典型罩形件成形模具结构设计及试制完善
文/顾建刚
根据某典型罩形件精确工艺计算后编排的加工工序需求,合理设计拉深、翻边等冲压工序需求配备的成形模具。同时根据试制过程中出现的问题,通过理论结合实际工程经验进行分析并制定可行的改善优化措施,加强试模操作控制,达到产出合格产品的目的。
某典型罩形件为风扇转子组件的组成单件,其材料为厚度1.5mm的铝合金2A12(LY12),外形整体为拉深件,底部带有反向翻边孔。2A12为硬铝,其塑性与优质碳素结构钢及不锈钢相比较差,相应也会导致拉深成形较为困难,危险断面易裂开,给整体成形带来不便。本文主要介绍罩(XX.002)在通过精确工艺计算后编排出的冲压加工工序中需配备的拉深、翻边模具的结构设计,同时对试模过程中出现的问题进行分析,制定合理改善措施,成功完成产品试制。同时结合试制成功经验,将此类冲压制件成形模具结构方案进行推广。
产品零件结构
XX.002罩零件结构如图1所示。XX.002罩外形整体类似碗状,底部有反向翻边孔。口部最大直径为φ(154.3+0.040)mm,整体高度为61.5mm,底部反向翻边孔尺寸为φ105mm,翻边高度为6.7mm。型面由13.5mm的直边段,SR80mm的球面,翻孔自然形成的圆弧R(经计算为R6.7mm)组成。整体外形需经拉深工艺实现;底孔需后续进行翻边完成;两端面粗糙度为Ra3.2μm,可通过机械加工达到。φ(154.3+0.040)mm尺寸公差较为严格,型面轮廓度为0.5mm,需进行校形来满足使用要求。
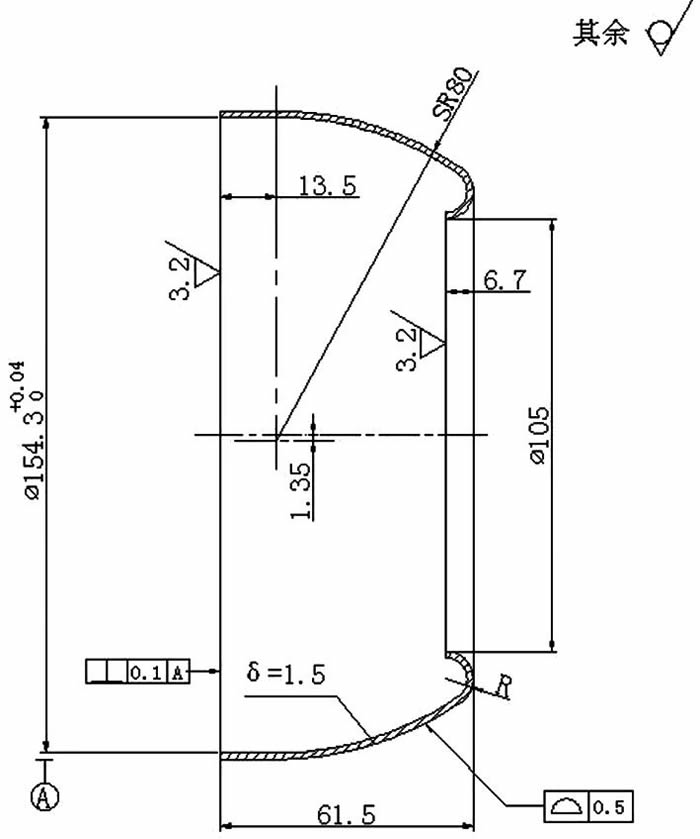
图1 XX.002罩产品图
产品成形工艺路线及模具配备
经精确工艺计算及策划分析,具体工艺路线拟为:5下料→10钳工→15冲工→20热处理→25冲工→30热处理→35冲工→40车工→45钳工→50冲工→55车工→60钳工→65热处理→70冲工→75检验。
15、25、35冲工皆为拉深工序,共用一套拉深模;20、30热处理工序皆为退火消应力、恢复塑性,方便后续拉深;50冲工为翻边工序,需一套翻边模;65热处理工序为固溶时效;70冲工工序为校形,需一套校形模。
模具结构设计及试制完善
成形工艺中需要3套模具,其中校形模结构与翻边模相似而且可简化,这里主要对其中的拉深模及翻边模共两套模具进行结构设计及要点分析,同时结合在试模过程中出现的问题及改善措施进行详述。
拉深模结构设计及试制
现根据零件拉深特点及工厂现有设备配置,成形设备选用350t液压机床。根据液压机床安装及顶出方式,拉深模结构设计如图2所示。
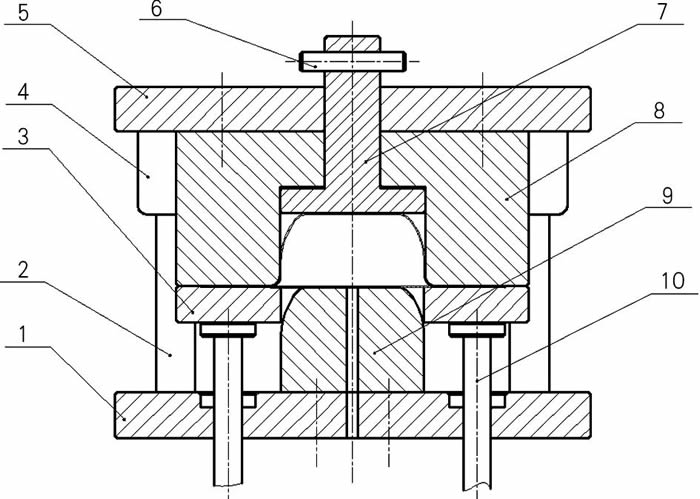
图2 拉深模结构示意图
其主要结构件为:1-下模板,2-导柱,3-压板,4-导套,5-上模板,6-固定销,7-打料板,8-凹模,9-凸模,10-顶杆,其余定位销及紧固件仅作示意。
工作原理:利用机床顶出装置将顶杆顶出,使得压板与凸模齐平,即可放置板料。机床上滑块带动凹模下压闭合,由于机床的顶出装置可施予压板一定的压边力,板料处于张紧状态,并且随着凸模慢慢顺着凹模圆角进入凹模腔成形。成形结束后,可利用打料板或压板卸出零件。
由于此种材料的拉深性能较差,拉深试制前期产生较多报废件,主要集中在危险断面(侧壁与底部R角转角处稍上部位),拉深高度未到一半即开裂,如图3所示。
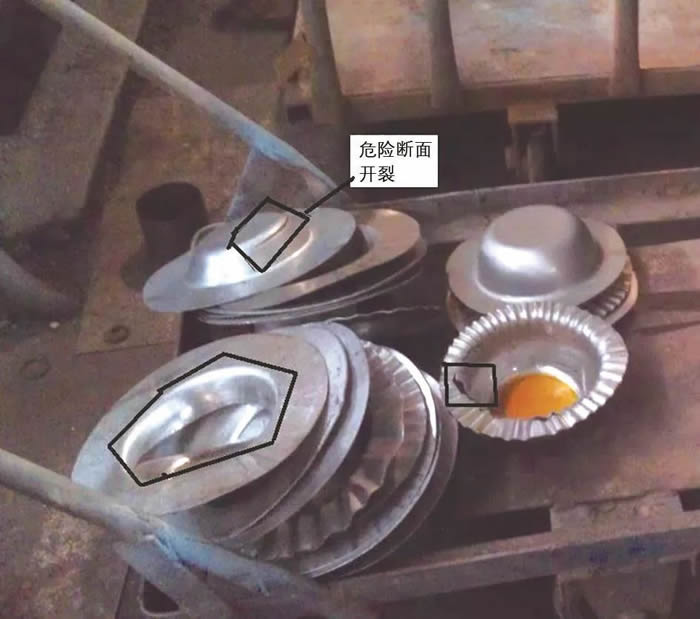
图3 半成品件开裂示意图
凸模圆角处是侧壁和底部的过渡区,材料承受侧壁较大的拉应力、凸模圆角的压力和弯曲作用而产生的压应力和切向拉应力,在这个区间的侧壁与底部转角处稍上的地方拉深开始时它处于凸、凹模间,需要转移的材料较少,变形的程度小,冷作硬化程度低,加之该处材料厚度变薄,使传力的截面积变小,成为整个拉深件强度最薄弱的地方。经分析导致零件开裂的原因主要集中于:⑴板材表面润滑性较差,不利于材料流入凹模;⑵法兰边受力过大;⑶机床滑块下滑速度过快。
解决措施:
⑴对于材料表面的润滑性主要采取涂刷润滑油和覆盖聚乙烯薄膜(最佳为0.4mm);
⑵对于压边力过大的改善需综合两方面,若单减小机床液压缸压力有可能导致法兰边受力过小导致起皱。对于此问题需综合法兰边受力面积考虑,由于在拉深过程中侧壁有所伸长,所以根据前期毛料计算足够保证总高,于是可采取在拉深过程对原板材进行修剪(直径方向上每次修去3~5mm),减小法兰边面积以达到减小受力,利于材料流入凹模腔。通过试验最终将板材初始直径修改为φ275mm;
⑶机床下滑速度则完全由人工控制,可在机床工作空间放置参照物来提供参照及限位。
改进后工作状况如图4所示。
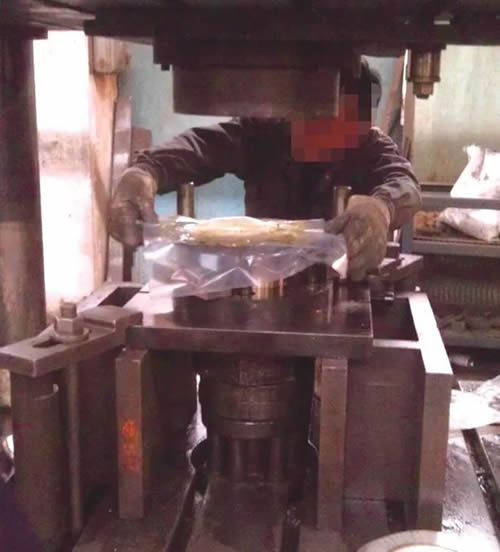
图4 改进后工作示意图
经采取如上措施后按既定工艺能顺利完成所有拉深工序的加工,并能拉出可用的半成品件。
翻边模结构设计及试制
根据40车工工序对拉深后的半成品件中间掏孔加工后的结构,翻边模结构设计如图5所示。
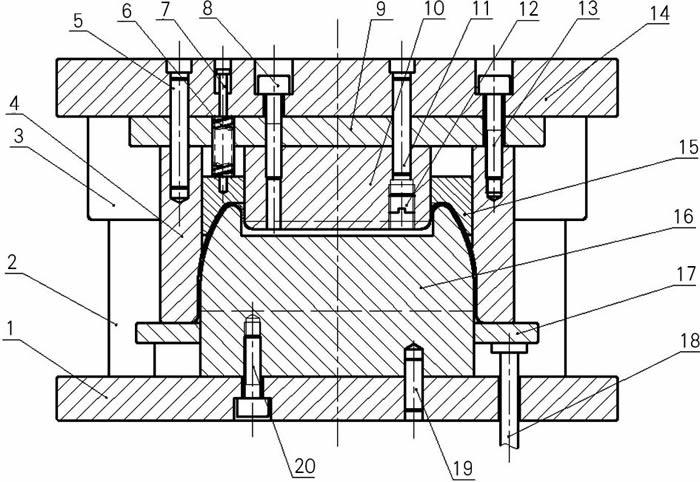
图5 翻边模结构示意图
其主要结构件为:1-下模板,2-导柱,3-导套,4-凹模,5-定位销,6-矩形弹簧,7-卸料螺钉,8-螺钉,9-垫板,10-凸模,11-定位销,12-螺堵,13-螺钉,14-上模板,15-顶块,16-定位凸模,17-推板,18-顶杆,19-定位销,20-螺钉。
工作原理:利用机床下顶出装置将顶杆顶出,使得推板上升至一定高度(不需超出定位凸模),将车加工完的半成品零件扣入定位凸模中并置于推板平面上。机床上滑块带动上模向下运动,凹模首先接触零件压紧,并与推板接触闭合一起向下运动,当达到一定高度后,顶块与零件接触并压紧零件型面,由于有矩形弹簧的存在,上模继续向下,凸模与零件底平面接触并且继续向内进行翻边,当达到指定高度后即可完成翻边工艺。当模具打开后,上顶块在矩形弹簧的作用下将零件卸出,即可取件。
设计注意要点:该模具设计时要注意在定位凸模定位零件后,利用凹模及顶块配合作用控制SR80球面材料,不让其在后续翻边时流入孔内,否则很难控制尺寸。
在前期试制过程中,由于在平底上开设的内孔尺寸取的是保守值,于是在内孔翻完保证工艺所需高度后,发现有一圈被强行扯裂的余料,如图6所示。显而易见是底孔直径开得偏小,但是如果要修改需注意不能过于加大底孔直径,如果底孔直径开得过大会导致直线段减少,翻边时模具对零件施加的力臂过小难以成形,导致回弹严重。后经测量比较,逐步试验后,底孔取得一合适值(φ95mm),并进行工艺固化。
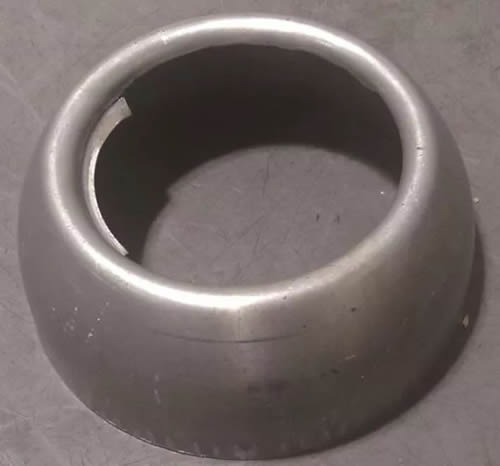
图6 翻边余料扯裂示意图
整体加工效果
经细致的工艺计算及合理安排工艺路线,同时按照工艺实施要求设计结构完善的模具等工装,通过试模及零件加工试制发现、处理问题,合理化完善,顺利加工出XX.002罩成品件,其尺寸及轮廓度要求都能满足使用要求(图7)。工艺、工装合理有效,现已投入批量生产。
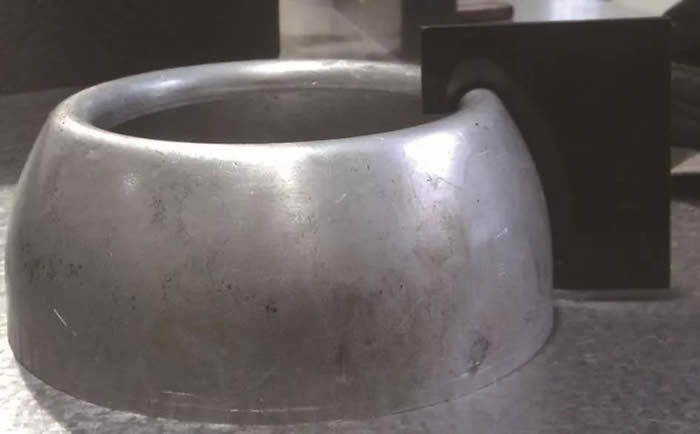
图7 XX.002罩成品件样板测量示意图
结束语
通过对冲压制件的结构进行类比分析,合理选择工厂现有设备,经济有效地完成模具结构设计。同时需注重产品试模过程中问题的发现,结合模具结构并侧重对成形过程中的材料流动性进行分析,制定系列切实可行的改善措施。本文以XX.002罩的拉深、反向翻孔等模具结构设计及试模过程中制定的系列改善措施为切入点,将典型冲压拉深件、翻边件的模具设计结构方案进行推广延伸。 |