放射性核废物贮运容器柔性自动化生产线研发及应用
文/侯斌
摘要: 介绍了用于核废物贮运容器柔性自动化生产线的组成、主要设备柔性化方案,详细阐述了所采用先进的七层矩形卷边、小弯曲半径的折边、内胀外箍胀筋整形、自动擦桶代替清洗磷化线和以铣代磨产业化生产工艺。生产运行表明: 该生产线运行稳定,安全可靠,经济效益显著,完全可以替代进口产品,以供本行业技术人员参考与借鉴。
关键词: 放射性核废物贮运容器; 柔性化方案; 产业化生产工艺
0 前言
针对核电站中放射性核废物处理的需求,研发了一种柔性的放射性核废物贮运容器自动化生产线,改生产线采用了5种先进的产业化生产工艺,提高核废物容器制造精度,使核废物容器制造达到先进的行业水平,推动核废物容器在核电站的应用,满足了我国多规格核废物容器产业化生产的要求。从而保护环境,有利于核能的发展和应用。
1 生产线的组成
该生产线由容器成型设备、传送装置和控制系统三大部分组成。其中,容器成型设备由卷圆焊接线、折边机、胀筋整形机、自动擦桶机、卷边机、自动卸桶机、喷漆线、固化线、印字机、250吨冲床、预卷喷胶机、滚箍机和13套底盖模具等组成; 传送装置由6条输送机、翻桶机、以及上、卸料机械手等组成; 它们依靠自动控制系统来完成确定的工作循环。
2 生产线主要设备柔性化设计方案
某放射性核废物贮运容器有7中规格品种,要求在一条生产线上完成。为适应这些规格的材质、料厚、直径、容器高度、开口形式等结构参数的变化,整条生产线和设备(机床)部件应具有充分的可调变性,实现生产线的快速(4小时内) 可调整即柔性化,在生产线具备柔性化功能的同时,还要操作简单、实用和方便。
具体是在柔性化生产线上的折边机、胀筋机、整形机、擦桶机、卷边机、预卷喷胶机、铣边机等设备和生产线上的工件输送机构(机械手)采用轴向和径向可调或可换的总体和部件设计,凡涉及被加工工件结构和作用尺寸的零部件设置有螺纹副调整机构、T型槽位移调整机构、长槽位移调整机构、铰链接机构、销定位或止口定位互换装置、半瓦连接互换装置、分体式结构互换装置、交换齿轮互换装置等零部件调整和更换环节,在机械)液压、气动等动力系统的作用下,通过控制系统的集中控制,对各项参数进行迅速调变。
在生产线上包括每个单机和输送机构(机械手)中设置必要的调整环节,运用 PLC及单片机等控制技术对动力部件的工作位置、作用尺寸、工作压力、运动速度、循环程序等功能参数进行快变、快换或快调,实现核废物贮运容器自动化设备柔性化。
3 采用的先进产业化生产工艺
3.1 七层矩形卷边工艺
近几年来,德国、法国等国家率先在一些较重要的领域,使用了七层矩形卷边工艺钢桶容器代替传统的七层圆形卷边结构。从力学强度方面考虑,七层矩形卷边截面积更大,强度更好,耐冲击能力更强。在实验中,七层矩形卷边与七层圆形卷边相比,性能提升也非常大。为了实现七层矩形卷边,进行了多次工艺试验和对德国进口卷边机的研究,摸索出了七层矩形卷边工艺的基本流程,设计了四导柱式六头卷边机,采用第一道滚轮预卷,滚轮槽型较小;第二道滚轮卷边,滚轮槽型较大;第三道滚轮整形,滚轮为矩形槽。三道滚轮实现了矩形卷边的最后结构和形状,取得了较好的效果。
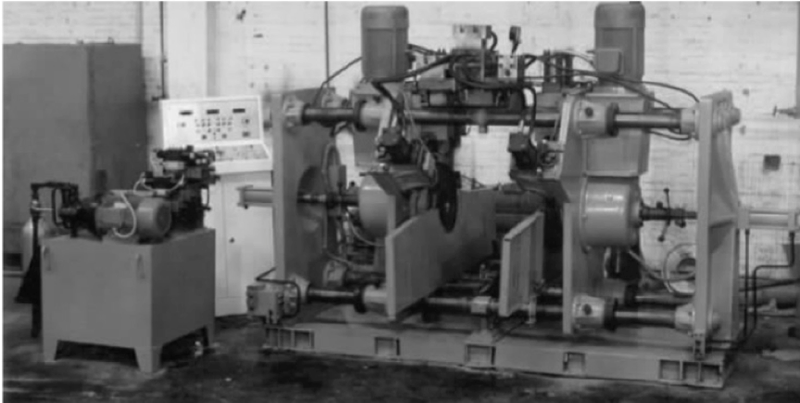
图1 六头四导柱式卷边机
3.2 小弯曲半径的折边工艺
如图2所示,某320L核废料容器要求工件上沿及下沿折边弯曲半径尺寸均为R3.5mm,而国内现在使用传统的挤压折边工艺其挤压折边弯曲半径尺寸均为≥R8mm。该生产线容器折边采用旋压折边成型技术,即为液压传动旋压成型板边,带有独立的电器驱动和液压操作的对中装置,成型和对中心定位机构分别可调,以适应柔性化生产的需要。工件(容器)连同主轴大盘、定尺隔圈、偏心盘一起旋转,上滚轮下压,上滚轮接触到工件后,偏心盘在上滚轮压力下旋转,而偏心盘受到向下的压力后导致轴心下移,同时使工件进入折边成型,直至达到规定形状和尺寸。上滚轮行程到位后,反向往上移动,偏心盘在弹簧作用下,带动已完成的折边成型工序的工件。滚压折边重复精度可达±0.1mm。
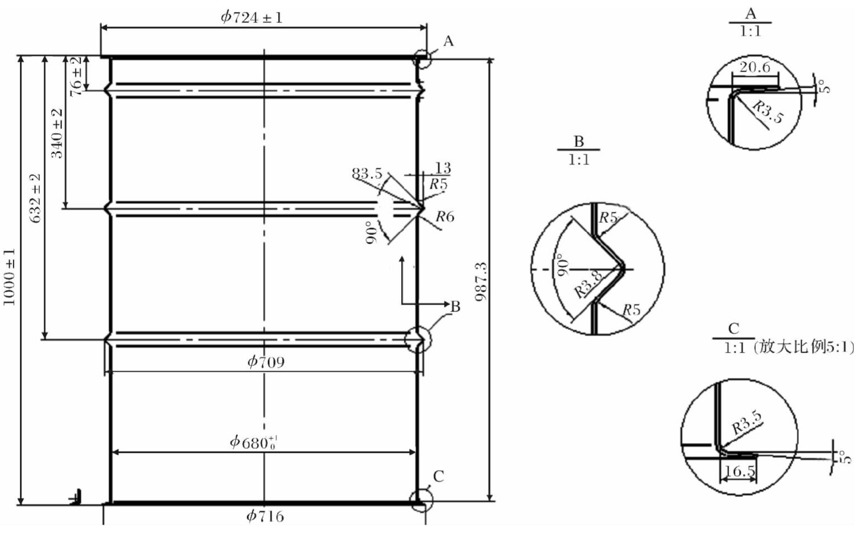
图2 320L核废料容器
3.3 内撑外箍胀筋整形工艺
由于核电站用来转运核废物容器的机械手对容器的胀筋形状和筋的精度要求较高,且工件的材质较硬和料厚较厚。该核废物容器要求不但要胀制在容器内表面向外挤出突起的环形筋,还要胀制在容器内表面向内挤出突起的环形筋(2mm厚不锈钢W型筋) 。而国内目前还没有用胀制工艺加工W筋的报道,普遍采用滚制加工的方法。为了适应厚料(料厚3mm) 、不等距大筋(料厚1.5mm) 、不锈钢材质以及复杂大筋形状(料厚2.0mmW筋) 的胀筋加工,经过计算和试验,在国内首创性提出了内撑外箍胀筋整形胀压新工艺,将胀筋工序和整形工序同时进行,一次性完成。不仅能胀制复杂W筋,而且使核废料容器加工精度达到了 ±0.5mm。
图3为XJY203型胀筋整形机。该机型胀筋部分采用胀压工艺,立式结构、地坑式布置、全部动力由液压装置提供。床身由钢板焊接结构的主机架构成,主机架中的主轴滑动导套采用了润滑系统。工作油缸的活塞杆与成型工具的主轴相连接,工作油缸下移时,胀形机构驱动12瓣胀膜体完成径向进给运动,实现桶身环筋的胀形。
主机设计采用可调式方案,以达到更换成型工具满足不同规格钢桶(直径: 385~710mm;料厚: 0.8~3mm)的要求。
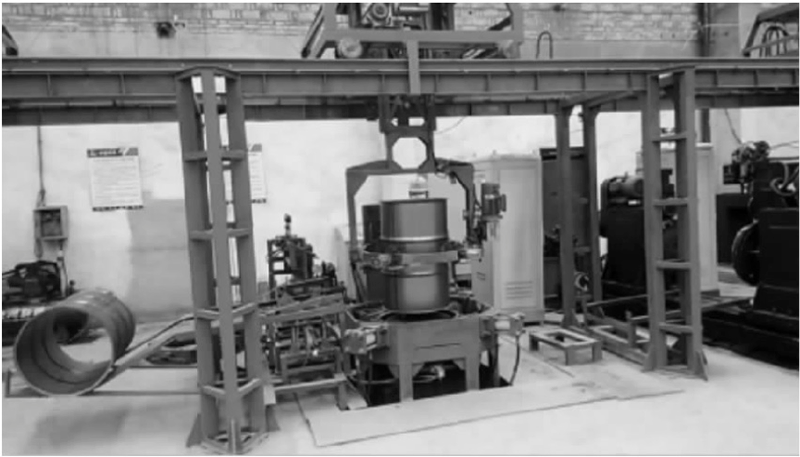
图3 XJY2012型胀筋整型机
3.4 自动擦桶代替清洗磷化线
全自动擦桶机包括毛刷、机架、气缸、导向座、导向防转杆、行程限定机构以及桶身支承轮等。通过气缸带动毛刷作直线往复运动,桶身支承轮带动钢桶桶身旋转,从而自动完成桶身内、外表面的清洁工作,通过控制气缸的行程可适用于不同桶高的钢桶。全自动擦桶机生产效率高,投资小、较原先的清洗磷化线节省生产成本30%~40%。
3.5 以铣代磨工艺
采用铣边工艺实现了与全自动生产线的联线,属国内首创。设计有防止刀具切入或切出时撕裂钢板,出现打角现象的钢板输送自动变速机构; 动力头偏移角装置及防止板材在铣削过程中抖动或上翘的压料装置; 45°大前角,却削负荷小的四面刃端面铣刀盘; 设置有四路位移测量系统,可视性显示铣头的调节量,实现了铣头的精确调整,适应不同厚度板材的生产。
4 运行情况
本生产线于2013年1月在中国核工业华兴建设有限公司扬州加工厂进行了安装调试,调试顺利成功。2013年4月24日正式开始生产至今。实践证明,研发是成功的。所有生产的5种规格的产品达到课题任务书的目标。生产线运行可靠、平稳,工艺流程设计合理、操作便捷、电气系统及液压系统工作可靠,实现了机、电、液、气一体化设计,综合评价用户满意。
自生产投产后,具有明显的经济效益和社会效益。并获国家实用新型专利 2项,专利号:ZL20130521130.0和ZL201520352319.0,已有中核集团某燃料元件有限公司定制了一条核元件容器生产线。
参考文献:
[1] 杨文亮,辛巧娟. 钢桶制造技术[M]. 北京: 印刷工业出版社,2006.
[2] 杨文亮,辛巧娟. 金属罐制造技术[M]. 北京:印刷工业出版社,2009.
[3] 杨文亮,辛巧娟. 钢桶包装标准应用指南[M]. 北京: 印刷工业出版社,2013.
[4] 汪大年. 金属塑性成型原理[M]. 北京: 机械工业出版社,1981.
[5] 杨文亮. 新型七层矩形卷边工艺实践[J]. 钢桶,2014(4).
[6] 许林成. 包装机械原理与设计[M]. 上海: 上海科学技术出版社,1988.
[7] 杨文亮. 钢桶生产线的设计[J]. 钢桶,2013(2).
[8] 罗虎文. 钢桶五层平卷边不良品的发生及克服方法[J]. 中国制桶信息,1988(3).
[9] 杨一飞. 立式全自动钢桶生产线的技术特点[J]. 钢桶,2011(4).
[10] 王志坚. 制桶设备生产线新技术与应用[J]. 钢桶,2015(1).
[11] 杨文亮. 放射性固体废物钢桶的性能及试验[J]. 钢桶,2013(4).
|