闭口包装钢桶生产过程检测技术分析与研究
译/林陈彪
摘要:根据GB/T325-2000标准要求,对闭口包装钢桶生产过程检测项目进行技术分析和研究,提出切实可行的检测方法。参照GB/T325-2000标准要求,结合生产过程,应用比对法、测量法、计算法、试验法及源头控制等,对生产实践中的检测方法进行提炼。通过比对、测量、计算、试验以及源头控制等方法,可逐项对GB/T325-2000标准提出的要求或指标进行检测或控制。利用技术分析办法,对生产过程中的产品质量进行监控,可以防止不合格品的生产、流转和放行出生产企业。
关键词:闭口钢桶;生产过程;标准要求;技术分析;检测方法
引言
闭口包装钢桶是指桶顶不可以移动的钢桶。其中,小开口钢桶其注入口直径不大于70mm;中开口钢桶其封闭器直径大于70mm,小于钢桶的内径,国际上亦称为为活动盖钢桶。闭口钢桶广泛用于盛装液体状态的化工、石油、食品等产品的出口包装。在液体危险货物的出口中,更离不开闭口钢桶。危险化学品在装卸、贮存、运输过程中,将不可避免地受到碰撞、跌落、冲击和振动。因此,闭口钢桶质量要求高,检测和试验环节多,目的是对生产过程中的产品质量进行监控,以防止不合格品的生产、流转和放行出生产企业,并及时对其进行纠正,避免造成更多损失而对用户造成不良影响。
1 基本要求、技术分析及检测方法
钢桶生产行业自1995年开始实行生产许可证准入制度。企业应具有按规定程序批准的正确、完整的图样和技术文件,具备许可证产品质量的生产设备、工艺装备和测试手段。要有一支保证产品质量和进行正常生产的专业技术人员、熟练工人及检测人员,以及有效的质量管理体系,能够生产出达到国家标准或行业标准的产品。但是,取得生产许可证仅仅说明了企业具备生产该产品的资格。要保证生产的产品必定合格,还有赖于获证后的生产状态和质量保证能力。生产过程检测是指在生产过程中对所生产钢桶以各种质量控制手段根据产品工艺要求对其规定的参数进行检测,以达到对产品质量进行控制的目的。过程检测的目的是为了防止出现大批不合格品,避免不合格品流入下道工序继续加工。
1.1 桶身、捅顶和桶底用材
1.1.1 要求
标准规定桶身、捅顶和桶底均由整张薄钢板制成,不允许拼接。
1.1.2 技术分析
虽然目前机械制造技术水平可对钢桶某个部位乃至有限部位进行焊接方法拼接,且在逐个检测条件下,钢桶成品仍然可以满足使用要求,但是考虑到目前钢桶企业基本是大批量生产,大量采用薄板开卷矫平剪切流水线,见图1,并按规定的抽检方式对产品生产过程进行抽检测,而拼接增加了不合格产品的风险点。为了有效避免质量事故发生的风险,标准规定桶身、捅顶和桶底均由整张薄钢板制成是科学的。
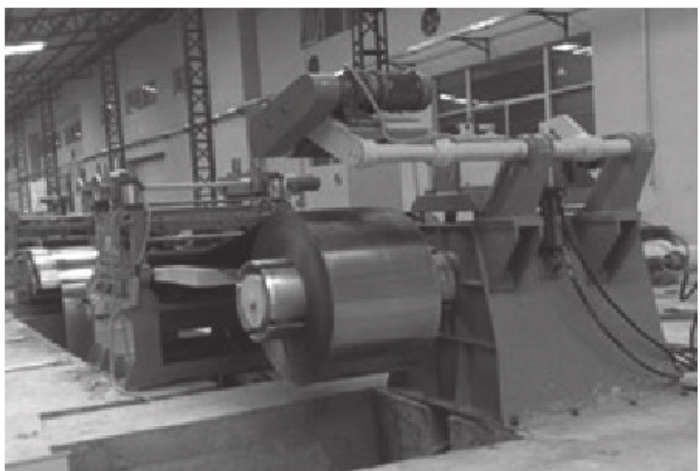
图1 薄板开卷矫平剪切
1.1.3 检测方法
目前,钢桶桶身制作大量采用卷板材料,即使采用平板材料,钢板供应企业在尺寸上均有对应钢桶生产相应的规格材料提供,且是否拼接用观察方法判定,主要检查其锈迹及其是否已处理。
1.2 桶身焊缝
1.2.1 要求
标准规定,桶身焊缝需采用电阻焊焊接。
1.2.2 技术分析
目前,钢桶桶身焊接方式主要有两种:一是电阻焊,主要是缝焊;另一种焊料焊。电阻焊具有生产效率高、低成本、节省材料、易于自动化等特点。我国企业自行开发的新型钢桶缝焊机实现焊接的无级调速实现了高速焊接。对于焊接 200升钢桶,目前焊接速度可提高到每只桶8s的速度,且可实现无需点焊定位的直接缝焊,有效提高了焊接质量,节省了一道工序,是钢桶生产最重要的焊接工艺。
1.2.3 检测方法
桶身焊接的传统工艺是磨边、点焊后缝焊。点焊是将焊件装配成搭接接头,并压紧在两柱状电极之间,利用电阻热熔化母材金属形成焊点,目的是在缝焊前进行准确定位,为难于作业的缝焊作准备。目前,在工装夹具的支持下,已大量采用无点焊直接缝焊工艺。桶身缝焊过程见图2。
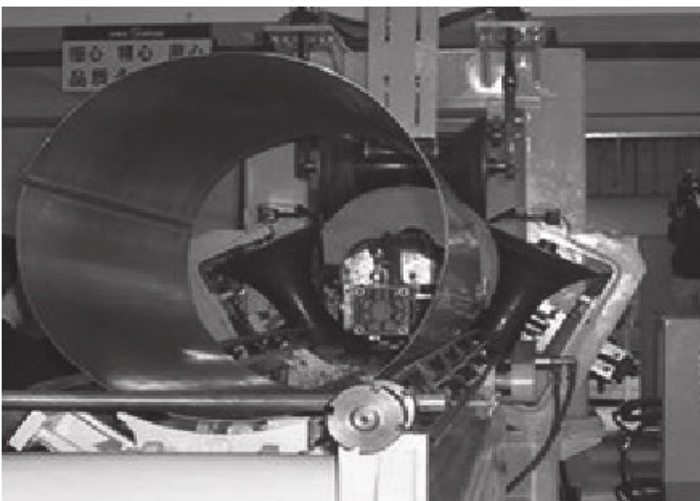
图2 桶身缝焊过程
1.2.4 检测方法
点焊加缝焊工艺焊接桶身过程中,应把握搭边宽度。搭边宽度应在10~12mm,焊点一般为4个,还要检查桶身点焊两头搭边尺寸和焊点是否正确。两端不能出现过大误差,否则也会造成焊接后桶身一端渗漏。采用全自动缝焊机焊接钢桶桶身时,搭边宽度在2~3mm。工件表面上的氧化物、污垢、油和其他杂质增大了接触电阻。另外,要注重检查是否有过厚的氧化物层。过厚的氧化物层会阻碍电流通过,且氧化物层的不均匀性还会影响各个焊点加热的不一致,引起焊接质量的波动。
1.3 桶身型式
1.3.1 要求
标准规定,桶身型式可采用具有2道环筋或两端具有3-7道波纹的型式,也可同时具有2道环筋的型式兼有环筋至桶顶、环筋至桶底之间3~7道波纹。
1.3.2 技术分析
标准提出,桶身型式可根据用户的要求进行商定,但对于纳入《海运出口危险货物包装检测规程一性能检测》要求的200L及以上钢桶,通常采用具有2道环筋的型式兼有环筋至桶顶、环筋至桶底之间3~7道波纹的型式。其他钢桶特别是100L及以下的钢桶,则采用具有2道环筋的型式。闭口钢桶桶身型式关键结构型式见图3。
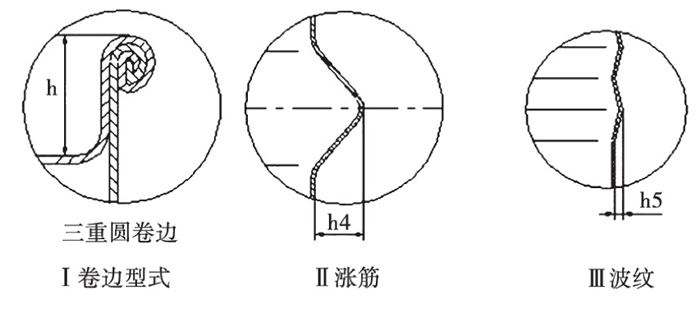
图3 闭口钢桶桶身关键结构型式
1.3.3 检测方法
桶身型式确定后,通过设备及模具工艺进行保证。生产前,通常检查设备及模具的准备是否符合工艺要求;生产过程中,通常检测产生环筋及波纹的模具是否磨损或脆裂缺损。设备或模具异常应及时进行修复,以保证产品质量。
1.4 桶身与桶顶、桶底的卷封及密封填料
1.4.1 要求
桶身与桶顶、桶底的卷封按需要充填密封填料。卷封型式可采用二重平卷边、二重圆卷、三重圆卷边中的一种。
1.4.2 技术分析
对于纳入《海运出口危险货物包装检测规程——性能检测》要求的或在国内流通的危险物品用200L及以上钢桶,应采用三重圆卷边保证性能要求,而未被纳入的则可采用二重平卷边或二重圆卷边,但如果性能达不到要求,亦必须采用三重圆卷边。密封填料则必须具备下列特性:填充性、致密性、吻合性、连续性、稳定性、适应性和工艺性。
1.4.3 检测方法
卷边由封口机或卷边封口机完成。卷边型式则以卷边垂直剖切后检查其断面的方式进行检测。密封填料必须具有一定的弹性、强度和扯断伸长率,目前均由密封填料专业厂家提供,且物理、化学性能应符合其出厂质量证明文件中的承诺。闭口钢桶二重平卷边、二重圆卷边及三重圆卷边见图4。
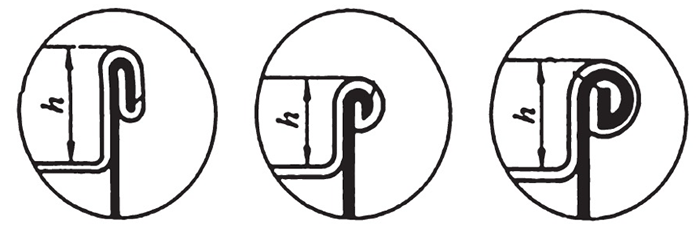
图4 二重平卷边、二重圆卷边及三重圆卷边
1.5 封闭器
1.5.1 要求
标准中提出了钢桶顶上设置封闭器的要求。闭口钢桶所用封闭器有螺旋式、揿压式和顶压式三种。
1.5.2 技术分析
封闭器一般由封闭器专业厂家提供。同密封填料一样,通常采用合格供应商审查并定点供应的方式。封闭器型式也是根据用户要求选定的,安装在桶顶上。不同的封闭器有不同的开口型式。闭口钢桶常用的旋塞式封闭器见图5。
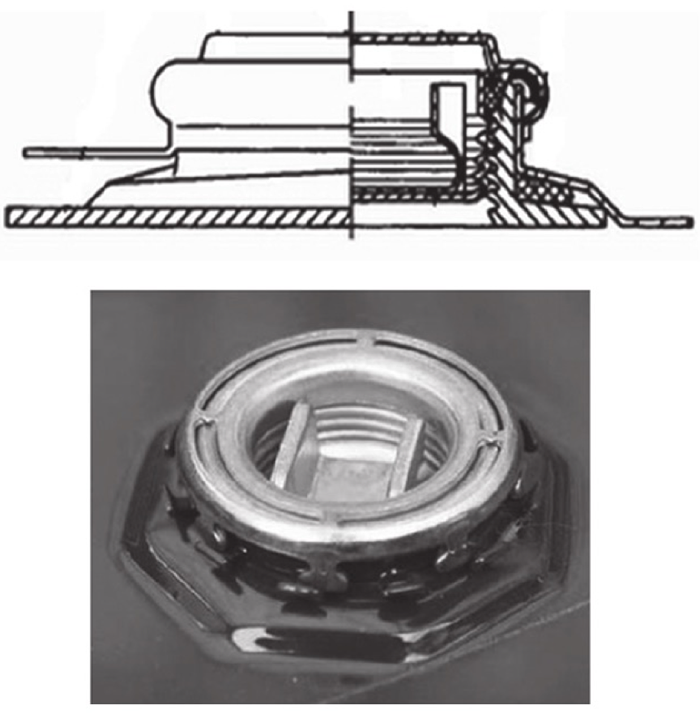
图5 旋塞式封闭器
1.5.3 检测方法
开口型式确定后,就是由压力机及模具来完成工作。检测时主要检查安装过程,特别是安装时保证到位,密封圈的位和螺纹的对正。封闭器装配后密封良好,并保证配合件的互换性。闭口钢桶封闭器装配后的高度低于卷边沿口。
1.6 公称容量和结构尺寸
1.6.1 要求
GB/T325-2000标准中,规定了公称容量从50~208L闭口钢桶的结构尺寸,且均为线性尺寸,分别为内径d、内高H等9个基本要素尺寸。需说明,标准规定了9个要素的基本尺寸值和基本偏差值。
1.6.2 技术分析
根据互换性技术原理,基本尺寸越大及相对次要的尺寸,其基本偏差值就越大,甚至超出相应尺寸自由偏差值。反之,基本尺寸越小及相对重要的尺寸,其基本偏差值就越小。结构尺寸的保证也是对公称容量的保证。闭口钢桶结构见图6。
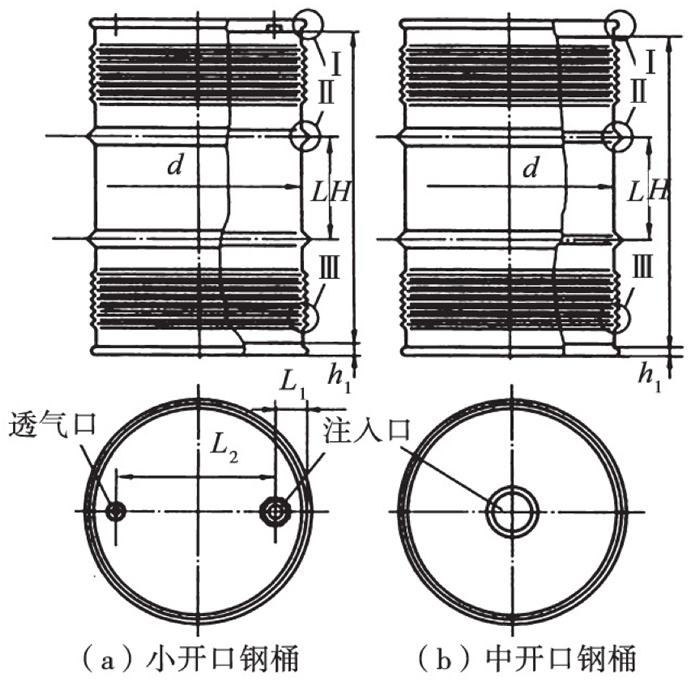
图6 闭口钢桶结构图
1.6.3 检测方法
根据基本尺寸值和基本偏差值,闭口钢桶的长度尺寸主要的检测器具为卷尺、钢板尺、带深度测量功能的游标卡尺以及R度板等。过程应注意,新测量器具在投用前的精度或刻度值的校核或校准。
2 钢桶外观质量的要求及其检测的方法
2.1 外观圆整
2.1.1 要求
钢桶圆整、无毛刺、机械损伤和卷边无铁舌;钢桶的凹瘪不多于2处,每处面积不大于桶身面积的0.7%。
2.1.2 技术分析
钢桶生产过程中,桶顶、桶底加工工序通常由压力机完成,加工与流转过程一般不会产生损伤,而桶身则由卷圆机完成卷圆,其圆整度在制造过程是有保证的。毛刺主要产生在冲裁工序,要使用足够冲裁力的压力机并及时修整模具。个别毛刺的产生要及时在本道工序中予以人工消除。卷边铁舌与封口机工艺行程及R轮形状有关,卷边铁舌通常是R轮磨损所至。
2.1.3 检测方法
钢桶的凹瘪常发生在桶身卷圆后或钢桶封口后的流转过程中。桶身受到机械损伤,比较容易变形或在流转通道中受到障碍物的影响。以200L钢桶为例,其桶身表面积(不计桶顶、桶底面积)为56×3.14×84.5=14858cm2,其桶身面积为凹瘪不多2处,每处面积不大于桶身面积的0.7%,即要求凹瘪应控制在104cm2内。如果是圆状凹瘪,则其直径需控制在11.5cm内。根据企业经验,凹瘪深度应控制在3mm以内,超出应进行人工修复。
2.2 焊接外观
2.2.1 要求
桶身直缝补焊不多于2处,焊疤表面平整,宽度不大于原焊缝的一倍,总长度不大于直缝长度的10%。环筋顶部不允许补焊。钢桶卷边允许整圈补焊,焊缝平整均匀。
2.2.2 技术分析
以200L钢桶为例,桶身直缝900mm长,补焊如果多于2处需要焊补,说明桶身直缝焊接质量存在问题或存在潜在漏点。环筋顶部不允许补焊是基于环筋顶部承担着钢桶装卸、运输时与其他桶的直接接触,而补焊处易产生新的漏点。
2.2.3 检测方法
桶身在与桶顶、桶底封口前,要逐个进行气密性试验。试验中所发现的直缝漏点需及时做上记号,修复方式只能对直缝进行补焊,机器或人工均可,但焊疤表面必须平整,个别焊疤在不影响泄漏的情况下可以进行适当打磨。补焊还应控制其宽度不大于原焊缝的一倍,总长度按要求只能在56mm以内。
3 结语
通过对GB/T325-2000标准要求的研究,对闭口钢桶生产过程检测项目逐项进行技术分析,提出的比对、测量、计算、试验以及源头控制等方法是切实可行的,能够对生产过程中的产品质量监控发挥作用,防止不合格品的生产、流转和放行出生产企业,以及时对其进行纠正,避免造成更多损失而对用户造成不良影响。
|