全开口钢桶桶箍成型工艺探索(下)
辛巧娟
三、滚压成型设备
桶箍滚压成型机有两类,如图7所示。 一类为悬臂式,辊轮主轴为单边支承,是薄壁小断面成型常用设备;另一类为封闭式,主轴为双边支承:是厚壁大断面成型设备。桶箍成型一般采用前者。
作为滚压成型的辅助加工装置,常把导向滑槽、托辊、矫正、剪切等机构结合起来使其联动。
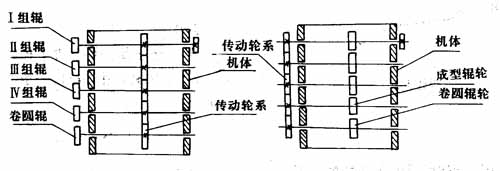
a——悬臂式滚压成型机;b——封闭式滚压成形机
图7 滚压成型机类型示意图
图8所示为常用桶箍成型机示意图。带料从滑槽1中送进,能使带料位置不致偏斜和歪移,然后通过A、B、C三道辊轮的滚压,形成所需零件的断面形状。当带料从C辊出来后遇着卷圆辊D;使条料转向上弯,由导向轨5导向卷圆成型。
滑槽1是可以调节宽度的长槽,可适用于不同宽度带料的需要;手轮2、3、4可调节A、B、C上下辊轮之间的间隙,使之适用于不同厚度的带料;手轮6可调节卷圆辊D与对辊C的距离,以实现不同直径的桶箍成型。在桶箍直径变化的同时,导向轨5也可调节。
1-定位滑槽;2-A辊调节手轮;3-B轮调节手轮;4-C辊调节手轮;5-导向装置;6-D辊调节手轮
图8 桶箍成型机示意图
四、工艺设计要点
1.主轴直径
作为成型设备设计和使用的基本出发点,与变形力呈函数关系的辊轮主轴直径常被认为是强度和尺寸的基本因素。据有关计算表明,主轴直径与板厚具有如图9所示的关系。
主轴的驱动方式有上下等速驱动、变速驱动和下轴驱动等。在辊轮的槽型设计中要注意摩擦损失。为减少辊轮和材料之间的摩擦,采用水溶性油混合液(2-10%)作为冷却润滑。
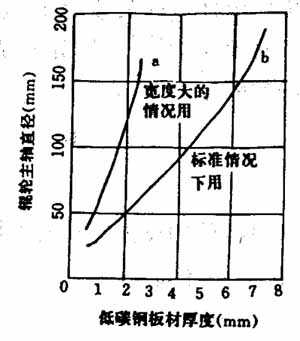
a-板料厚度与宽度比,宽度超过标准的情况;b-板料厚度t与宽度b比,t:b=1:20,此为一般标准情况
图9 滚压成型主轴直径与板厚的关系
2.零件形状
考虑所需桶箍形状的时候,首先要避免零件断面形状出现太深的沟槽。选择弯曲半径,要考虑材质的弯曲性能,避免弯曲半径过小的尖角。尖角的成型是难以达到精度要求i的。这些都是首要的基本条件。
3.断面形状的展开
设计前,要考虑所需断面的形状。接着,绘制弯曲件逐渐展开,直至回复到平板料的展开草图,然后进行分析研究。就象如图3的下图那样,把零件逆向数次展开,可看出逐渐成型的过程。这种方法,不论是对于形状简单的断面还是复杂的断面都是有效的研究方法。进而,就可以从整体上考查从一个辊轮槽型移至下一个辊轮槽型,高度方向和宽度方向的弯曲加工有无不合理的地方。
4.辊轮的组数
带料成型的最大高度h是基于以直线关系向上增加为出发点,也就是说使之在成型过程中均匀过渡。其设计方法为控制成形直边的变形角度使之匀速成型。经验表明对于一般低碳钢材料采用3。左右即可,如果边缘部分的延伸过大,则边缘容易产生皱纹。图10所示,为一U型截面的桶箍成型过程分折。如果在图中把辊轮的工位间距取为d,定出各工位上的成型高度,就可以作出断面展开图和各辊轮槽型的设计图。
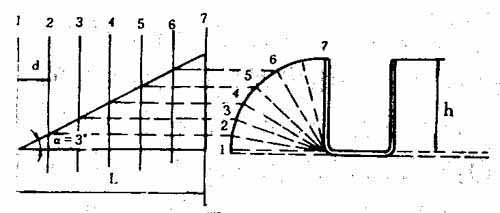
d-相邻两组辊轮的间距;L-第一组与最后一组辊轮间距;h-成型最大高度;α-成型直边的直线上升角度(解析几何)
图10 辊轮组数
辊轮组数的确定是一个困难的问题,但是对于简单断面形状的成型,如图10所示那样确定成型直边的上升角度为α,辊轮工位间距为d,成型设备的全长为L(L为第一组辊与最后一组辊的间距),那么辊轮的组数n就可以用式确定:
n=L/d=hcosα/d
5.导向线
为使板料从平板状态向前移动,直至成型出所需断面形状,就需要有水平导向线和垂直导向线。图8中所示,水平导向线从第一组辊轮开始到最后一组辊轮为止始终保持在同一水平面上,为确定成型辊轮节圆直径的基准。垂直导向线垂直于辊轮轴线,如图3中标示,是从第一组辊轮至最后一组辊轮, ,使得在此导向线两侧的成型加工量都是均等的一条基准线。在对称断面中,此导向线与断面中心线一致。
6.辊轮的节圆直径
上下辊轮一致的直径是辊轮的节圆直径。上下辊节圆由水平导向线分开,直径为上下辊中心距的二分之一,如图8中标示。
在节圆可以无滑移地送进成型材料。在此点以外的辊径上,辊轮和材料之间就要发生滑移。将辊轮节圆直径选在成型辊轮槽型的哪一点上是个重要的问题。从理想的角度出发,最好是选在辊轮受力最大的点上,但是这些点在每一组成型辊轮上是变化的。在这里,如考虑使通过第三组辊轮的水平导向线和辊轮节圆直径相一致,那么,在各组辊轮中,使节圆直径与断面形状的底面或者与断面高度的中心相重合就方便了。节圆直径的长度要在每组槽型中增加0.5-1.0%左右,朝着最后一组辊轮方向对材料给以拉伸作用,以防止弯曲和扭转。
7.带料坯的宽度
与模具弯曲的情况一样,滚压成型的坯料宽度按等于弯曲中性线的长度来计算,参看图11。
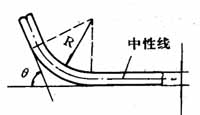
图11 弯曲弧的长度
在半径较小的弯曲部位,必须注意到中性线向受到压缩的一侧,亦即是弯曲的内侧转移。如果取中性线的长度为L,弯曲角度为θ,内侧弯曲半径为R,板厚为t,从弯曲内侧到中性线的距离为kt,则:
L= 2π(R + kt)(θ/360) =0.017458(R十kt)
中性线在板厚的1/2处时(弯曲半径大的情况),k=0.5,但是对于半径较小的弯曲,k即变为0.4~0.3。
8.辊轮槽型的间隙
在滚压成型中,板厚不会出现变厚的现象。对于弯曲部分,由于材料变薄,因此就可以取间隙等于材料的厚度。由于除辊轮节圆直径外,原则上都要发生位移,所以对于节圆直径以外的点,若取得较板厚大一些更为安全。一般取板厚的1(1/4)。此外,对于最后一组辊轮槽型以外的各中间槽型,最好是把间隙取得大一些(可加大到板厚的1/3。请参看图6。
9.防止回弹
采用过弯法,及对在精整辊轮(最后一组成型辊)槽型中的桶箍从两侧对槽型作强制加压的方法,对于限制滚压成型的回弹都是行之有效的。
10.防止表面伤痕
滚压成型中,如果坯料放置在辊轮肩部半径处(偏斜),那么,由于辊轮回转的滑移作用,就要在纵向表面上产生连续的表面伤痕。了防止这种缺陷,要把槽型作得较宽,这对将板料放进槽型的倾斜面成型,或者由侧辊轮从横向挤压都是有效的。
11.辊轮的材料
将工具钢(如T8、T10等)淬火至洛氏硬度RC60左右即可作为辊轮使用。也可以采用较软的材料,如青铜铝合金制作辊轮,能防止产生表面划伤。
五、成型桶箍件常见缺陷分析
1 .刮痕
桶箍表面的局部地方出现光亮印痕,有时在滚压过程中还伴随着从桶箍表面刮下来的飞刺和屑末,破坏了桶箍表面质量,引起桶箍局部变薄。产生的主要原因是辊轮边缘角太小,或磨损后不光滑,或间隙太小,或上下,辊轮槽位置偏移所致。
2.划痕
在桶箍上产生表面划痕可能是直线的,可能是曲线的。产生的原因是辊轮表面状态不良,或速度太小不合理。
3.裂纹
裂纹发生在弯曲处。产生的原因是材料塑性差,工作圆角半径太小,或弯曲角太小所致。
4.条纹
周期性出现在桶箍表面上的清晰条纹,虽手摸无明显感觉,但涂漆后复盖不住。产生的原因是桶箍转动阻力太大,速度不均匀,桶箍与辊轮之间出现瞬时打滑现象。
5.偏斜
滚压过程中出现的偏斜现象,致桶箍两侧宽度不一致,时常还伴随着桶箍的扭曲。产生的原因是滚压成型过程中,桶箍定位不稳,摆动所致。产生原因是各组辊轮未调整在同一水平导向线上,或辊轮在轴上左右窜功等。
相关链接:全开口钢桶桶箍成型工艺探索(上)
|