大凸缘薄壁件冲压成形失效分析及解决方案
文/顾建刚
某排气组件中单件XX.034前板为大凸缘薄壁零件,在开发前期采用常规拉深工艺进行试制,发现中间拉深部位出现了不同程度的减薄及破裂等失效现象,后通过对失效件进行研究分析,精确工艺计算,合理优化成形方案,完善模具结构,成功克服失效现象,顺利完成试制。通过对零件工序间工艺余料的精确计算,提出冲压件工序间“储料”概念,为后续类似结构件成形提供成熟经验。
XX.034前板为某动力装置排气组件之组成单件,外形整体为拉深件,中间拉深方向与外缘拉深方向成反向,最外缘直径与内圆直径比值达3.86,为典型的大凸缘件。
由于此件形状规则,同时材料具有良好的冲压性能,在试制前期采用常规拉深工艺,中间拉深模采用常规90°变形率拉深法(即凹模为直角过渡),但在实际加工过程中发现中间拉深部位转接R角处出现了剧烈减薄及破裂等失效现象。
针对失效现象,对实物零件进行解剖分析研究,尝试减小工序间变形率,提出工序间进行“储料”概念,通过精确计算,重新编排工艺路线,解决了上述减薄、破裂等问题。
零件工艺性分析
XX.034前板零件如图1所示。
材料
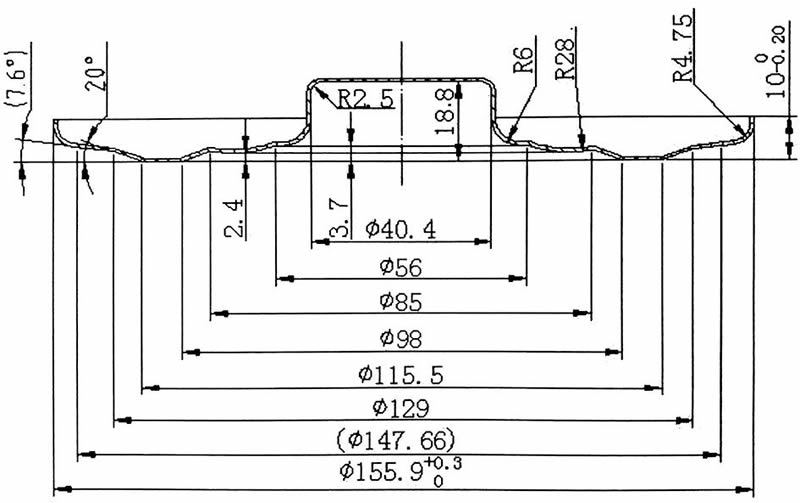
图1 XX.034前板产品图
XX.034前板材料为1Cr18Ni9Ti,为奥氏体不锈钢,料厚为0.8mm。此钢不能用热处理强化,冷加工是强化的唯一手段,工序间可通过热处理进行恢复塑性,消除冷作硬化等现象。此钢具有良好的塑性、韧性及冲压性能,其塑性与日常使用较为广泛的优质碳素结构钢具体对比如表1所示,热处理退火状态伸长率达40%,而20钢退火状态为25%。
表1 材料机械性能对比表
外形尺寸
XX.034前板其壁厚为0.8mm,中间部位有一拉深处,内圆尺寸为φ40.4mm,拉深深度为18.8 mm。由于零件功能性要求,凸缘设计为多型面,各型面均在一定直径处相接,最外凸缘也为拉深处,与中间拉深部位呈反向,高度为10mm。整体结构较为规则,最外缘直径与内圆直径比值达3.86(155.9/40.4=3.86),属大凸缘类结构件。
试制问题及分析
失效现象
对XX.034前板进行工艺性分析,其中间内圆尺寸为φ40.4mm,拉深高度为18.8mm,高径比为0.465(18.8/40.4=0.465),此比值属可一次性拉深成形范畴,再者由于其材料本身具有优良的冲压性,所以在前期安排试制工艺及模具结构设计时,按常规思路将中间拉深模具设计为90°变形率拉深法(即凹模为直角过渡),通过一次成形到位。但投入试模过程中发现,中间拉深处几乎每件均出现了转接R处破裂现象,如图2所示,无法制出合格零件。
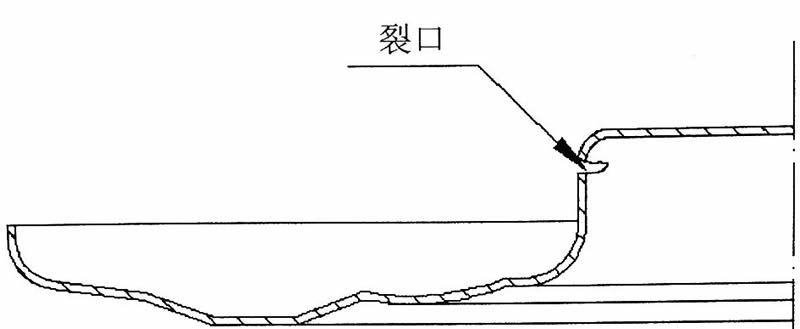
图2 转接R破裂示意图
问题分析
由于试模件出现上述问题,为此开展原因查找及问题分析。在拉深过程中,裂口处对应凸模圆角处,凸模圆角处是侧壁和底部的过渡区,材料承受侧壁较大的拉应力、凸模圆角的压力和弯曲作用而产生的压应力和切向拉应力,在这个区间的侧壁与底部转角处稍上的地方拉深开始时它处于凸、凹模间,需要转移的材料较少,受变形的程度小,冷作硬化程度低,加之该处材料厚度变薄,使传力的截面积变小,成为整个拉深件强度最薄弱的地方。同时将失效件进行剖切,对壁厚进行分析,如图3所示。
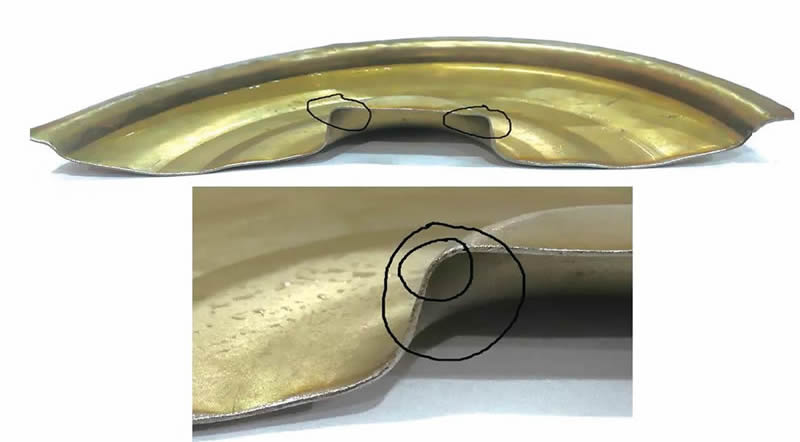
图3 失效零件剖切示意图
由图3剖切实物图可以看出在拉深底部转接R处(画圈处)壁厚出现了严重减薄现象,经测量已减薄至0.3mm(原始料厚0.8mm),此处成为了薄弱区域,所以在此位置最先出现了破裂现象。
通过分析,出现上述现象的主要原因在于由于零件凸缘过大,外凸缘展开后是中间拉深部位的四倍之多。这样造成了外面凸缘的抗拉深力大大超出了中间部位的成形拉深力,外面的材料很难流入中间拉深部位,使中间拉深部位的变形材料不能得到外凸缘材料的及时补充而破裂。
解决方案
工艺优化
要解决此零件中间拉深部位的破裂问题,首先要使拉深部位的变形材料在变形过程中能够及时得到外凸缘材料的补充,为此制定如下成形步骤。
⑴将拉深成形的凹模R加大。一般情况下,此R是零件壁厚的5倍左右,零件壁厚为0.8mm,按理论计算应为R4,零件实际设计要求为R6,虽对成形有利,但为降低风险,优化方案给定的数值是为R10,先拉深到8~10mm的深度,进行固溶处理,消除应力,以利于再次成形(图4)。
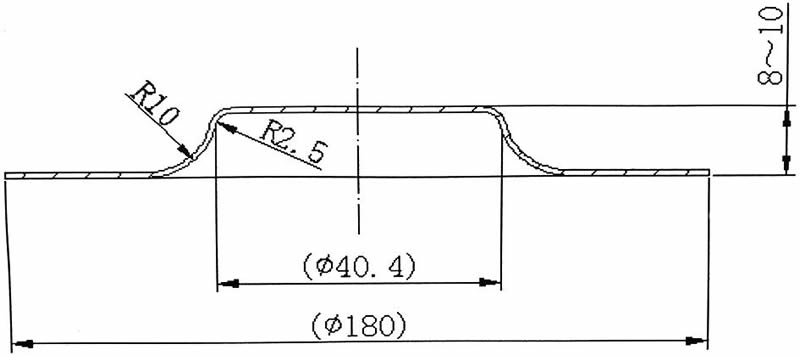
图4 初步拉深示意图
⑵二次拉深成形时,将模具设计成外凸缘有一斜角的形状,其角度为 ,凹模成形R仍采取加大的R10,此R10在外凸缘上沿圆周为φ125.3mm,中间部位的形状基本不变(图5)。
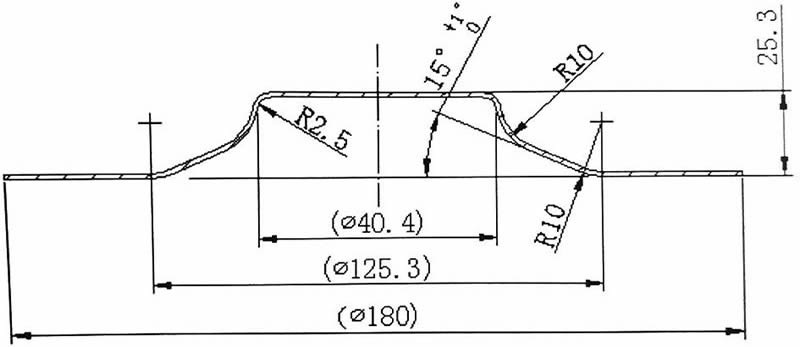
图5 二次拉深示意图
这样处理使比较容易被拉深成形的外凸缘材料能及时补充给中间拉深成形处。此次拉深后,零件高度为25.3mm,而零件的最后成形高度为18.8mm。25.3-18.8=6.5mm,多出的6.5mm高度值就为下一步成形提供了所需材料的来源。
⑶再次成形时,将φ40.4mm的凸缘R10压成R6,φ40.4mm的深度也增加到15.1mm,去掉R6,其直壁深度(包括底部R2.5mm)为9.1mm,至此中间部位φ40.4mm的拉深成形已经完成。通过模具型面可预成形到位,如图6所示。
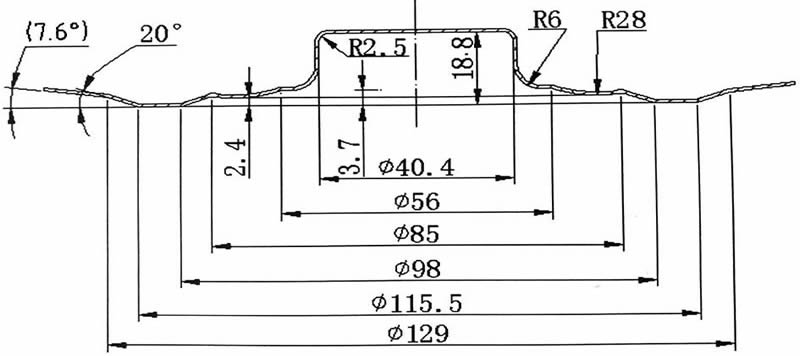
图6 型面成形示意图
在这道工序中,考虑到外凸缘的多型面,可以与中间部位的成形同时进行,只是不能进行最外面的反向拉深。因为反向拉深时材料的变形剧烈,拉深力较大,很容易使图5中φ125.3mm以内的多余材料向反向拉深处φ147.66~φ155.9mm处流动,造成R10变为R6这个地方因无材料补充而变薄或破裂。为避免此种情况发生,可将最外面的反向拉深放到最后进行,先把R6和凸缘上的型面完成。这样原来高出的6.5mm处多余的材料,能补充给R10变为R6,以及外凸缘上的多型面所需的材料,即可比较顺利地完成拉深成形。
⑷反向拉深φ155.9mm,高度不小于12mm的外缘壁。这一步反向拉深是属于正常的冲压成形工艺(图7),易实现。
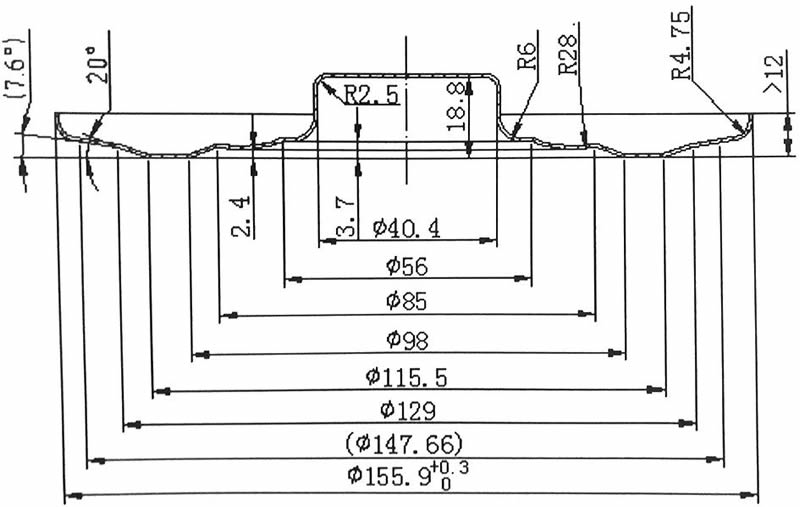
图7 外缘反拉深成形示意图
⑸将拉深成形好的零件进行车加工,去除外缘多余料。
至此,零件加工完成。
工艺优化前后对比分析
⑴成形要素对比。
现就常规拉深成形(前)与斜角过渡成形(后)比较分析如下,比较示意图如图8所示。
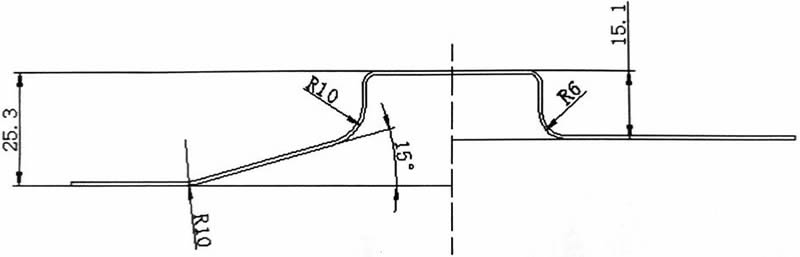
图8 优化前后方案比较示意图
1)常规拉深成形。
①沿φ40.4mm拉深处的凸缘R6,拉深深度15.1mm;
②材料曲率变化90°;
③外凸缘(毛坯)与拉深成形直径比:190(下料直径)/40.4=4.703,比值过大,不利于拉深成形,外凸缘材料抗力太大,难以向成形处流动补充。
2)采取优化后拉深。
①沿φ40.4mm拉深处的凸缘R10,拉深深度8~10mm(图4);
②R10处的材料曲率变化约45°,是正常拉深的50%,有利于成形;
③外凸缘(毛坯)与拉深成形处直径比:190(下料直径)/125.3=1.516,比值较小,加上15°的成形角,材料的变化曲率也很小,外凸缘的材料比较容易向成形处流动补充,所以较容易成形(图5)。
⑵中间过程材料分布计算对比。
在此冲压成形过程中,遵循材料体积基本相等原则,根据上述原则进行材料分析计算,材料计算对比示意图如图9所示。
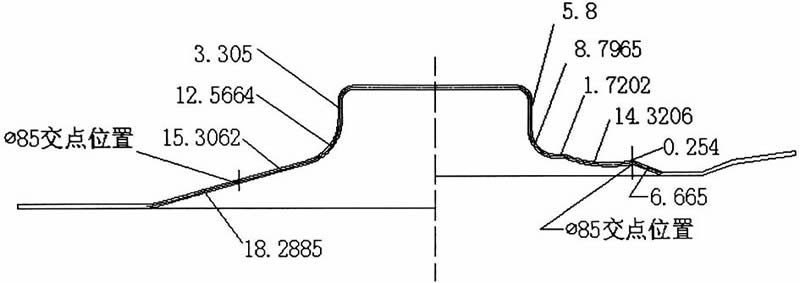
图9 优化前后方案材料分布计算比较示意图
(注:图中各段线性值均可在cad软件中测量出)
1)常规拉深(φ85mm交点处)材料展开计算。
5.8+8.7965+1.7202+14.3206+0.254=30.8913 mm
6.665-6.25=0.415mm(斜边比直边多0.415mm,需要再补充0.415mm的材料;6.25mm为6.665mm区域内投影直线长度)。
2)优化方案拉深(φ85mm交点处)材料展开计算。
3.305+12.5664+15.3062=31.1776mm
①两种方案材料差值:
31.17-30.89=0.28mm,表明优化后材料可多余0.28(φ85mm交点以内的材料);
②15°斜角材料差值:(分段计算)
15.3062-14.78=0.526mm(14.78mm为15.3062mm区域内投影直线长度);
18.2885-17.67=0.618mm(17.67mm为18.2885mm区域内投影直线长度);
0.618+0.526=1.144mm(表明斜边比直边多1.144mm);
1.144-0.415=0.729mm
通过上述计算,表明采用优化方案后,将多余的1.144mm材料补充给前面区域成形所需要的0.415mm,还剩余0.729mm可供后面凸缘的多型面成形。采取优化方案后完全能够满足零件最后成形所需要的材料。
模具结构设计
在上述成形方案中,总共需要两套模具即可完成,如图10、图11所示。
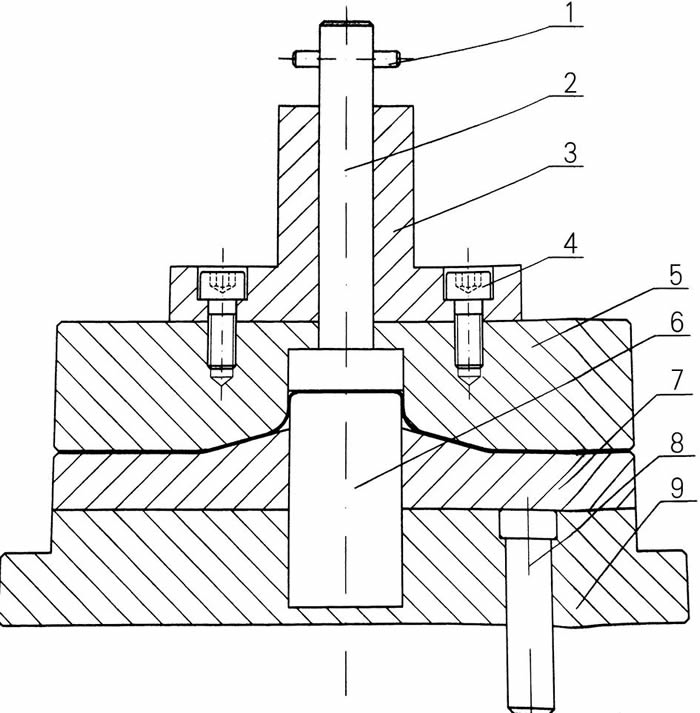
图10 预成形模结构示意图
1-横销 2-推料杆 3-模柄 4-连接螺钉 5-上模 6-凸模7-下模 8-顶杆 9-下模板
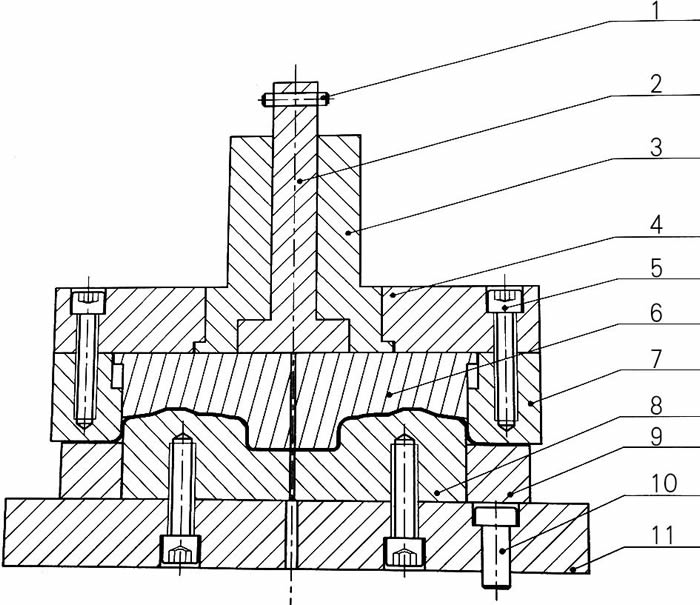
图11 成形模结构示意图
1-横销 2-推料杆 3-模柄 4-上模板 5-连接螺钉 6-内型芯7-凹模 8-凸凹模 9-压边圈 10-顶杆 11-下模板
⑴预成形模,用于浅拉深及制成斜角。
⑵成形模,用于中间部位拉深成形及最终凸缘成形。
此成形模具可做两用,在上述第三步成形中只需用内型芯及凹模,可拆去7凹模,当进行第四步外凸缘反向拉深时可用上凹模成形。
总结
通过精确数值模拟计算,采取有效的拉深途径,避免成形过程中零件破裂,产生报废,从而实现零件的批量合格生产。经过生产实践,证明大凸缘薄壁零件的冲压成形,不能直接按照常规的冲压成形方法进行加工,而要根据不同的零件情况采取相应的措施,才能达到成形目的,同时此方法也可为同类零件的加工成形借鉴使用。
|