谈缩颈机的改进
沈阳市制桶厂 董宏
在缩颈桶的生产过程中缩颈工序是关键工序,直接影Ⅱ向钢桶的质量,缩颈机的好与坏即影响缩颈质量,同时也影响其成品率及生产率。目前,很多厂使用的缩颈机工作状态很不稳定,给使用和调整带来很多困难。
缩颈机的基本工作原理大都是桶身在上下两辊之间自由旋压,下辊转动带动桶身转动。两辊之间在未压实的时候,桶身转动不平稳。旋压时,因桶身没有定位,桶身擅动,左右移动,致桶身尺寸误差很大,也给翻边和卷管带来困难。不易保证桶身高度、桶颈直径及圆度,并且压出的缩颈易起皱,出现较多的废品。针对这些问题,设想了一种新缩颈机的设计方案。为了解决上述问题,采取了以下措施:实体分离式下辊;上辊液压驱动;桶身定位。
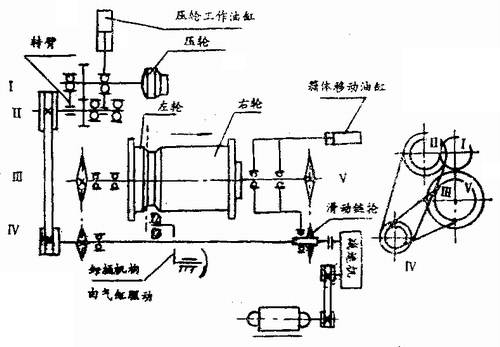
图1 缩颈机传动系统
1.传动系统。见图1。通过减速机动力传给Ⅳ轴。Ⅳ轴为主传动轴,其它各轴动力全都来自Ⅵ轴。为了保证箱体的移动,Ⅳ轴左端链轮与轴采用滑链结构。为了保证Ⅲ轴与Ⅴ轴的同步运行, Ⅲ轴和Ⅴ轴Ⅳ轴的传动采用链传动。该级转速较低,链传动可以满足需要。Ⅱ轴与Ⅵ轴采用三角带传动。压轮与下轮(左、右轮)接触时,压轮与下轮的传动比是有变化的,而皮带有一定的滑差,且压轮受力不大,将皮带传动用在低速非常适宜。 Ⅰ轴与Ⅱ轴采用齿轮传动的目的是:
①结构紧凑;
②满足转向的需要;
③使Ⅱ轴成为回转中心。
当压轮被工作油缸向下推进而围绕Ⅱ轴回转,上压轮向下靠近下轮开始工作。工作过程如下:
桶身到位;箱体左移、右轮穿过桶身中心,向左轮靠拢定位;同时,右轮中心胀紧机构顶起,将桶身固定;然后,上压轮向下逐渐接触桶身,逐渐旋压成型;压轮抬起;卸桶机构向上抬起卡住桶颈;箱体右移,右轮退出;卸桶机构归位。
采用这种系统利于操作,适于自动控制。
2.下轮(左、右轮)的结构分析
下轮分为左轮和右轮两部分,参看图2。左轮和右轮分别与Ⅲ轴和Ⅴ轴相联。左轮与右轮转速相同。右轮V轴安装在箱体内。当箱体在油缸的作用下左移,右轮穿过桶身与左轮闭合。在闭合的过程中,件2退回,弹簧5压缩,推动件?绕轴11向外翻转。件12固定在件7上,件12在右轮的壳体9的四周上。件12随着件7向外翻转,从而将桶身固定在右轮上。当右轮退出时,弹簧5不受压缩,恢复原状,处于自由状态,而件7在弹簧8的作用下复位。
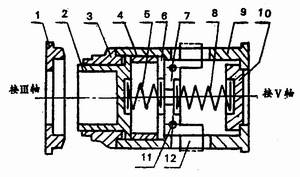
图2 左、右轮工作示意图
这种结构的目的是:使下轮成为实体,而且即能将桶身固,定,又能将桶身退出。该结构对于提高桶颈的圆度,保证桶身的尺寸相当有利。由于桶身处于受控状态,故不在上轮、下轮之间滑动,使缩颈处规整,并防止出现波纹、裂口。即提高了桶的成品率,又提高了生产效率。
3.桶身的定位、固定与退出。见图3。
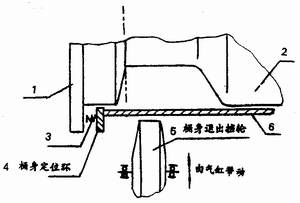
图3 定位、退桶身示意图
在右轮2与左轮1靠近的过程中,桶身定位环4在弹簧3的作用下,将桶身推到右轮2的右端定位。由于定位环4接触桶身,桶身到位,弹簧3继续被压缩。同时,图2中的弹簧5:i也被压缩,使图2中的件7翻转,达到胀紧的目的。
当桶身缩颈后,一组挡轮5向上抬起,进入缩颈处。当右轮退出一定距离后,桶身的胀紧力消失,继续退出直至初始位置。由于一组挡轮5的作用,桶身被留在空位。桶身或由气缸推出或落在传送链上送出。
4.特点及效果分析
(1)实体分离式下辊 实体下辊可以充分保证桶身尺寸公差(桶颈直径、桶身高度、桶颈圆度等)。
为了使桶身退出,下辊必须做成分离式,由左轮与右轮组合而成。左轮与右轮转速相同没有摩擦。在油缸的作用下右轮与左轮压紧,保证正常运行。
(2)在下辊上固定桶身 桶身固定在下辊上,保证了桶身在上辊和下辊之间没有相对滑动,不易卡壳。由于桶身与左、右轮处于实体状态,且不能相对滑动,因而消除了桶颈处的裂纹和起皱。
(3)油缸驱动上辊 油缸推进效果好。一是推杆的速度可调,可根据板厚、材料的要求调节。二是在空行程时,可有快进快退,节省时间。三是辊轮磨损修复后易补偿行程。
(4)适于较大批量生产d因由所生产桶的规格确定下辊,以及不同的规格桶径传动比不同,需要更换挂轮,小批量生产时显得麻烦。
|