)设定,形成双级压力回路。在挤压缸回路和胀压缸回路中设置有单向阀(6)和专用板块(7),由于这两层阀块的作用,当工作负荷未达到外控顺序阀(9)的调定压力时,挤压缸和胀压缸由双泵(P1和P)同时供油快速运行。当系统达到或超过外控顺序阀调定压力时,P1油路的压力油通过外控口打开顺序阀使大流量泵自动卸荷,这时P1油路和P油路自动由单向阀(6)隔开,油缸在电磁溢流阀(10)设定的压力范围内且随外界阻力变化而变化的工作负荷下运行。这时电机功率几乎全部用于驱动小流量泵(P1)工作。使得本定量泵系统也发挥出了变量泵系统恒功率控制的优势。从液压系统图1中不难看出:同名油缸液压回路(如左挤压缸回路和右挤压缸回路,左胀压缸回路和右胀压缸回路等)从结构上基本对称,在这种情况下,当外界工作阻力相差不大,管道沿程阻力差别也不大时,由于各缸结构参数都相|同,自然形成了同名油缸的基本同步动作(在同步精度要求不高时)。
又如举升油缸和定位油缸回路所示,因为这两路油缸和其余油缸相比缸径要小得多,同时工作负荷也要小得多,为了控制其平稳工作,采取了以下措施:首先用专用板块将P油路隔断,让高压小流量泵P1给其供油,其次,为了避免油缸在工作过程中的冲击,在这两个回路中都设置了减压阀和节流阀,在接受主系统为其提供的压力油的同时,各自还可调出自身所需的分路压力,可靠实现了其平稳工作。
本系统的缸荷环节有三处:除了外控顺序阀(9)在工作过程中可以实现大泵P的动态自动卸荷外,当机床处于原位状态时,由行程开关提供电讯号,让电磁阀(11CT)、(12CT)同时通电动作,使得电磁溢流阀(10)和换向阀(4)将P1油路和P油路都与O油路导通。让全系统卸荷,这样整机便处于待命准备状态,减少了功率损失,降低了系统发热。
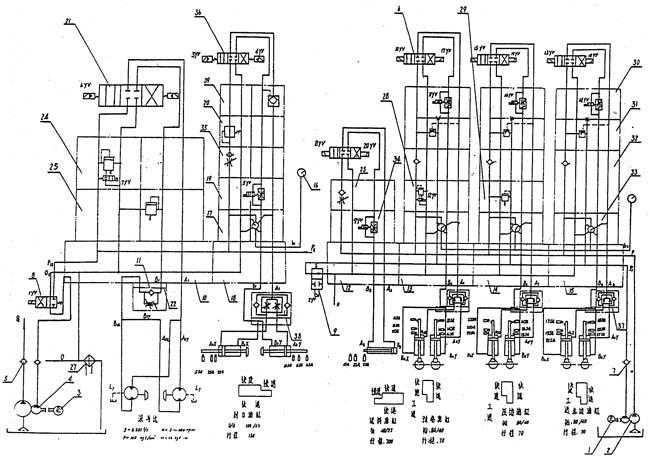
图2 XJY49型卷边液压系统图
图2为我所研制的全液压式驱动的XJY49型卷边机的液压原理图。它是使用叠加阀来控制较为复杂机床动作的又一典型范例。
由于卷边机的工作特点决定了其液压系统较为复杂,其主要原因有:第一,由驱动封口盘主旋转动作决定的主传动系统需要有较大扭矩的动力输出,与之相应便需要给液马达提供较大的压力和流量(由液压马达的排量决定),所以功率消耗较大。
封口盘驱动油缸由于缸径较大,也需要较-大流量,但夹紧力需要较小。然而送料辅助油缸以及卷边轮进给油缸所需的流量和压力均较小,这样形成了多路动作的各执行元件之间流量压力需求相差较大这样一种矛盾。第二,由于各部件的运动在时间上交错作的情况,因而在各回路之间将会产生压力波动,使得各回路之间容易产生干扰,具体为:主传动回路(包括封口盘夹紧回路)与进给缸回路(包括送料缸、预卷缸、卷边缸和压边缸)之间的干扰,以及各进给缸回路之间的相互干扰。
根据以上分析不难看出,必须将相近流量大小的执行件安排为一组进行单独控制,这样可以充分利用叠加阀系统既可分散又可集中控制的特点,从总体布局上将主传动系统与进给系统(包括辅助系统)分隔开来进行控制。这样既解决了两组系统流量压力相差比较大的矛盾,又从根本上消除了主传动系统和进给系统之间的压力干扰。
如图2所示,油泵4是驱动大系统的双联定量叶片泵。为了满足液压马达排量要求,在液压马达回路中采用目前国产叠加阀中最大规格(通径为20mm)叠加阀,并将封口油缸回路(通径为16mm)与液压马达回路进行横向叠加,以便对这种具有相近流量需求执行件进行流量控制。系统压力用同一只电磁溢流阀(24)设定(两联泵压力相等)并且压力高低按卷边时流压马达回路压力需求设置。液压马达回路中溢流阀(23)用于防止换向阀当阀芯切换时在回路中产生的压力冲击。板式单向调速阀(22)与叠加阀组结合使用,安装在液压马达的回油路上,其作用有两个:第一,建立一定的背压;使两并联马达同步稳定旋转,第二,通过调速以控制液马达的转速的无级变化。液压马达的转速是通过两个环节来调整的,—方面通过电磁换向阀(8)来控制两联泵的合并或小泵的直接卸荷,实现液马达的两级速度变化;另一方面通过板式单向调速阀(22)来实现液压马达的无级调速,以满足加工不同桶径时所需的不同转速。封口油缸回路流量、压力都要求较低。减压阀(20)用来控制该回路的输出压力;单向节流阀(35)用来控制封口缸的快进速度;电动调速阀(19)用来控制封口缸的工进速度;液控单向阀(39)使封口缸的夹紧在卷边过程中不能有松动现象;板式单向同步阀38)与叠加阀组相结合,保证了封口缸的同步进给。
大系统的卸荷由电磁溢流阀(24)来控制。
如图2右所示,为卷边机进给缸和送料缸油路控制系统,该系统控制的各缸流量和压力相近,便于用叠加阀进行横向叠加集中控制,在这里选用了10通径叠加阀组。系统仍用双联定量泵提供动力。低压大流量P泵由电磁溢流阀(28)来控制压力,给各进给缸提供快进压力油。高压油路P1由顺序阀(29)来控制压力给各进给缸提供工进压力油。当外界阻力低于电磁溢流阀(28)调定压力时,P和P1同时给油缸供油,使其快进;当外界阻力高于电磁溢流阀(28)调定压力而低于顺序(29)调定压力时,P发生溢流或给其余旁路提供快进压力油,而原缸回路继续由P1提供工进压力 <油;当原回路油缸工作到行程终点,而其它旁路油缸仍在行进中时,P1油路将给其余旁路回路提供压力油。当全部油缸都工作到终位或每一组叠加阀中最上面一层的板式换向阀处于中位时,顺序阀由自控口打开,使P1油并入P油路,经电磁溢流阀(28)溢流。该系统的卸荷环节为两处,一处是电磁溢流阀P iZ油路的电磁铁断电卸荷环节,一处是板式换向阀(9)控制的P1油路电磁铁通电卸荷环节。
如图所示送料油缸回路,用进口油路设置的单向节流阀(25)和回油路上的电动调速阀(34)分别控制送料油缸的快进速度和缓冲速度。其余三组进给缸回路(预卷油缸回路,压边油缸回路和卷边油缸回路)从控制形式上讲L乎完全对称,在每一组进给回路中安装的板1式同步阀(37)是为了实现同名并联油缸的同步动作;单向阀(32)可将低压P油路和高压P l油路隔开;电动单向调速阀(30)是为了控.制进给缸的工进速度,这种出口调速同时也保 压证了进给速度在负载变化时的稳定性。外控顺序节流阀(31)是实现三组油缸高低速交叉进给互不干扰的关键元件,它的作用是:当三组进给缸中的一组缸正进入工过程时,由于外顺序节流阀(31)节流口的作用,可以避免其它支路这时因为油缸的快进和快退而产生压力波动时对工进回路的影响。
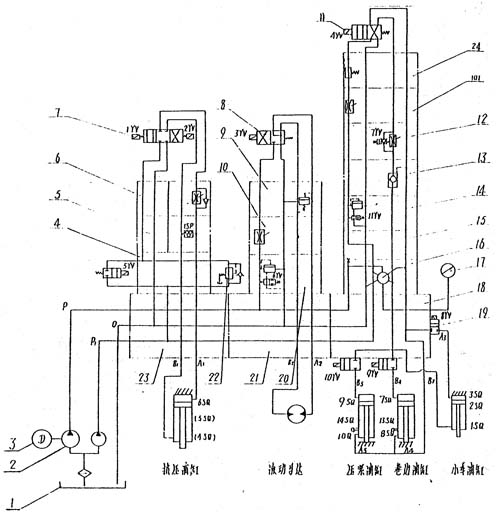
图3 XJY61型压缩封装机液压系统图
如图3所示,是我所研制的ⅪY61型压缩封装机液压系统原理图。本系统执行元件为三个直线运动油缸和一只旋转运动液压马达。压缩封装机的基本工作过程为:送料缸将工件(乘满物料的钢桶)送到工作位置——挤缸对桶内物料进行挤压—退出填料(反复多次)——加盖后再进入——挤压缸压盖一液马达旋转——卷边缸进给卷边——卷边缸出——压力缸进给压边,压边缸退出——液马达停转——挤压缸抬起——送料缸退出。
该系统总体设计特点:由于项目任务书中系统有严格的重量限制,首先,系统设计必须结构紧凑。第二,挤压缸油路必须具备双级压力,以便实现同一油缸两级压力驱动的动作。第三,液马达的旋转运动与进给缸直线运交错动作,为了排除压力干扰,将液压马达回路与进给缸回路隔开供油。从上面几点要着眼,在考虑方案时对以下几点作了重点考虑,系统油泵选取双联叶片泵,让大泵给液马达供油,小泵给其余各缸供油两路压力分别由电磁溢流阀(20)和电磁溢流阀(14)来控制,并将两路完全隔开,两路流量也因需求不同有较大差别。如图所示在挤压缸回路中,采用板式减压阀(22)和板式换向阀与叠加阀组结合使用,使得在压料过程中挤压缸用溢流阀(14)调定的P1压力动作,达到压头在压缩过程中所需的力量;在压盖过程中,压力要求较低,通过板块上的换向阀切换,P1经过减压阀减压,形成第二级压力(对于整个系统来讲实际上是第三种压力)以满足在封口过程中压头夹紧桶盖旋转所需的力量。单向节流阀(6)可以控制压头的前进速度,中位阀芯机能为O的三位四通电磁换向阀可以让压头在点动时停留在任何需要的位置,并能防止因自重而下滑。压力继电器(5)可让挤压缸何时返回提供讯号,因为在装料量变化的情况下,挤压缸每次前进距离是不一样的,无法靠行程定位发讯。
在液压马达回路中,节流阀(10)用来控制液压马达的转速。溢流阀(9)并联在P油路和O油路之间,调节其开启的压力,可以避免液压马达在换向阀(8)切换使其停转时由于惯性产生的冲击。
第三组:小车油缸,卷边油缸和压紧油缸回路,实际是三组相同类型回路的合并,在这里因为考虑到三组油缸在动作顺序上是接续动作,因此在充分发掘叠加阀潜力的基础上再与三只电磁换向阀(9)进行有机结合,使得该回路更加紧凑,这是叠加阀巧妙应用在简化结构方面的一种典型范例。在第三组回路中节流阀101控制进给缸的快进速度,减压阀(24)可以控制该回路各缸的工进速度。液控单向阀(13)主要是为了使送料车油缸在卷边过程中不要因为油路泄油而发生移位。叠加阀式压力表开关(16)可以方便地读出系统的P油路压力和P1油路压力值以及该组回路中的A油路、B油路和O油路各咱压力值。
从以上几种液压系统的应用实例可看出,叠加阀在制桶机械液压系统中确实显示出其具有较大的优势。实际上,在产品的研制、开和改进工作过程中,对一种系统要经过几次甚至十几次的修改,这时可能要进行多次元件增减和重组,只要零件齐备,应用叠加阀应付这种棘手问题便显得易如反掌,在此充分显示出叠加阀配置灵活的特点,我们搞产品开发的工程技术人员对这一点体会很深。最后,我们相信,随着液压技术的不断发展以及新元件、新技术的不断出现,一定会给我国的制桶技术来新的进步。
作者单位:西安市机械研究所
|