桶身“三合一”成型机床的应用
西安市机械研究所 景志平
我所于研制的XJY44系列桶身折边、波纹、环筋“三合一”成型机床,经多年应用实践,现已发展为生产节拍为每分钟2、3、4、6、3、10件的系列产品。曾获国家科委等五部委联合颁发的“国家级新产品”证书。目前,该机已在国内16个省区的24家制桶企业使用。
一、 “三合一”机床简介
图1示出了“三合一”机床的总体结构。机床由四柱式导轨构成的床身多用于自动上下料的举升定位装置;产生折边和筋纹成型动力的工作油缸;一次完成折边、波纹和环筋三道工序的成型工具(模具)及电气,液压系统等部分构成。
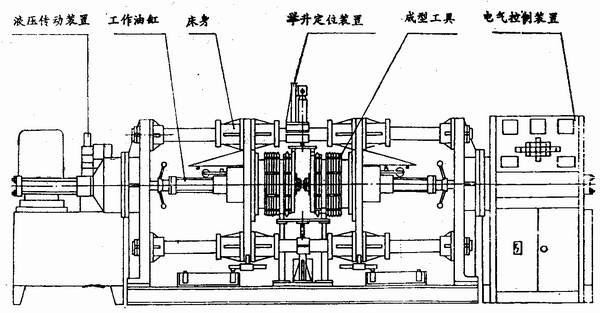
图1 桶身联合成形机床
图2为某两种规格钢桶桶身的加工示意图,每个规格只示出一半。桶坯举升定位后,由机床两端的折边油缸将安装在左右工具座板上的成型工具缓慢地推进桶。口。进入桶口后高速向桶身中部推进至折边位置,再转入低速工作进给,从而实现挤压折边。然后,成型工具内部的八棱锥由工具主轴驱动进给,通过工具表面的波纹模和环筋模实现桶身多条波纹和两道环筋的成型加工。加工完毕,八棱锥先退回原位,令环筋波纹模缩回,随后整部成型工具由工具座板拖出桶身, 自动上下料机构动作使桶身滚下,并作好准备接受下一桶坯的自动上料。
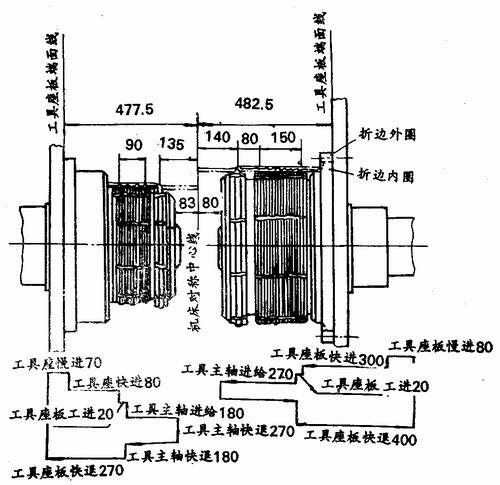
图2 桶身联合成形机床加工示意图
二、应用概况
表1列出了“三合一”机在国内钢桶行业的应用情况。
表1 “三合一”机应用一览表(略)
三、应用特点
1.多品种加工。表1显示,有50%的企业用“三合一”机生产两种以上规格的桶身。机床适于生产直径φ285~φ570mm、长度330~1OOOmm, 料厚O.4-1.5mm的各种规格的桶身。一些厂家开始只订制了一两种规格的模具。后根据市场需求又逐步增加到三、四种。有的厂家还订做了快换式折边圈。这种折边圈由内、外圈组合而成,如图2加工示意图的右端所示。变更桶身折边宽度时,不必卸下整套成型工具,只须将折边外圈纵贯模具外周卸下,并装入另一外圈,即可生产另一折边宽度,或两端折边宽度不同(如开口桶)的桶身。实践表明, “三合一”机恰似一台通用压力机,只需在半小时内更换一付模具,即可加工20~200L间任一规格的钢桶桶身,或在更短时间内更换折边外圈生产原有直径而不同折边宽度的桶身。一特点使企业有能力接受客户的多品种中小批量钢桶订货,迅速调整设备以适应市场需求。
诚然,通常不只在桶身成型机上进行更换钢桶生产,品种的设备调整工作。钢桶底盖和卷边等中段设备也须进行相应调整。因而本所研制的XJY49型可调式通用卷边机、XJY81系列导柱式底盖复合冲模及XJY48A型预卷喷胶机等配套设备也都具有多品种加工的特点。
2.上下料自动化。用户在“三合一”机上的上下料操作目前有三种方式:
一种是靠人工或滚道滚入,举升V形臂,加工循环完成后,在定位弧形挡块抬起瞬间,操作者将桶身推入下料滚道。这种方式并未发挥本机自动上下料装置的功能,十分原始费力。
第二种是用户自制动力输送环节,将本机与前后设备相连接。这种方式虽也实现了上下料的自动化,但同样未能发挥本机自动上下料装置的潜力,造成输送装置和动力的浪费。
实际上, “三合一”机床的上下料作业,无须任何附加装置和动力,即可实现自动化。下面便将这种上下料方式即第三种方式,作以介绍。
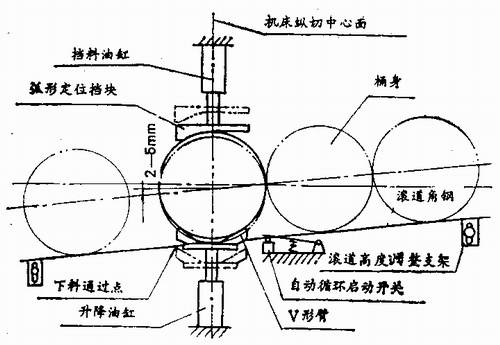
图3 自动上下料滚道安装示意
如图3所示,“三合一”机的升降油缸原位处于缩回状态,这时V形臂处于图中滚道下方的双点划线位置。挡料油缸原位则处于伸出状态,这时弧形挡块处于图中实线所示位置。从缝焊工序滚来的桶身毛坯沿倾斜约10°的角钢滚道进入机床纵切中心面。此面低于工作中心2-5mm(图中上下定位元件之间的双点划线桶身位置)。此时桶身下方支承在滚道角钢上,上方则被处于原位的弧形定位挡块阻挡定位。桶身滚入瞬间压下图示自动循环启动开关(或操作者按下自动循环启动按扭),升降油缸驱动V形臂将桶身举升2 --5mm至工作中心高度(图示实线桶身位置), 自动上料即告完成。之后,机床自动按图2所示加工过程进行成型加工。成型工具撤出桶身后,升降油缸驱动V形臂降至滚道角钢滚动面以下的原位(图示双点划线位置),挡料油缸则提升弧形挡块至图示双点划线位置,桶身即沿滚道斜面滚下。在下一桶坯到达工作位置之前的瞬间,挡料油缸已在放过上一桶身后迅速压下,从而实现下一桶坯的上料定位。实践证明,按上述方式可十分简便而可靠地完成桶身的自动上下料作业,不需其它输送动力装置。
在应用上述方式时应注意三个环节。一是滚道角钢的滚动平面高度,应使桶坯的输送中心在工作位置低于定位后的工作中心2-5 mm,但不低于图示“下料通过点”。图示滚道高度调整支架除调整这一高度和斜度外,还用于更换钢桶规格时的高度调整。图示滚道角钢在实际应用中大多分为上料和下料两段。二是挡料油缸抬起后放过成品桶身又及时压下阻挡下一桶坯。确定定位时间,除通过调节定位油缸的速度外,还可通过调整电气柜中的一只时间继电器得到准确的定时。三是图示自动循环启动开关为一行程开关。在机床电气分线盒内已标有这只开关的接线号,并在升降油缸开关出线处备有预留接线。由于这只行程开关与机床操纵台上的自动循环启动按扭并联即作用相同,即使是每分钟8件生产率的用户,其操作也不显得繁琐,因而大多数用户不在滚道上安装那只启动行程开关而习惯于使用按扭。当然,在大批量连续生产线上安装这只行程开关还是值得的。
3.折边精度。图4示出了“三合一”机床采用的挤压折边工艺的成型机理。在机床左右两侧成型工具折边圈(图中示出一半并旋转90°)轴向挤压力作用下,桶口沿模具锥度逐渐扩口、延伸、弯曲形成折边。由于这一过程相当于金属冷冲压中的弯曲及成形, 因而挤压折边精度较传统的滚压工艺有较大幅度的提高。如折边宽度可达IT 12级(±O.1)左右,折边倾角精度可达±0.5°等。这对于实现三重卷边已形成数倍的精度储备。
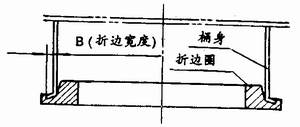
图4 挤压折边机理
实践证明,保证折边精度的重要条件是桶坯的尺寸精度。图5将常见的两种桶坯缺陷集中于一只桶身的两端。左端为由于下料精度或点焊定位精度较差引起的接缝错位;右端则为更常见的缝焊铁舌。这两种桶坯进入“三合一”机折边后,将对折边精度产生影响。其中铁舌的影响如图6左端所示,它使整个圆周上的折边宽度减小。接缝焊错位则使折边沿圆周方向宽度不等,形成如图7所示的螺旋线状折边外缘。
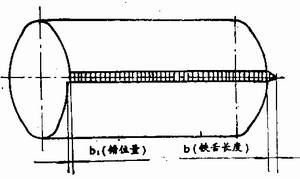
图5 常见的两种桶坯缺陷
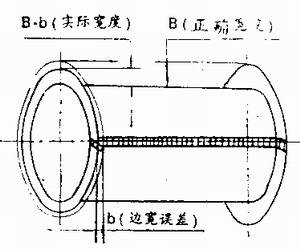
图6 缝焊铁舌对折边精度的影响
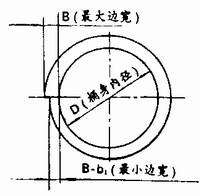
图7 接缝错位对折边的影响
目前,很多企业暂无条件采用自动缝焊机或焊缝挤压修边机,于是采用下列方法保证桶坯的尺寸精度:用纵横双向冲剪保证下料的对等边和垂直度;用定位卡和正确操作提高点焊精度;在“三合一”机上料前用手持砂轮去除缝焊铁舌及磨薄桶口缝焊重叠厚度等。采用这些措施后,效果相当理想。
4.波纹胀压加工。传统滚压工艺加工波纹的主要目的在于钢桶的习惯性外观和增加桶身的局部刚性。 “三合一”机因波纹胀压加工方式的固有特点,使形成的波纹对钢桶的力学结构已产生影响。
(1)桶壁强度。如图8所示。传统滚压工艺是在桶身转动中采用上下一付轴向凸凹相问的可转辊轮作径向进给,滚压出波纹。这种工艺的优点是波纹清晰,但在滚压中因波纹部位桶身材料受到双滚限位强制拉伸,不可避免地引起桶壁局部变薄,从而使桶身强度受到一定程度的破坏。“三合一”机波纹采用如图9.所示的胀压工艺加工,桶身和波纹模均不转动,只由各道波纹模依次向外作径向进给胀出波纹。加工过程中,波纹部位材料自由流动,仅使桶身缩短而未导致桶壁变薄,从而保持了桶身的原有材料强度。实现这一保证的主要条件。一是各道(图中示出其中四道)波纹胀模的径向进给运动不是同时,而是依次的,即按顺序先加工出第一道波纹,然后依次加工第二、第三、第四道波纹。这就防止了多道波纹延伸变形时的相互干涉导致材料变薄;二是各道波纹模问预留出轴向间隙(图9中的X),这就使波纹成型时的桶身缩短成为可能,从而保证桶壁材料变形时可自由流动而不致于变薄。
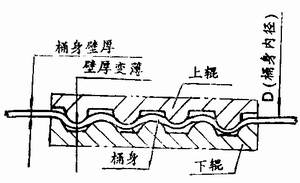
图8 传统波纹滚压的桶壁变化
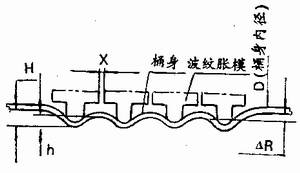
图9 “三合一”波纹胀压加工特点
近年“三合一”机对波纹模采取了加大间距和高度等措施,提高了波纹成型的清晰度。
(2)桶身径向刚度。“三合一”机的波纹胀压工艺使桶身刚度得到较大幅度的提高。如图9所示,“三合一”机的波纹胀压使桶身整个波纹段长度上的波纹根基高出原位置△R高度。这就给传统的外观修饰性波纹赋于新的意义——提高桶身的径向刚度。这种胀压波纹相当于坐落在长100多毫米、高△R的宽筋上。桶身的这两道宽筋大大提高了它的径向刚度。对于200升桶身, 图9中的宽筋高△R≈1.5mm,波纹高h=2.5mm,波顶距桶壁总高H=h十△R=4mm。即无论在宽筋范围内或宽筋范围外,测得的波纹高度均符合GB325标准的3±1尺寸要求。由于波纹段钢桶内径由D增大为D+2△R, 因而其容积并不因桶身的缩短而减小。计算可知,200升钢桶2×6道波纹,当△R=1.5mm时,宽筋所增大的内径可补偿因宽筋引起的△L=3.2mm的桶身缩短。
|