某中低放固体废物钢桶整备方案优化及分析研究
文/贾云全
摘要:某暂存库接收了大量的来自废物产生单位的中低放固体废物钢桶(200L钢桶)在全自动化钢桶码放过程中,容易出现由于钢桶堆放不稳而产生的钢桶跌落事故,为了解决钢桶跌落问题, 本文通过设置中间盖板结构对钢桶的整备方案进行了优化设计与分析,优化方案极大地提高了暂存库的容纳能力和转运效率, 为暂存库钢桶整备方案的优化提供了新想路。
关键词: 暂存库, 中低放固体废物,200L钢桶, 跌落事故, 中间盖板
在核三废以及核设施退役环节中都会产生大量的固体废物,废物产生单位将生产过程中的固体废物装在标准的卡箍式200L钢桶内,随后送至暂存库进行整备处理、处置。当前,越来越多的中低放固体废物钢桶被送至暂存库进行整备,然而现有厂房贮存能力有限,且码放过程中跌落事故易发,因此需要优化废物钢桶的整备方案,解决钢桶跌落事故、提高厂房的容纳能力和转运效享。
1、设计原则
在暂存库的优化设计中应严格遵守国家现行的标准规范和法律法规,确保设施安全稳定运行。合理可行地提高自动控制、远距离操作技术水平,既减少操作人员的辐射剂量,又应使该设施能连续、稳定、安全、可靠的运行;充分考虑设施和设备退役的清冼去污,设备的拆除及减少污染深度, 降低放射性退役废物产生量等;高度重视厂房剂量监测及辐射防护?题,保障操作人员的辐射安全和环境安全;设计中遵循废物最小化原则, 尽可能减少各种放射性废物的产生量。
2、废物桶暂存流程及码放现状
废物产生单位将固体废物装在标准卡箍式200L钢桶内。申请得到批准后,废物产生单位将包装好的废物桶送至暂存库。废物桶由专用汽车运至暂存库后 暂存库工作人员对废物桶核查并登记接收。操作人员在控制间内打开汽车门斗大门,装有废物桶的汽车倒入汽车门斗区域。操作人员关闭汽车门斗大门之后,开启废物桶吊装孔电动盖板。根据设在遥控吊车上的摄像头以及废物桶贮存区内的摄像头,远程操作遥控吊车,通过废物桶吊装孔进行废物桶吊装操作,进行废物桶的码放操作。待车上的所有废物桶吊装完成后,关闭废物桶吊装孔电动盖板。开启汽车门斗大门,汽车驶出暂存库后关闭汽车门半大门,实现完整的贮存流程,见图1。上述过程反向操作,可实现200L废物桶从暂存库的运出。
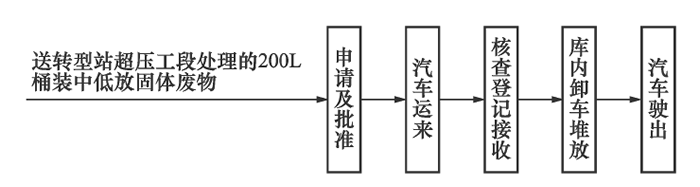
图1 废物桶贮存流程图
依据《低、中水平放射性固体废物容器钢桶》的标准要求“200L桶码放试验负载应为五个同样的钢桶”,依据相关工程经验,
一般码放设计为四层宝塔式码放。经放射性水平计算,废物桶中心距最小应保持700mm。现有厂房即把废物桶贮存区分为四个区域,各区域间采用高度为4m 的隔墙分隔,采用废物桶中心距为700mm,废物桶要求码放整齐,具体的码放情况如图2所示。
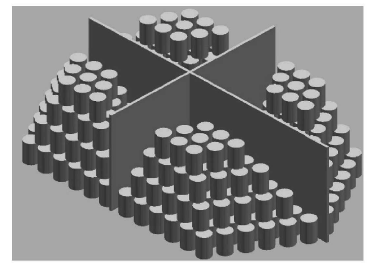
图2 废物桶码放情况
3、优化方案
3.1 废物桶码放初步设计概念
四层宝塔式码放形式在200L桶专用吊具实际抓取和吊装码放过程中,容易遇到钢桶定位不准确、堆放不稳定等问题。当码放系统累计误差值超过限定值时,操作过程中就极有可能出现钢桶跌落事故,严重影响了厂房运行效率,而且传统宝塔式码放忽视了空间利用率问题,过多浪费了上层码放空间,于是拟在每层钢桶之间设置一个中间盖板来提高钢桶码放过程中的稳定性和可靠性以及厂房空间利用率。初步设计概念见图3所示。
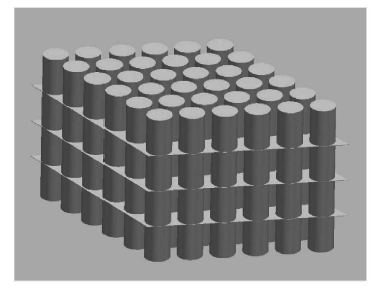
图3 废物桶码放初步概念图
设置中间盖板后:钢桶的受力情况得到改善,提高了码放稳定性;合理利用了上层码放空间,提高了厂房容量;降低了钢桶定位操作难度,极大地提升了钢桶转运效率;此外中间盖板还具备一定的辐射屏蔽防护作用。
3.2 三角形排列与正方形排列
依据废物桶中心距最小要求,本文拟两种排列方案即三角形排列和正方形排列,如图4所示。基于现有厂房面积和桁车跨度对废物桶进行模拟布排,比较分析了理想条件下两种方案的排布结果,得到如表1所示。 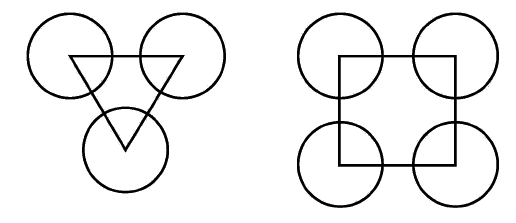
图4 三角形排列与正方形排图
表1 排列方式比较
数据结果 |
宝塔式 |
竖直式 |
排列形式 |
三角形 |
正方形 |
三角形 |
正方形 |
单位面积码放数量(个/平方米) |
7.17 |
5.18 |
12.00 |
8.67 |
比较表1数据不难发现三角形排列形式能够容纳更多的钢桶,所以本文确定采用三角形竖直码放形式为最终废物钢桶码放的优化方案。
3.3 中间盖板设计
以上数据都是基于理想条件下的结果,考虑到中间盖板吊装难易程度以及盖板的强度和刚度等实际情况,还需要进一步对中间盖板的设计进行优化。
废物桶暂存库区内200L桶的转运能够通过在厂房内设置数控吊车,配合自重式无动力抓具系统实现对废物桶抓取、码放等精确操作、实现遥控作业。所以中间盖板也应该采用200L桶专用吊具进行吊装,在最大程度上避免更换吊具的麻烦。抓头结构形式参考200L专用钢桶, 如图5所示,顶盖下表面制作成连续倒圆角形式,增大吊起过程中抓具与抓头的摩擦力,防止产生滑动位移。
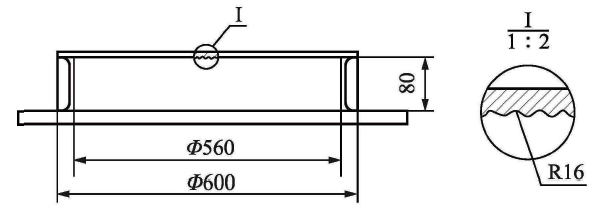
图5 中间盏板抓头结构
中间盖板抓头的设计就要求盖板上的钢桶位置减少一个,一个中间盖板上拟设计一个抓头, 原则上中间盖板面积越大抓头浪费的钢桶空间比例越小,但是钢板的面积受吊具最大承载能力(400kg)、钢板挠度、合理密排等影响不可能无限放大,所以需要对盖板的厚度和面积进行限制。
3.4 有限元软件建模与分析
对于竖直三角形码放形式考虑到合理密排,中间盖板宜采用正六边形结构。正六边形盖板可以承载覆盖7个、19个、37个钢桶,本文采用ANSYS 15.0软件分析比较了7桶、19桶、37桶模型,其中考虑到中间盖板部分为大平板问题,所以抓头和盖板分别采用SOLID 185和SHELL 281模型结构。模型结构、网格划分以及部分分析结果见图6所示。

图6 ANSYS分析模型与结果
盖板吊装过程中,正六边形边界的挠度值不应过大,过大的弯曲挠度会影响盖板下落的位置和准确性。这里我们参考工程经验,在设计过程中要求钢板的Z向挠度值不应超过10mm。有限元软件分析的盖板Z向最大挠度值如表2和图7所示。
表2 钢板Z向最大挠度
钢板厚度/mm |
挠度/mm |
9桶 |
19桶 |
37桶 |
2 |
1.1 |
15.8 |
75 |
3 |
1.5 |
20.3 |
95 |
4 |
1.4 |
18.8 |
87 |
5 |
1.1 |
15.2 |
69 |
6 |
0.9 |
5.8 |
54 |
8 |
0.6 |
7.7 |
34 |
10 |
0.5 |
7.3 |
23 |
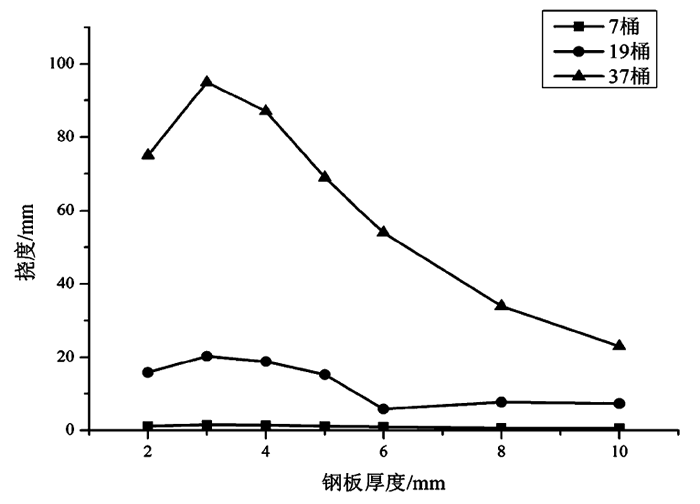
图7 Z向挠度有限元数据结果
中间盖板在起吊环节受重力和垂直加速度共同影响,为中间盖板的极限载荷工况,模拟后等效应力云图显示抓头与盖板环形焊接接头部位为局部应力极大值,是中间盖板结构的危险截面。经比较分析模拟数据可得如表3和图8所示。
表3 盖板危险截面应力(von Mises应力)
钢板厚度/mm |
压力/MPa |
7桶 |
19桶 |
37桶 |
2 |
7.4 |
33.4 |
88 |
3 |
9.6 |
42.3 |
114 |
4 |
9.3 |
44.2 |
110 |
5 |
8.8 |
40.4 |
103 |
6 |
7.9 |
25.0 |
91 |
8 |
8.7 |
39.4 |
98 |
10 |
8.5 |
39.1 |
97 |
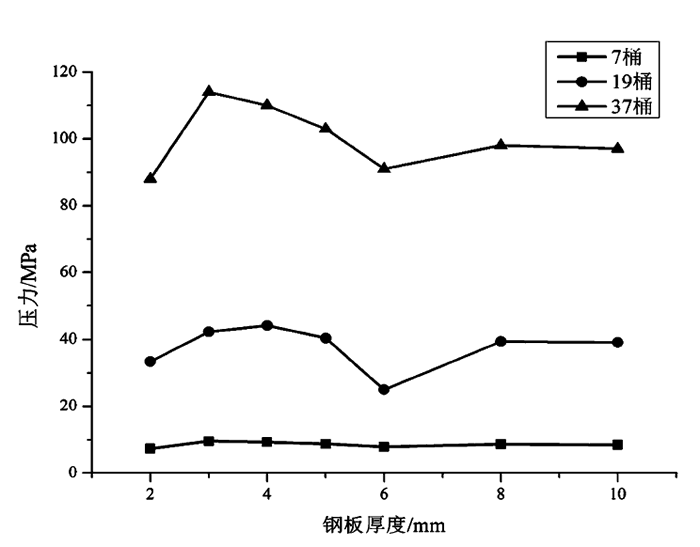
图8 危险截面von Mises应力结果
由以上图表信息分析可得:随着盖板的厚度从2~10mm不断增加,7桶和19桶模型的应力和Z向最大挠度都控制在较低的水平范围内, 37桶模型由于盖板面积过大其挠度和应力都不满足工程设计要求;7桶模型相比较于19桶模型,其抓头浪费的空间远远大于19桶模型;同时从图表中可以看出,当钢板厚度为6mm时,19桶模型的Z向挠度和危险截面等效应力同时达到极小值且满足强度和刚度的要求,所以我们最终确定6mm钢板的19桶模型为中间盖板设计的最优结构。
3.5 底层钢桶受压失稳校核
EJ 1042-2014《低、中水平放射性固体废物容器钢桶》中规定了钢桶堆码试验:对于法兰连接、螺栓固紧封盖形式的钢桶为正位立式堆码。重点考察底层钢桶的受压强度和稳定性情况。考虑码放的不稳定系数、钢桶无加强筋的厝况下,分析校核上文确定的19桶最优结构,经解析计算底层钢桶的强度和受压稳定性满足要求,底层钢桶受压失稳校核通过。
3.6 成本与效率
中低放固体废物暂存库如采用中间盖板优化方案,优化前后厂房容量对比如表4所示,优化后其容量的提升极为可观,经粗略计算中间盖板增加成本约为1万元,整体设计上符合经济性原则。
表4 优化前后厂房容量
项目 |
优化前 |
优化后 |
单位面积码放数量(个/平方米) |
7.17 |
9.36 |
4、结论
本文依据现有暂存库厂房的实际情况对所容纳的大量中、低放固体废物钢桶进行了重新码放,提出了中间盖板的结构设计,经分析论证:该结构能够使钢桶的受力情况得到改善,提高码放稳定性;合理利用上层空间,提高厂房容量;降低钢桶定位操作难度,极大地提升钢桶转运效率。经模拟分析与理论计算证明了中间盖板结构设计是合理、可靠的,在符合工程经济性原则的基础上能够极大提高暂存库容量和转运效率。本文的改进方案以及相关的分析研究为暂存库整备方案的优化提供了参考。 |