钢桶涂装车间洁净度探讨
文/杨文亮
目前,高清洁桶已经成为很多钢桶高端用户的正常需求,在用户要求不断提升的情况下,一些制桶企业也开始对生产车间进行改造,以满足高清洁桶的生产要求。生产高清洁桶,最关键的工序是在后段,因为既便是前段生产时不够清洁,在后段涂装前处理工序中,都可以被清洗地干干净净。所以,钢桶涂装车间的洁净度,才是保证生产高清洁桶的关键环境。
一、什么是洁净度?
洁净度指以表征单位体积空间内空气中所含微粒大小及数量的多少,是区分空间洁净程度的标准。
涂装清洁度泛指整个涂装车间空气洁净程度(含尘量)。
事实上,涂装车间均把钢桶表面清洁度、涂装各工序清洗用水污染度、空调供风和压缩空气干燥及洁净度、涂料及各种原辅材料本身清洁程度等均列入洁净度管理项目,避免污染源二次污染。
洁净间(区)是指需要对尘粒及微生物含量进行控制的房间(区域)。
根据生产工艺要求,应对洁净区划分为高度洁净区和一般洁净区。洁净间(区)内空气的微生物数和尘粒数需要定期监测和记录存档。
二、洁净度标准
1、国际标准(ISO14644)
空气洁净度标准是指每1m3空气中含有一定粒径的粒子浓度的限制指标。国际洁净室标准ISO14644中等级级别分别有ISO1~9九个等级(见下表ISO14644-1):
ISO分级 |
最高浓度极限(颗粒数,个/m3) |
5μm颗粒数,个/2.83L |
近似对应传统级别 |
0.1μm |
0.2μm |
0.3μm |
0.5μm |
1.0μm |
5.0μm |
ISO1级 |
10 |
2 |
|
|
|
|
|
|
ISO2级 |
100 |
24 |
10 |
4 |
|
|
|
|
ISO3级 |
1000 |
237 |
102 |
35 |
8 |
|
|
1级 |
ISO4级 |
10000 |
2370 |
1020 |
352 |
83 |
|
|
10级 |
ISO5级 |
100000 |
23700 |
10200 |
3520 |
832 |
29 |
|
100级 |
ISO6级 |
1000000 |
237000 |
102000 |
35200 |
8320 |
293 |
|
1000级 |
ISO7级 |
|
|
|
352000 |
83200 |
2930 |
8.2919 |
10000级 |
ISO8级 |
|
|
|
3520000 |
832000 |
29300 |
82.919 |
100000级 |
ISO9级 |
|
|
|
35200000 |
8320000 |
293000 |
829.19 |
|
2、中国标准(GB/T16292-1996)
粒径、数值洁净度级别 |
尘埃最大允许数/立方米 |
微生物最大允许数 |
≥0.5μm |
0.5μm |
浮游菌/立方米 |
沉降菌/皿 |
100级 |
3500 |
0 |
5 |
1 |
10000级 |
350000 |
2000 |
100 |
3 |
100000级 |
3500000 |
20000 |
500 |
10 |
300000级 |
10500000 |
60000 |
- |
15 |
3、制桶行业适用的标准:
针对钢桶涂装车间不同的区域,制桶企业应以下表所示的洁净度作为标准:
级别 |
名称 |
区域范围 |
尘粒子含量限度(个/2.83L) |
检查频次 |
ISO14644 |
1~5μm |
5~10μm |
>10μm |
次/周 |
等级 |
1 |
高洁净区 |
喷漆室、流平区、烘干炉、调漆间 |
<50000 |
0~10 |
≤1 |
1 |
ISO7级 |
2 |
洁净区 |
前处理线、风冷区、上盖区、印标区 |
<50000 |
10~100 |
≤10 |
1 |
ISO7级 |
3 |
一般洁净区 |
输送轨道、车间办公室、人员通道、车间卫生间 |
- |
- |
≤100 |
1 |
ISO8级 |
4 |
其它区 |
仓库等 |
- |
- |
≤100 |
1 |
ISO8级 |
目前,制桶企业涂装车间的高洁净区域在静态下洁净度控制在IS07级以上。
三、感性上认识微粒粒径
一般微粒粒径对比:
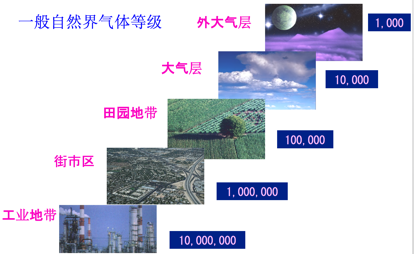
四、钢桶涂装车间洁净度的控制
1、日常监控:车间环境空气微粒含量的监控和检测
按照制桶行业涂装洁净度标准,基本上可以分为四个区域进行划分(高洁净区、洁净区、一般洁净区、其它区域)。各个区域的含尘量均有量化的数据标准。为了达到上述等级,可以定期用灰尘测量仪测定车间各区域空气含尘量。
2、日常监控:车间通风环境监控
涂装车间的风平衡需满足工艺要求,喷漆室、厂房需保证微正压。其余区域可维持常压状态。车间的通风环境需要定期进行监控和统计。
序号 |
检测项目 |
理论值 |
检测频次 |
检测方法说明 |
1 |
风速 |
喷涂区:0.45~0.5m/s
流平区:0.2~0.3m/s |
1次/周 |
将风速仪的探头置于离格栅1m高处,每个区可均匀检测4~10点 |
2 |
风向 |
按设计要法庭 |
1次/周 |
将20cm长的磁带条悬浮于各区间,检查磁带条的飘动方向 |
3 |
正负压 |
微正压 |
1次/天 |
将20cm长的磁带条悬浮于喷漆室门上,打开喷漆室门,检查磁带条的飘动方向 |
3、日常监控:洁净度控制环境(分区域)
(1)高洁净度区域:
◎人员进入喷漆洁净间时,必须在风淋室吹风≥10s,非区域人员进入洁净间需穿戴一次性鞋套;
◎作业人员进入喷漆室需穿戴一次性连体服,一次性连体服一天一换;
◎烘干炉工艺维护,需根据车间工艺要求在停产期间进行维护;
◎调漆间的门窗日常保持关闭状态,不得随意打开门窗。在接受油漆时,需先关闭内部大门,再开启外部大门,待油漆全部进入车间后,先关闭外部大门,再开启内部大门,搬运油漆。严禁同时开启内、外门;
◎调漆间除有相关工作人员进出外,其他人员禁止进入;
◎化学品进入车间前,需对包装桶表面灰尘进行轻擦,保证干净的情况下,方可进车间;
(2)洁净区域:
◎前处理原料定置摆放表面无灰尘,地面保持整洁;
◎进出UBS喷胶室,需更换劳保鞋;
(3)一般洁净区域及其它区域:
◎原辅材料进入车间需检查外表面的洁净,杜绝灰尘随辅材进入车间;
◎需按周期对设备、工装、输送装置进行清洁;
◎厂房及喷漆室需保证微正压;
◎定期需对工艺装备、喷涂工具等工具进行清洁,保证工具上灰尘、杂物清理干净。
|