涂装连续生产线废气焚烧集中供热系统
文/许言午
涂装连续生产线废气焚烧集中供热系统,通过对钢板彩涂线中产生的废气再利用,将废气用来预热换热装置,节省了能源,同时废气最终均进入燃烧炉二次燃烧,使得有机溶剂和部分未完全燃烧的废气充分燃烧,再通过热风管排出,将高温焚烧产生的热能直接送回烘房进行能源利用,节能效率达到40%~70%,对外界无污染,更具环保性(连续生产线的生产能力不同,降低能源消耗比例不同)。
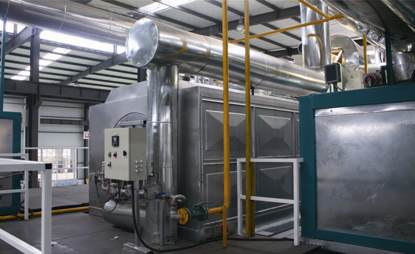
一、主要技术特点
1、主要研发要点
1)有机溶剂挥发气体的收集和无害化处理。废气收集和无害化处理技术由变频风机和收集管形式收集,保证烘房内气体成微负压状态,以减少气体外泄,废气抽取量应稍大于新风补充量,以保证有害气体含量在爆炸极限浓度25%以下,保证炉体和生产安全。燃烧室内的燃耗温度至少在720℃以上,以保证有害气体能充分裂解燃烧,有机溶剂热值得到利用并且达到气体无害排放。
2)余热利用。利用三级其他换热器分别预热从炉内抽出的废气至500℃左右以便更好进行裂解燃烧:加热从车间抽入的新鲜空气至200℃左右输送至前处理带钢倾斜后的水汽烘干;最后一级采用列管式水换热器对从前处理输送过来的清洗液进行加热处理至60℃~80℃左右送回到前处理对原材料钢板带进行涂前清洗处理。
整体方案为:技术自主开发,设备自行制造。具体技术、设备的试验与生产厂家配套合作,并吸收消化国内外的相应的先进技术应用于本系统。
2、关键技术要点
本系统研发的涂装连续生产线废气焚烧集中供热系统采用高温裂解燃烧处理方式处理废气(排放达标)、采用蓄热式焚烧炉降低装机负荷(降低碳排放)、利用废气放热和余热技术提高能源利用率(节能);将涂料烘房前段排风排出的有机废气,引入焚烧炉废气预热换热器中预热;再经高温炉膛,使该有毒有害的有机废气在720°C~750°C高温炉膛中裂解燃烧,同时裂解后废气中的有机溶剂的C、H成分的可燃烧值也作为燃料燃烧,热能得到利用,从而节省了能源;燃烧后产生的高温热空气(达到环保GB16297-1996二级排放标准)通过离心风机输送回涂料烘房各循环风机加热室,用来加热涂料烘房;多余的低温热量可送至生产线上的辅助用热设备,以提高热能利用率,节约能源40%~70%(连续生产线的生产能力不同,降低能源消耗比例不同)。
3、特色创新要点
1)将涂装生产线产生的有机废气在焚烧炉内进行充分裂解后,保证了涂料中的有机溶剂挥发物经过处理后再排放到大气中,不会对大气产生污染(达到环保GB16297-1996 二级排放标准);
2)运用变频方法控制负压焚烧,并在炉体上安装开启式防爆装置,以确保安全运行;
3)将原生产线中的所有加热设备(5—11 台)废止,用焚烧炉替代供热(集中),并将废气燃烧裂解过程中的有机溶剂中的C、H 成分的可燃性热质作为燃烧能源加以充分燃烧利用,降低了其他燃料的使用,节省了燃料的使用量,达到了节约能源的作用;
4)焚烧炉采用优化数据的蓄热式设计,降低整个生产线的装机负荷容量(由原来的5.6MW 降为2.8MW),最大程度的实现低碳生产。燃烧后产生的高温热空气的余热不仅可以加热待焚烧的废气,同时还可通过离心风机输送回涂料烘房各循环风机加热室,用来加热涂料烘房,以提高热能利用率。
该涂装连续生产线废气焚烧集中供热系统的工作的流程如下:
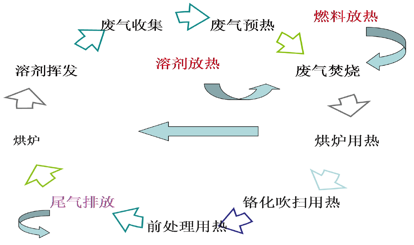
二、技术经济性分析
该系统目前已获得相关发明专利3项,实用新型专利24项。其主要技术指标如下:
1、燃烧室废气裂解温度720°C~750°C;
2、废气预热器出口烟温550℃,出口废气废气温度620℃;
3、新风换热器出口烟温350℃,出口新风温度220℃;
4、最后一级水换热器出口烟温180℃,出水温度70℃至80℃;
5、吨钢天然气消耗小于10NM3/T;(原为24NM3/T)
6、废气充分裂解燃烧后无害排放,排放排放温度≤180℃。
系统的顺利实施,以天津市新宇彩板有限公司壹条生产线年产18万吨,无本系统每吨天然气平均单耗24m3/t,3.0元/立方米的天然气价格来计算,其能源费用为24×3×18=1296 万元,实施本系统后达到吨天然气平均单耗9.5m3/t,其能源费用为9.5×3×18=513万元,节能61.5%,每吨彩涂钢板节约燃料成本43.5元,年产18万 彩涂钢板每年节约43.5×18=783万元。该企业有6条相同产能的生产线,若全部按此计算每年节约燃料成本783×6=4698万元。
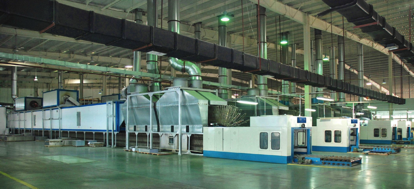
|