制桶冲压自动生产中的监测装置(1)
文/贾苛珍
钢桶生产中,很多零件都是冲压加工的,如桶底、桶顶、封闭器、提环、提环座等等。在高生产率的钢桶零件冲压自动生产过程中,单靠操作人员来看管生产过程,发现和处理事故及废次品的产生,无论在精神上和体力上都是很大的负担。若采用各种监视和检测装置代替操作人员,监视冲压有关环节,以实现生产过程中的自动保护,保证有条不紊地、稳定正常生产,才是科学的方法。
图1所示为冲压自动生产各个环节中,具有各种监视机能的检测装置。它们的功能和应用场合简述如下:
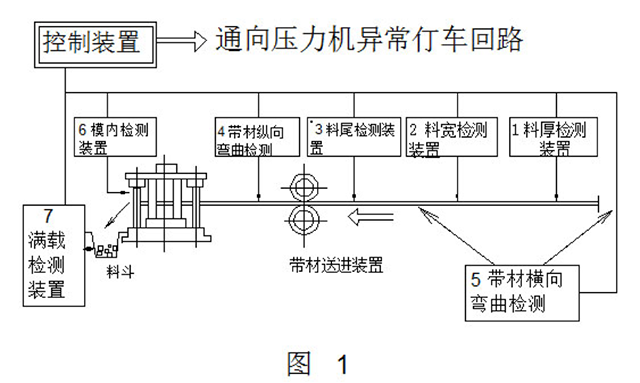
1、料厚检测
该检测在一般情况下不大使用,但在材料厚度误差较大或冲制精密零件时有必要使用。
2、料宽检测
在少、无废料冲压中,当使用原宽度带材料时,则需进行宽度检测。当采用多工位模具冲压时,常常采用侧刃切边送进,这时,进行带材横向弯曲(蛇形)的检测较之带材宽度检测更为有利。
3、料尾检测
带材到达末端时进行显示,并立即停止压力机运转是很重要的工作,它告知操作人员需添新料,便于多机床管理。
4、带材纵向弯曲检测
当某一工位模具发生故障时,下一个坯料就不能送进,在这种情况下如再次冲压时,带材送进受阻碍,便会出现纵向弯曲。故纵向弯曲是因模具事故引起的暴露在带材表面的最典型的缺陷。
5、带材横向弯曲检测
当冲压料厚较大时,如果带材因横向弯曲严重而不能通行时,就会出现很多废品,不仅如此,而且它还将成为模具损坏的原因。
6、模内检测
该检测不仅作为模具保护所需,此外还可检验制件精度和质量。
7、成品贮存料斗满载检测
这是采用料斗或者排列制件的方法进行入仓的。假如这个部分不加检测,制则将溢出料斗外,而造成不必要的事故。
检测装置的传感方式,有接触式及无接触式两种。前者主要通过机械方式使电触头动作,后者通过电磁感应、光电或β射线等取得信号。
信号分两类:一类是直接从检测装置的信号(导通或切断)就可以判别有无故障;另一类信号必须与冲压工作循环的特定位置或时刻相联系,才能判别有无故障。一旦故障发生,信号便通向压力机异常停车回路。
下面简要介绍各种监视和检测装置的典型结构和作用原理。
一、机电式检测装置
1、料厚检测
对允许公差要求严格的制件,其料厚检测较复杂。在需进行正规检验的情况,可采用金刚石针接触式检测。
图2所示夹板式料厚检测法有现场实用价值。电测部分与夹持材料部分以支点为中心形成较大的杠杆比,因此可以进行相当精确的检测。图中,当夹持材料的端部钢球间通过薄料时,接触端子相接触并将输入信号送至控制装置。假如事先按照这种状态调节接触端子,则在厚料通过时,就向控制装置发送输出信号。
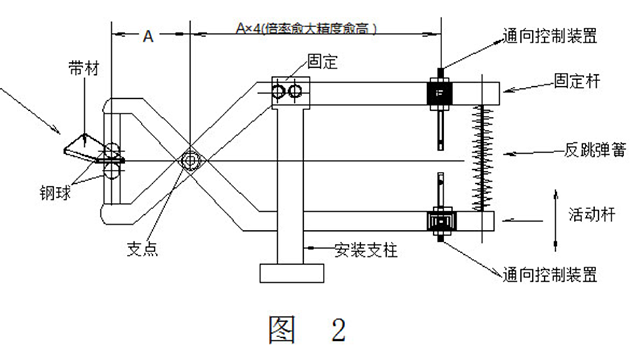
2、料宽检测
该检测方法不复杂。图3为该检测装置的一个例子,如图中所示,当带有辊子的L型杆其端部左右移动时,与A或B限位开关相接触,从而接通控制回路。
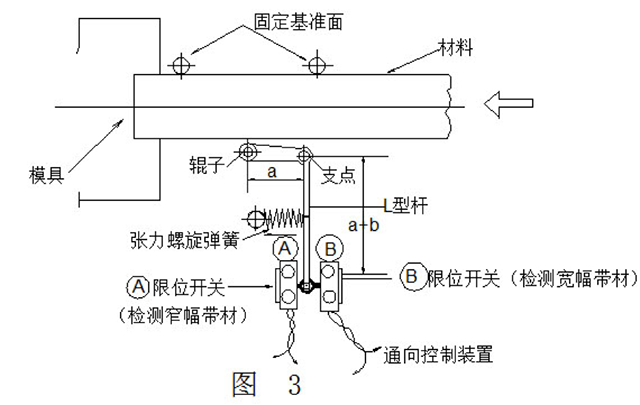
该检测法也可利用杠杆比将实际的微小尺寸加以放大。限位开关可进行微调,预先把介于带材宽度最大和最小允许公差之间的基本规格的板料置于基准面与辊子之间,以此来调节限位开关。
带材尺寸宽时B限位开关接通,宽度过小时,在装在臂上的张力螺旋弹簧作用下,A限位开关接通,同时向控制装置发出输入信号,使压力机停止运转。
3、料尾检测
一般采用图4所示的自动压力机本身所带的检测装置进行检测较多,但在使用气动送料器或在压力机后边设送料器(即拉式送料器)时,就必须考虑设置如图5的特制料尾检测装置。在带有支点的杠杆一侧设置常分限位开关,另一侧设置杆或辊子。为使带材在通过时能够借助辊子给杠杆以张力,应把固定支架移到进料口安装。当带材到达末端时,由于失去张力而使杠杆处于自由状态,这时输入信号就送到控制装置。
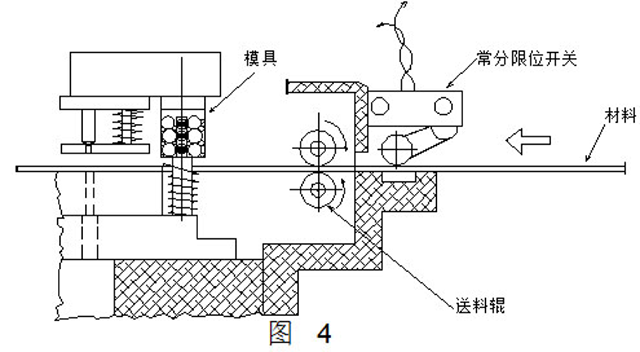
料尾检测装置上使用常分限位开关较好。原因是,如果控制开关在平时带电,而一旦发生异常情况时(指已到达带材末端),只需给出切断回路的输入信号即可,这样就可避免回路断线及开关误操作等事故。压力机在没有检测、保护回路的情况下不允许运转,这是最可靠的方法。
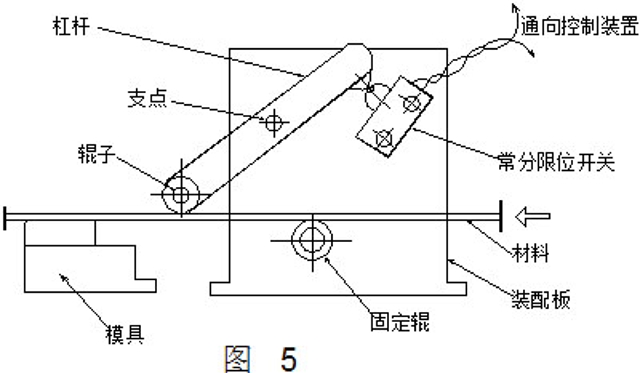
图6为自动卷筒。这是为送进带材而配置的,该装置可配合压力机的加工速度自动送进材料。卷筒配有电动机,它是应用了在检测装置部位被送进的带材过多时就引起带材松弛的原理。
当松弛的带材与下面的棒接触时,卷筒的电动机开关就断开,电动机便停止转动。但经一段时间带材拉紧后就与上面的棒接触,从而使电动机接通,此时卷筒旋转,带材被送进,依此反复进行。
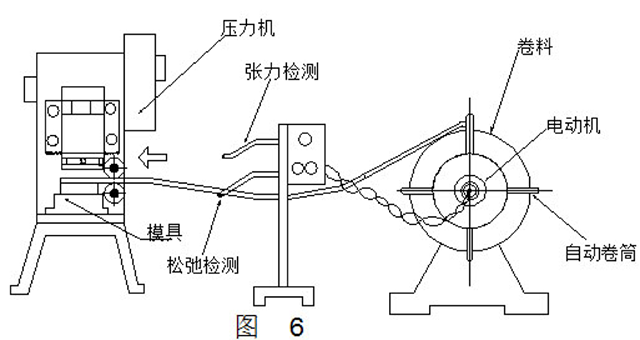
4、带材纵向弯曲检测
如前所述,带材纵向弯曲是模具内发生的种种异常现象最明显的暴露,因此,较其它检测更重要。
图7为带材发生纵向弯曲的情况,图8为对此采取的措施,该装置很简单,但重要的是如何把装置设在效果最好、而且在发生异常时最易起拱的地方,这就需要对模具进行仔细观察。
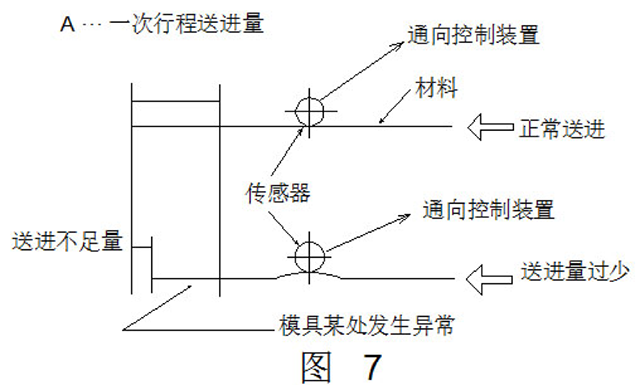
不消说的是,在每一次短距离送进或冲压厚带材时,往往纵向弯曲不显著,尚须进一步研究如何获得相应的精度。此外,由于一般带材原来多少都有些拱曲,因而有时会无缘故发现带材碰触接触端子,并使压力机停止运转的情况。因此,在检测装置处宜使用导板,以使带材尽可能保持平整。
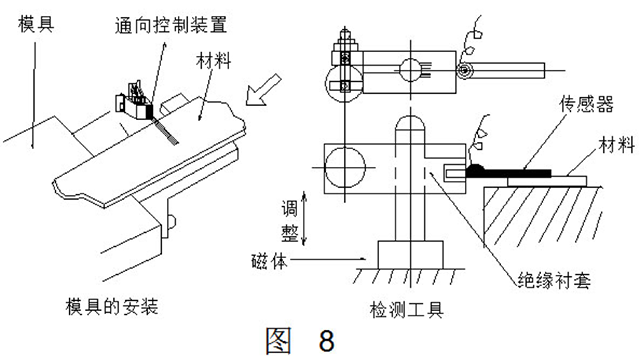
5、带材横向弯曲检测
为节约原材料,板形检测是不可缺少的项目。一般通过顺序送进,在多工位模具中切掉带材边部(侧刃修边)可达到修正的目的。但对于横向弯曲严重的情况会不可避免地损坏价格昂贵的模具。
图9所示为板形检测的实例。该例只适用于带材为导体材料,对非导体材料不适用。须注意之点是,在距离模具多远的地方放置传感器进行检测为宜。
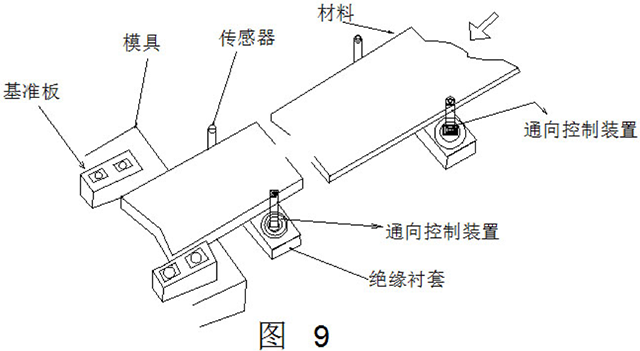
6、模内检测
模内检测包括材料送进或工序件定位是否准确;凸模是否折断;顶件装置工作是否正常;出件是否流畅等,这类检测装置形式很多,这里介绍几个典型例子。
(1)定位检测法
采用图10的定位加工时,在定位部分设置传感器,这样只有当材料送进到顶定位置,并接触传感器,压力机滑块才向下冲压。一旦送进步距不足,材料便不接触传感器,滑块也就不能下降。
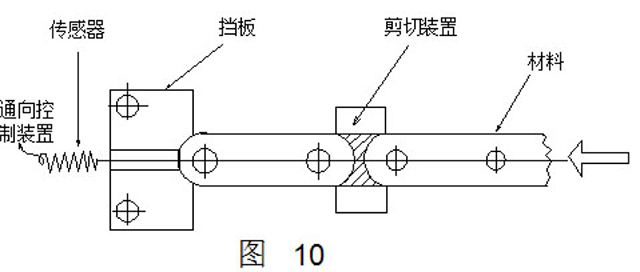
(2)自动挡销检测法
该检测法利用杠杆以支点为中心左右移动的原理(见图11)。当带材顶到头时,在自动挡销的作用下,带材每次与传感器相碰,当不碰触时可认为带材尚未被送进好,从而压力机也就不能工作。
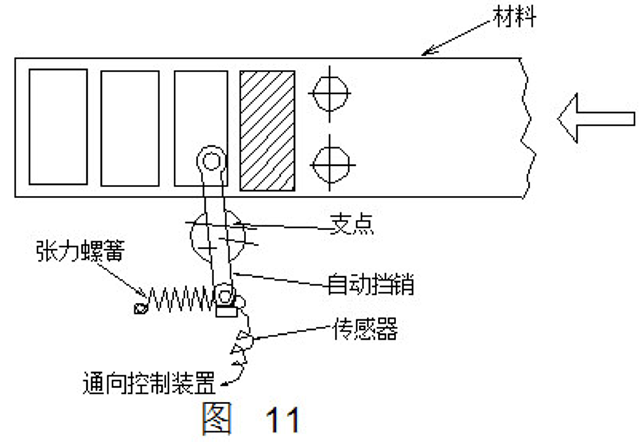
(3)导电销检测法
该检测法是利用废料孔检测每次送料是否准确,该检测装置设在下模内(见图12)。导电销由绝缘套绝缘,销的顶端略小于废料孔,当带材通过上方时,导电销瞬时与带材接触而线路导通,但当导电销顶出下一个孔时线路就切断,每一工作周期依次循环地向控制装置发出导通和切断的输入信号。

图13示出一个工作循环图。发出误送进时就出现如图中D那样导电销不顶出的情况,由于导电销与带材仍保持接触,线路处于接通状态。图14为正常情况与误送进时导电销检测输入信号图,当送进量不当或完全没有送进时,检测装置就能操纵压力机滑块停止工作。
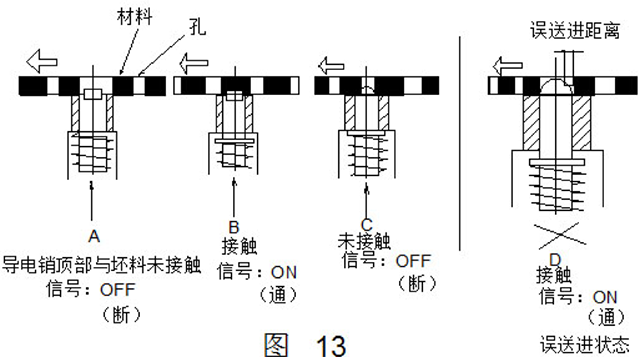
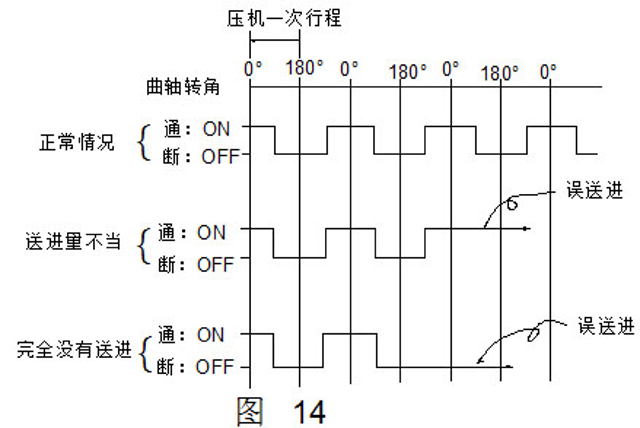
为使导电销能顺利出入于带材废料孔,要求销的直边部分不应高出凹模上平面,故此法的检测精度受此影响,为进一步提高检测精度,可采用图15所示的高精度杆检测法。该法中导电销不是依据带材而移动,而是每次通过装在压力机上的定时凸轮发出的气路启闭信号来自动运动的。因此,该法导电销的直边部分即使进入带材废料孔内也并不防碍。由于销径与废料孔径可以接近,从而能够高精度地检测定距送进的误差。
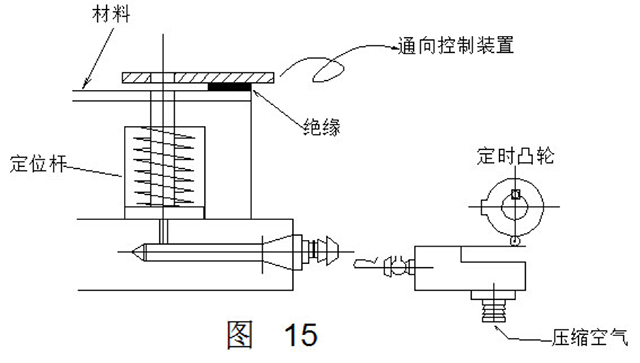
该方法与其说是单纯的送进误差检测,倒不如说具有检查制件质量的机能。
【相关链接】
制桶冲压自动生产中的监测装置(1)
制桶冲压自动生产中的监测装置(2)
|